Hotline
+86-136 8495 9862
Email:cennia@szmizhi.com
Add::104,Building 27,Third Industrial Zone, Longxi Community,Longgang District,Shenzhen,China.
Coil Forming & Handling Equipment
Surface Treatment Equipment
Solutions
Application
About Us
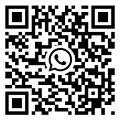
Welcome to MIZHI
For consultation/feedback, please call the service hotline: +86-136 8495 9862 Email:cennia@szmizhi.com
In the industrial landscape of 2025, sand blasting machines have evolved into indispensable tools for surface preparation, material finishing, and heavy-duty cleaning. Unlike their commercial or portable counterparts, industrial-grade sand blasters are engineered to handle large-scale operations, continuous use, and rigorous environmental demands. These machines form the backbone of industries ranging from automotive manufacturing to aerospace, shipbuilding, and heavy equipment maintenance. This article delves into the technical specifications, operational principles, advanced features, and market trends that define industrial sand blasting machines, exploring how they address the unique challenges of high-volume, precision-driven industrial applications.
1 High-Pressure Compressed Air Systems
Industrial sand blasters rely on robust compressed air systems capable of generating pressures ranging from 80 to 150 PSI (pounds per square inch), far exceeding the capacity of commercial units. These systems typically integrate dual-stage air compressors with oil-free or oil-lubricated designs, depending on the application’s sensitivity to contamination. For example, in aerospace component processing, oil-free compressors are mandatory to prevent residue on critical parts. The compressed air is stored in large-capacity tanks (often 100+ gallons) to ensure a consistent flow, which is essential for maintaining uniform abrasive velocity during prolonged operations.
The air stream is directed through heavy-duty hoses and valves designed to withstand high pressures and abrasive wear. Specialized pressure regulators and gauges allow operators to fine-tune the air pressure, while flow control valves manage the volume of abrasive media, creating a precise balance between cleaning efficiency and surface integrity. This system is particularly critical in applications like removing thick rust layers from steel structures or preparing castings for coating, where inconsistent pressure can lead to uneven surface treatment.
2 Advanced Abrasive Delivery Systems
Industrial machines feature sophisticated abrasive delivery mechanisms, primarily categorized into two systems: direct pressure (pot blasting) and siphon (suction) blasting. Direct pressure systems, the preferred choice for heavy-duty tasks, use a sealed pressure pot to store abrasive media. Compressed air enters the pot, forcing the abrasive through a hose to the nozzle at high velocity. This method delivers a more powerful blast, ideal for removing tough coatings, scale, or weld slag from large metal surfaces.
Siphon systems, while less powerful, offer precision and are suitable for delicate industrial applications. They use the Venturi effect created by the compressed air stream to draw abrasive from a hopper into the nozzle. This design is commonly seen in industries requiring controlled surface finishing, such as preparing aluminum components for anodizing or deburring intricate parts.
3 Integrated Dust and Fume Control Systems
Industrial sand blasters prioritize safety and environmental compliance through advanced dust extraction systems. These systems often combine cyclonic separators, HEPA filters, and baghouse collectors to remove up to 99.97% of airborne particles as small as 0.3 microns. For example, in steel fabrication plants, where silica dust poses significant health risks, dual-stage filtration systems first use cyclonic separation to capture larger particles, followed by HEPA filters to trap fine dust.
Additionally, some machines incorporate wet blasting technology, mixing abrasive media with water to suppress dust at the source. This not only reduces air pollution but also minimizes wear on machine components, extending operational life. Wet blasting is increasingly popular in industries near urban areas, where strict air quality regulations limit dry blasting operations.
1 Conveyor - Fed Automatic Sand Blasters
Conveyor-fed systems are the workhorses of high-volume manufacturing. These machines feature an endless conveyor belt that transports workpieces through an enclosed blasting chamber. Multiple fixed nozzles, strategically positioned above and below the conveyor, direct abrasive streams at the parts, ensuring uniform coverage. Programmable Logic Controllers (PLCs) manage conveyor speed, nozzle pressure, and abrasive flow, allowing precise control over the blasting process.
