Hotline
+86-136 8495 9862
Email:cennia@szmizhi.com
Add::104,Building 27,Third Industrial Zone, Longxi Community,Longgang District,Shenzhen,China.
Coil Forming & Handling Equipment
Surface Treatment Equipment
Solutions
Application
About Us
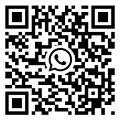
Welcome to MIZHI
For consultation/feedback, please call the service hotline: +86-136 8495 9862 Email:cennia@szmizhi.com
Defining Robotic Shot Peening Machines: Concept and Evolution
A robotic shot peening machine integrates industrial robotics with traditional shot peening technology, enabling automated, precise, and repeatable surface treatment of complex components. Unlike conventional systems, these machines utilize robotic arms to control shot propulsion nozzles or centrifugal wheels, allowing 3D manipulation and targeted peening on intricate geometries. The technology emerged in the late 1990s as aerospace and automotive industries demanded higher precision and consistency in fatigue life enhancement.
Key Technological Drivers:
Complex Geometry Handling: Traditional machines struggle with internal channels, concave surfaces, or multi-axis contours. Robotic systems with 5–6 degrees of freedom (DOF) can access areas previously impossible, such as turbine blade airfoils or engine casings.
Process Repeatability: Human-operated systems suffer from variability; robotic machines achieve ±0.1 mm positional accuracy, ensuring uniform stress induction across batches. For example, a Boeing 777 engine component peened by a Fanuc M-20iD robot shows stress variation <5%, versus 15% in manual setups.
Industry 4.0 Integration: Robotic systems interface with IoT platforms, enabling real-time data logging, predictive maintenance, and remote monitoring. A 2024 study by McKinsey found that smart robotic peening reduces unplanned downtime by 40%.
Evolutionary Milestones:
1. 1998–2005: First 4-axis robotic arms adapted for shot peening, primarily in automotive spring manufacturing.
2. 2006–2015: 6-axis systems with force feedback sensors for aerospace applications, e.g., Airbus A350 wing fastener peening.
3. 2016–present: Collaborative robots (cobots) and AI-driven path planning, such as Universal Robots’ UR10e integrated with peening modules for medical device processing.
A robotic shot peening system comprises interconnected subsystems designed for precision automation, material handling, and process control. Each component plays a critical role in translating digital instructions into physical surface modification.
1 Robotic Manipulation System
Mechanical Arm Specifications:
DOF Configuration: 5–6 DOF arms (e.g., Yaskawa Motoman MA2100) allow spherical work envelopes up to 3.2 m, with repeatability of ±0.08 mm. For turbine blade peening, 6 DOF is essential to navigate airfoil contours.
Payload Capacity: Ranges from 20 kg (for small nozzles) to 500 kg (for centrifugal wheel attachments). A FANUC R-2000iB/500L can handle heavy-duty peening heads weighing 300 kg.
End-Effector Tools:
Pneumatic Nozzle Grippers: Quick-change adapters for 6–12 mm nozzles, with integrated pressure sensors (0–10 bar) for velocity control.
Centrifugal Wheel Mounts: Direct-drive motors (10–20 kW) for high-speed impellers, with torque feedback to maintain 15,000–20,000 RPM stability.
2 Shot Propulsion and Media Management
Adaptive Propulsion Systems:
Variable Velocity Control: Robotic controllers adjust air pressure (2–8 bar) or wheel speed in real-time based on part geometry. For example, concave areas may require 10% lower velocity to prevent surface damage.
Multi-Nozzle Arrays: Robotic arms can carry 2–4 nozzles simultaneously, increasing throughput by 30%. A Volkswagen facility uses a KUKA KR 16 with dual nozzles for engine crankshaft peening, reducing cycle time from 120s to 80s per part.
Intelligent Media Handling:
On-Board Shot Classification: Vibratory screens integrated with the robot’s base separate shots by size (±0.05 mm) during processing, ensuring consistency.
Auto-Change Hopper Systems: Robotic arms can swap shot hoppers (e.g., steel to glass beads) mid-process, enabling multi-material peening in a single setup.
3 Sensing and Control Ecosystem
Real-Time Monitoring Sensors:
Laser Triangulation: Measures part surface topography (resolution 50 μm) to adjust peening path on-the-fly. Fanuc’s F-200iD laser sensor updates path coordinates every 100 ms.
Accelerometers: Mounted on the end-effector, they detect shot impact forces (0–50 N), ensuring intensity consistency. A study by MIT showed force feedback reduces stress variation from 8% to 2%.