In automotive component production, for instance, these machines can process hundreds of parts per hour, removing casting flash or preparing surfaces for powder coating. The enclosed chamber design minimizes dust exposure, while automatic abrasive recycling systems collect and filter used media, reducing waste and operational costs. Some advanced models even integrate robotic arms within the chamber to manipulate complex parts, ensuring all surfaces are treated thoroughly.
2 Rotary Table Sand Blasters
Ideal for batch processing of circular or symmetrical parts, rotary table sand blasters feature a rotating platform that holds workpieces. The table spins within a blasting booth, while stationary or articulated nozzles direct abrasives at the parts from multiple angles. This design is common in industries producing gears, flanges, or engine components, where uniform surface treatment is critical.
Rotary tables can accommodate varying part sizes, from small brackets to large engine blocks, with adjustable fixtures securing the workpieces. Some models include multiple tables that rotate independently, enabling continuous operation as one batch is loaded/unloaded while another is being processed. This increases throughput in industries like heavy equipment manufacturing, where downtime must be minimized.
3 Monorail and Overhead Rail Systems
For large, irregularly shaped workpieces—such as ship hull sections, aircraft fuselage components, or industrial tanks—monorail and overhead rail sand blasters offer versatile solutions. These systems suspend parts from a moving rail, transporting them through a blasting tunnel equipped with fixed or robotic nozzles. The rail can be programmed to move the workpiece at a controlled speed, while nozzles adjust their position and angle to target specific areas.
In shipbuilding, these machines are used to remove marine growth and rust from hulls before applying anti-corrosive coatings. The overhead design allows for the treatment of ultra-long components without the need for manual handling, improving safety and efficiency. Advanced models may integrate 3D scanning technology to map the workpiece’s geometry, enabling the blasting system to adjust automatically for varying surface profiles.
4 Custom - Engineered Industrial Sand Blasters
Many industries require specialized sand blasting solutions tailored to unique needs. Custom-engineered machines may include features like hermetically sealed chambers for processing hazardous materials, explosion-proof components for volatile environments, or cryogenic blasting capabilities for temperature-sensitive materials. For example, in the nuclear industry, sand blasters may be designed with lead-lined chambers to contain radioactive dust, while in the aerospace sector, machines might use inert gases instead of compressed air to prevent oxidation during blasting.
These custom systems often involve collaboration between equipment manufacturers and end-users to address specific challenges, such as treating heat-sensitive composites or achieving microscopic surface roughness for adhesive bonding. The design process may include finite element analysis (FEA) to optimize nozzle placement and airflow, ensuring both efficiency and precision.
Industrial Applications: Where Sand Blasting Machines Excel
1 Metal Fabrication and Foundry Operations
In metal fabrication, industrial sand blasters are essential for preparing raw materials and finished parts. For example, after casting, sand blasters remove core sand, scale, and surface imperfections from iron and steel components. The abrasive process also improves the surface roughness, enhancing the adhesion of paints, primers, or protective coatings. In structural steel manufacturing, large-scale sand blasters clean and prepare beams and plates for welding or galvanizing, preventing corrosion in outdoor infrastructure projects.
Foundries use specialized sand blasters to deburr complex castings, such as engine blocks or pump housings. The high-velocity abrasive stream can reach intricate cavities and recesses that manual cleaning cannot access, ensuring parts meet dimensional tolerances. Additionally, sand blasters are used to remove excess material from investment castings, a process critical for aerospace and medical device components where precision is non-negotiable.
2 Aerospace and Defense Manufacturing
The aerospace industry demands the highest standards of surface treatment, and industrial sand blasters deliver precision and consistency. Aircraft components, from turbine blades to landing gear, undergo blasting to remove heat-treated oxides, prepare surfaces for plating, or enhance fatigue resistance. Specialized abrasives, such as glass beads or ceramic particles, are used to achieve specific surface finishes without damaging the base material.