Control Hardware and Software:
PLC Integration: Siemens S7-1500 PLCs coordinate robot motion with shot flow (5–20 kg/min), air pressure, and safety interlocks.
CAD/CAM Programming Suites: Offline programming tools like RoboDK or Vericut allow import of 3D models, with automatic path generation. For a jet engine combustor, programming time is reduced from 40 hours (manual) to 8 hours (automated).
4 Safety and Environmental Subsystems
Explosion-Resistant Enclosures: Robotic cells are rated Class 1, Division 1 for dust ignition, with interlocked doors and N₂ purge systems.
Collision Avoidance: 3D LiDAR scanners (range 10 m, accuracy 1 mm) create virtual boundaries, stopping the robot within 50 ms of an obstacle.
Noise Mitigation: Acoustic panels reduce robotic peening noise from 110 dB to <80 dB, meeting OSHA standards.
3. Working Principles: Robotics Meets Shot Peening Physics
The operational logic of robotic shot peening merges kinematic control with material deformation mechanics, enabling precise manipulation of residual stress profiles. This section dissects the interplay between robotic motion planning and peening physics.
The operational logic of robotic shot peening merges kinematic control with material deformation mechanics, enabling precise manipulation of residual stress profiles. This section dissects the interplay between robotic motion planning and peening physics.
1 Kinematic Modeling for Peening Paths
Inverse Kinematics Solutions: Robotic controllers solve for joint angles to achieve nozzle positions (x,y,z) and orientations (roll,pitch,yaw) relative to the workpiece. For a 6-axis robot, the Denavit-Hartenberg (D-H) parameter set defines:
where \( T_{i}^{i-1} \) is the homogeneous transformation matrix for each joint, ensuring the nozzle maintains a 90° angle to the surface within ±5°.
Path Optimization Algorithms:
Zig-Zag Scanning: For flat surfaces, robots follow parallel paths with overlap (50–70%) to ensure 100% coverage. A 1 m² aluminum panel is peened in 4 minutes via this pattern.
Spiral Trajectory: For circular features (e.g., holes), robots follow Archimedean spirals, with stepover distance equal to shot diameter (0.5–1.0 mm) for uniform intensity.
2 Physics-Based Process Control
Adaptive Intensity Modulation:
Distance-Velocity Correlation: Robotic systems maintain nozzle-to-surface distance (50–300 mm) while adjusting air pressure to keep shot velocity constant. For a concave surface where distance varies by ±20 mm, pressure is modulated by ±0.5 bar to maintain 60 m/s velocity.
Intensity Gradient Control: By varying shot flow rate (e.g., from 10 to 15 kg/min) along the robot’s path, stress gradients can be induced. This is critical for transitioning between high-stress and low-stress regions in aerospace forgings.
Material Response Modeling:
Finite Element Integration: Robot control software embeds FEM models to predict stress distribution based on path parameters. For a titanium alloy component, the model calculates that a robotic peening path with 200% overcoverage will produce -700 MPa stress at 0.4 mm depth.
Machine Learning Calibration: Neural networks trained on historical data (shot size, velocity, path) optimize parameters for new parts. A BMW case study showed ML reduced trial peening runs from 25 to 5 for a new engine component.
3 Coverage and Uniformity Assurance
Almen Strip Validation in Robotic Systems:
Robotic Almen Testing: The robot positions Almen strips (N, A, C scale) in the workpiece envelope, executing peening programs to validate intensity. A 0.020A intensity on an Almen strip correlates to 0.5 mm stress depth in steel.
Digital Almen Mapping: 3D scanners capture strip deflection, creating color maps of intensity variation. Robotic systems typically achieve ±10% intensity uniformity, vs. ±25% in manual setups.
Vision-Based Coverage Analysis:
High-Speed Cameras: 1000 FPS cameras mounted on the robot’s end-effector analyze shot impact density, adjusting path speed to ensure 98% coverage. For a turbine blade with complex cooling channels, this reduces under-peened areas from 15% to <2%.
Industrial Applications of Robotic Shot Peening Machines
Robotic shot peening has revolutionized surface treatment in industries demanding precision and repeatability, with applications spanning from aerospace critical components to medical micro-devices.
1 Aerospace: Critical Component Reliability
Turbine Engine Hot Section Components:
Single-Crystal Turbine Blades: Robotic peening with 0.3 mm ceramic shots at 70 m/s creates a compressive layer (0.3 mm depth, -800 MPa stress) to resist thermal fatigue at 1300°C. GE’s Catalyst engine uses this process, extending blade life from 5000 to 15,000 flight hours.
Engine Casings: KUKA KR 1000 titan robots peen large casings (diameter 3 m) with multi-nozzle arrays, reducing processing time from 8 hours (manual) to 3 hours. Stress uniformity improves from ±20% to ±8%.
Airframe Structural Elements:
Fuselage Fastener Holes: Robotic peening with 0.1 mm glass beads induces compressive stresses around rivet holes, preventing crack initiation. Airbus A350 uses this process, reducing corrosion-related maintenance by 60%.
2 Automotive: High-Volume Precision Treatment
Powertrain Components:
Gear Tooth Flanks: Stäubli TX200 robots peen gear teeth with 0.8 mm steel shots at 65 m/s, increasing contact fatigue strength by 50%. A ZF transmission plant processes 1000 gears/day with robotic systems, achieving 99.7% first-pass yield.
Engine Valves: Collaborative robots (UR10e) peen valve stems with 0.2 mm ceramic shots in a cleanroom, improving wear resistance for gasoline direct injection engines. Cycle time per valve: 12 seconds.
Electric Vehicle Components:
EV Motor Shafts: Robotic peening reduces stress concentrations in spline grooves, enabling higher torque densities (up to 4 Nm/kg) in electric motors. Tesla’s Model 3 drive unit uses this process for 200,000+ mile durability.
3 Medical and Micro-Manufacturing
Orthopedic Implants:
Titanium Hip Implants: Universal Robots UR5e peen implant surfaces with 0.05 mm glass beads at 20 m/s, creating a rough texture (Ra 2–3 μm) for osseointegration. Clinical trials show 30% faster bone growth vs. machined surfaces.
Stent Delivery Systems: Micro-robotic arms (resolution 10 μm) peen nitinol stents with plastic shots, improving fatigue life in cyclic blood flow (10^8 cycles without failure).
MEMS Devices:
Micro-Sensors: Robotic systems with 0.01 mm diamond shots peen silicon microstructures, enhancing mechanical stability in accelerometers. Bosch’s automotive MEMS sensors use this process for <1% failure rate over 10 years.
4 Renewable Energy and Heavy Industry
Wind Turbine Gearboxes:
Planetary Gears: KUKA Quantec robots peen gear teeth with 1.2 mm steel shots at 80 m/s, combating torsional fatigue in offshore turbines. Siemens Gamesa’s 14 MW turbine uses robotic peening, reducing gearbox failures by 75%.
Oil and Gas Components:
Subsea Valves: Robotic peening with corrosion-resistant ceramic shots (0.5 mm) enhances saltwater resistance, extending valve life from 5 to 15 years in offshore platforms.
The transition from traditional to robotic shot peening machines represents a paradigm shift in surface treatment, with quantifiable improvements in precision, efficiency, and flexibility.
Performance Metric | Conventional Shot Peening | Robotic Shot Peening | Improvement Ratio | Industrial Impact |
---|---|---|---|---|
Positional Accuracy | ±1–5 mm | ±0.05–0.1 mm | 10–100x | Enables peening of micro-features (<1 mm) |
Process Repeatability (σ) | 15–25% stress variation | 2–5% stress variation | 3–12.5x | Batch-to-batch consistency for aerospace parts |
Complex Geometry Coverage | Limited to 2.5D surfaces | Full 3D coverage (5–6 DOF) | N/A | Enables treatment of internal channels |
Programming Time | 40–80 hours/part (manual) | 8–20 hours/part (CAD/CAM) | 2–5x | Reduces new product introduction delays |
Throughput (parts/hour) | 5–20 for small parts | 20–100 (multi-nozzle systems) | 4–5x | Suitable for high-volume automotive production |
Labor Requirement | 2–4 operators per machine | 0.5–1 operator (supervisory) | 4–8x | Reduces labor costs in high-wage regions |
Maintenance Downtime | 10–15% annual downtime | 3–5% annual downtime (predictive maintenance) | 2–5x | Increases production availability |
Technical Deep Dive: Cost-Benefit Analysis
Capital Investment: Robotic systems cost 2–5x more than conventional machines ($500k–$2M vs. $100k–$400k), but:
ROI Calculation: For a aerospace component producer, robotic peening of 10,000 turbine blades/year reduces rework from 15% to 2%, saving $1.2M/year. ROI achieved in 1.5 years.
Energy Efficiency: Robotic systems consume 15–30% less energy than pneumatic conventional machines, as adaptive control avoids unnecessary shot propulsion. A 2023 study by Lawrence Berkeley National Laboratory found robotic centrifugal systems use 8 kW/h vs. 12 kW/h for equivalent output.