In defense manufacturing, sand blasters are used to refurbish military equipment, removing battle damage, rust, and old coatings from tanks, ships, and aircraft. The process must be efficient to minimize downtime while maintaining the structural integrity of critical components. Some military applications even use mobile industrial sand blasters that can be deployed in the field, enabling on-site maintenance in remote locations.
3 Shipbuilding and Marine Engineering
Ship hulls and offshore structures face constant exposure to saltwater, making corrosion prevention paramount. Industrial sand blasters are used to achieve the high surface cleanliness and roughness required for marine coatings, often following standards like ISO 8501-1 (Sa2.5 or Sa3). These machines can handle the massive surface areas of ships, removing barnacles, rust, and old paint in a fraction of the time required by manual methods.
Marine engine components, such as propellers and heat exchangers, also undergo blasting to remove marine growth and scale. In offshore oil and gas platforms, sand blasters prepare steel structures for protective coatings, extending their lifespan in harsh environments. The industry often uses wet blasting systems to minimize dust in confined shipyard spaces, improving worker safety and compliance with environmental regulations.
4 Heavy Equipment and Machinery Maintenance
Industrial sand blasters play a crucial role in maintaining heavy machinery, such as construction equipment, mining trucks, and agricultural vehicles. When components like hydraulic cylinders, chassis frames, or engine components become coated in grease, dirt, or rust, sand blasting efficiently restores them to a clean state. This not only improves aesthetics but also allows inspectors to identify cracks or wear that might otherwise be hidden.
In mining operations, where equipment is exposed to abrasive soils and harsh conditions, sand blasters are used to remove built-up debris and prepare parts for repair or reconditioning. The process is particularly important for extending the life of expensive components like excavator buckets or conveyor rollers, reducing replacement costs and downtime.
1 IoT - Enabled Smart Sand Blasting Systems
The integration of Internet of Things (IoT) technology has revolutionized industrial sand blasting. Smart machines are equipped with sensors that monitor parameters like air pressure, abrasive flow, nozzle wear, and dust concentration in real time. This data is transmitted to a central dashboard, allowing operators to track performance, predict maintenance needs, and optimize settings remotely.
For example, if a sensor detects a drop in abrasive flow, the system can automatically adjust the feed rate to maintain consistent blasting performance. IoT systems also enable predictive maintenance by analyzing wear patterns on components like nozzles or hoses, alerting maintenance teams before a failure occurs. In large manufacturing plants, this connectivity allows managers to coordinate multiple sand blasters, balancing workloads and maximizing efficiency.
2 Robotic Automation and AI Integration
Industrial sand blasters are increasingly paired with robotic arms to achieve precision and consistency in complex applications. Robots can navigate intricate part geometries, adjusting nozzle distance and angle to ensure uniform treatment. Artificial Intelligence (AI) algorithms can be trained to recognize different part types and automatically select the optimal blasting parameters, eliminating human error.
In automotive plants, robotic sand blasters can treat complex body panels with varying curvatures, ensuring each surface receives the correct amount of abrasion. AI can also analyze post-blasting surface scans to verify quality, flagging parts that require re-treatment. This level of automation not only improves product consistency but also reduces reliance on skilled labor, addressing workforce shortages in some industries.
3 Eco - Friendly Abrasives and Energy Efficiency
As environmental regulations tighten, industrial sand blasters are adopting sustainable practices. Biodegradable abrasives made from recycled glass, corn cobs, or walnut shells are replacing traditional silica sand, reducing health risks and environmental impact. These materials offer similar performance to silica while being non-toxic and easier to dispose of.
Additionally, energy-efficient designs have become standard. High-efficiency air compressors, variable speed drives, and automated shut-off systems reduce power consumption during idle periods. Some machines even incorporate heat recovery systems, capturing and reusing the heat generated by compressors to warm facilities or other processes, further improving energy efficiency.
4 Advanced Safety and Ergonomic Features
Industrial sand blasters now prioritize operator safety with features like pressurized blasting helmets with HEPA-filtered air supply, reducing exposure to dust. Automated door interlocks and emergency stop systems prevent accidental activation, while light curtains or laser scanners detect human presence in the blasting area, halting operations immediately.