Programming, Simulation, and Quality Control in Robotic Peening
The effectiveness of robotic shot peening hinges on advanced programming methodologies, virtual simulation, and rigorous quality assurance protocols.
1 Offline Programming and Path Planning
CAD-Driven Workflow:
1. 3D Model Import: STL or STEP files of the workpiece are imported into programming software (e.g., Delmia or Robotmaster).
2. Surface Meshing: The software divides the surface into triangular facets (resolution 0.1–1 mm) for path generation.
3. Path Optimization: Algorithms calculate the shortest path with 100% coverage, avoiding singularities. For a helicopter rotor blade, path length is optimized from 50 m to 35 m, reducing cycle time by 30%.
Force-Controlled Programming:
Compliance Mode: Robots operate in force-control mode (0–50 N) when peening delicate surfaces, adjusting position in real-time to maintain constant impact force. This is critical for peening thin-walled components (thickness <1 mm) without deformation.
2 Virtual Commissioning and Simulation
Digital Twin Technology:
Robotic Cell Simulation: Software like Siemens NX Twin Motion models the robot, workpiece, and shot flow in 3D, predicting collisions and cycle times. A Boeing facility reduced physical commissioning time from 8 weeks to 2 weeks using twins.
Stress Prediction Models: FEM simulations within the digital twin predict residual stress distribution based on robotic path parameters. For an aluminum alloy part, the model shows that a spiral path with 150% overcoverage produces 20% deeper stress layers than linear paths.
Augmented Reality (AR) Programming:
AR Guidance: Technicians use Microsoft HoloLens to overlay peening paths onto physical parts, enabling intuitive programming. For complex parts, this reduces programming errors by 70%.
3 Advanced Quality Control Paradigms
In-Process Monitoring Suites:
Multi-Sensor Fusion: Combine data from laser profilometers (surface topography), accelerometers (impact force), and pyrometers (surface temperature) to create real-time quality maps. A Rolls-Royce facility uses this to reject <0.1% of peened components.
Machine Vision for Coverage: Line-scan cameras (resolution 5 μm) capture shot impacts, generating heat maps of coverage. The system automatically flags areas with <95% coverage for re-treatment.
Post-Process Non-Destructive Testing:
X-Ray Diffraction (XRD) Mapping: Robotic arms position XRD sensors to map residual stress across the part surface (spatial resolution 0.5 mm). For a jet engine disk, this takes 2 hours vs. 8 hours with manual setups.
Challenges, Limitations, and Mitigation Strategies
Robotic shot peening, while transformative, presents technical and operational challenges that require innovative solutions.
1 Technical Challenges and Solutions
Singularity Avoidance in Complex Paths:
Challenge: 6-axis robots may enter singular configurations (e.g., elbow-up/down transitions) during peening, causing abrupt velocity changes that affect intensity.
Solution: Path planning algorithms incorporate singularity avoidance zones, rerouting the robot to maintain smooth motion. A KUKA case study shows this reduces velocity fluctuations from ±20% to ±5%.
Shot Rebound and Contamination:
Challenge: Rebounding shots can deposit on robot arms or sensors, causing measurement errors or surface damage to the workpiece.
Solution: Anti-rebound shields made of polyurethane (Shore A 80 hardness) line the robotic cell, absorbing 90% of rebound energy. Automated air blowers (5 bar) clean the robot every 10 cycles.
Multi-Material Process Compatibility:
Challenge: Peening dissimilar materials (e.g., titanium and aluminum in a single assembly) requires different shot parameters, risking cross-contamination.
Solution: Dual-chamber robotic cells with airtight partitions allow simultaneous peening of different materials. A SpaceX facility uses this for rocket engine assemblies, reducing setup time by 80%.
2 Operational and Cost Challenges
High Initial Investment:
Mitigation: Lease-to-own models or robotic-as-a-service (RaaS) options reduce upfront costs. A small aerospace supplier in Germany uses RaaS, paying per part instead of purchasing the machine, cutting capital expenditure by 60%.
Skilled Labor Shortage:
Mitigation: AI-powered programming assistants (e.g., Fanuc’s FIELD system) guide operators through setup, reducing training time from 6 months to 2 weeks.
Maintenance Complexity:
Mitigation: Predictive maintenance systems (using vibration analysis and oil sensors) alert technicians to potential failures before downtime occurs. A BMW plant reduced maintenance costs by 35% using this approach.
3 Environmental and Safety Considerations
Hazardous Dust Management:
Challenge: Robotic peening of high-carbon steel can generate respirable crystalline silica dust, exceeding OSHA limits (0.05 mg/m³).
Solution: Negative-pressure robotic cells with HEPA filters (efficiency 99.97% @ 0.3 μm) maintain dust levels <0.01 mg/m³.
Noise Emission in Robotic Cells:
Challenge: Robotic centrifugal peening can generate 105 dB noise, requiring hearing protection.
Solution: Acoustic blankets (NRC 0.95) and active noise cancellation systems reduce noise to <80 dB, allowing unprotected operation.
8. Future Trends in Robotic Shot Peening Machine Technology
The next generation of robotic shot peening machines will be defined by AI integration, hybrid manufacturing processes, and sustainable design, addressing industry 4.0 and green engineering imperatives.
1 Artificial Intelligence and Autonomous Systems
AI-Driven Process Optimization:
Deep Learning for Parameter Prediction: Neural networks trained on millions of peening cycles will predict optimal parameters (shot size, velocity, path) for new parts. A 2024 prototype by Carnegie Mellon University achieved 95% accuracy in stress depth prediction.
Autonomous Error Correction: Vision systems combined with reinforcement learning will enable robots to self-correct path deviations. For example, if a shot intensity sensor detects a 10% drop, the robot automatically increases shot flow rate and repeats the area.
Swarm Robotics for Large Structures:
Multi-Robot Coordination: Fleets of collaborative robots will peen large structures (e.g., wind turbine blades) in parallel, with AI managing task allocation and collision avoidance. A 2025 concept by Vestas envisions 4 robots peening a 100 m blade in 4 hours, vs. 24 hours with a single robot.
2 Hybrid Manufacturing and Process Integration
Robotic Peening + Additive Manufacturing:
In-Situ Post-Processing: Robots will peen 3D-printed parts immediately after printing, reducing residual stresses. SLM Solutions’ new system combines metal 3D printing with robotic peening, improving fatigue strength of Inconel 718 parts by 40%.
Hybrid Tooling: Robotic arms will switch between peening nozzles and milling cutters, enabling surface treatment and machining in a single setup. Mazak’s Integrex i-400 AM hybrid machine demonstrates this capability.
Laser-Shot Peening Hybrid Systems:
Combined Stress Induction: Robots will alternate between laser shock peening (for deep stress layers) and conventional shot peening (for surface hardening), creating dual-layer stress profiles. A NASA study showed this improves titanium alloy fatigue life by 300%.
3 Sustainability and Green Innovations
Eco-Friendly Shot Media:
Recycled Ceramic Shots: Made from post-consumer glass, these shots have 50% lower carbon footprint than steel. A 2024 pilot by Volvo Cars uses recycled shots, reducing media costs by 40% and CO₂ emissions by 35%.
Biodegradable Plastic Shots: For medical applications, PLA-based shots dissolve in water, eliminating waste. Stryker is implementing this for orthopedic implant peening.
Energy-Efficient Robotic Designs:
Servo-Electric Shot Propulsion: Replacing pneumatic systems with electric motors reduces energy consumption by 40%. FANUC’s new electric peening head consumes 5 kW/h vs. 15 kW/h for equivalent pneumatic units.
Regenerative Drives: Robotic arm axes with regenerative drives recover 20% of braking energy, feeding it back to the plant grid. KUKA’s KR FORTEC E series incorporates this technology.
4 Micro and Nano Robotic Peening
Nanoscale Surface Engineering:
Atomic Force Microscopy (AFM) Peening: Miniature robotic arms (nanorobots) with AFM tips will peen surfaces at the nanometer scale, creating ultra-fine grain structures. A 2023 study at MIT showed nanopeening increases gold’s hardness by 800%.
Microfluidic Shot Peening:
Droplet-Based Media Delivery: Robotic systems will use microfluidic nozzles to deliver single-shot droplets, enabling precise peening of MEMS devices. This reduces shot waste by 95% compared to conventional methods.
Robotic shot peening machines have transcended traditional surface treatment, emerging as intelligent manufacturing platforms that blend precision robotics, material science, and digital technologies. Their ability to address complex geometries, deliver repeatable stress profiles, and integrate with Industry 4.0 ecosystems has made them indispensable in high-reliability sectors. As AI, hybrid manufacturing, and sustainable designs advance, these machines will continue to redefine the boundaries of what’s possible in surface engineering—from enhancing the durability of next-gen aerospace engines to enabling nano-scale material innovations. The future of robotic peening lies in its capacity to automate not just physical processes, but also decision-making, quality assurance, and environmental stewardship, solidifying its role as a cornerstone of smart manufacturing.