Ergonomic designs also enhance operator comfort in manual blasting applications. Lightweight composite hoses, adjustable nozzle grips, and vibration-dampening handles reduce fatigue during long shifts. In enclosed systems, climate-controlled operator cabins with noise reduction features create a safe and comfortable working environment, improving productivity and reducing turnover.
Industrial Sand Blasting: Key Considerations for Implementation
1 Selecting the Right Abrasive Media
Choosing the appropriate abrasive is critical to achieving desired results. Factors such as material hardness, particle size, and shape influence the blasting outcome. For example:
Steel Shot/Grit: Used for heavy-duty cleaning and surface roughening on steel, cast iron, and other hard metals.
Glass Beads: Ideal for delicate surfaces, producing a smooth, satin finish without excessive material removal.
Aluminum Oxide: Extremely hard, suitable for removing tough coatings or preparing surfaces for bonding.
Walnut Shells: Soft, biodegradable, and used for cleaning delicate parts without scratching, such as wood or plastic.
Industrial operators must also consider abrasive recycling. High-quality abrasives can be reused multiple times in closed-loop systems, reducing costs. However, contaminated or worn abrasives must be replaced to maintain blasting efficiency.
2 Compliance with Safety and Environmental Regulations
Industrial sand blasting is subject to strict regulations, particularly regarding dust exposure and hazardous materials. In the U.S., the Occupational Safety and Health Administration (OSHA) sets permissible exposure limits (PELs) for respirable crystalline silica, while the European Union enforces regulations under the Industrial Emissions Directive.
To comply, companies must implement engineering controls (e.g., dust extraction), provide personal protective equipment (PPE), and conduct regular air monitoring. For hazardous applications—such as removing lead-based paint—additional precautions like negative pressure chambers and specialized PPE are essential. Failing to comply can result in fines, legal liabilities, and damage to worker health.
3 Maintenance and Lifecycle Management
Industrial sand blasters require routine maintenance to ensure optimal performance. Key maintenance tasks include:
Inspecting hoses and nozzles for wear and replacing them periodically.
Cleaning and replacing filters in dust collection systems.
Servicing air compressors, including oil changes and valve inspections.
Checking pressure pots and abrasive feed systems for clogs or leaks.
Developing a preventive maintenance schedule can extend machine lifespan and reduce unexpected downtime. Some manufacturers offer maintenance contracts, providing trained technicians and genuine parts to ensure equipment reliability. Lifecycle management also involves evaluating when to upgrade to newer, more efficient models, balancing initial investment with long-term operational costs.
1 Growth in Emerging Industrial Sectors
As emerging economies invest in infrastructure and manufacturing, the demand for industrial sand blasters is rising. Countries in Southeast Asia, Africa, and Latin America are establishing automotive plants, steel mills, and shipyards, driving adoption of advanced blasting technology. Additionally, renewable energy sectors, such as wind turbine manufacturing, are using sand blasters to prepare tower components and turbine blades for coating, creating new market opportunities.
2 Integration with Industry 4.0
The Fourth Industrial Revolution is transforming industrial sand blasting through digitalization. Machine-to-machine (M2M) communication, big data analytics, and cloud-based monitoring systems are becoming standard. This integration allows for real-time process optimization, remote diagnostics, and predictive maintenance, aligning sand blasting operations with smart factory initiatives.
3 Focus on Cost Efficiency and Sustainability
Industrial operators are increasingly prioritizing total cost of ownership (TCO) when selecting sand blasters. Machines with lower energy consumption, longer component life, and efficient abrasive recycling systems offer better ROI.同时, sustainability initiatives are driving the adoption of eco-friendly abrasives and energy-saving designs, as companies seek to reduce their carbon footprint and meet ESG (Environmental, Social, Governance) goals.
4 Rise of Mobile and Modular Solutions
For on-site industrial maintenance, mobile sand blasting units are gaining popularity. These self-contained systems, often mounted on trailers, include air compressors, abrasive storage, and dust collection, enabling operators to perform blasting tasks at remote locations. Modular industrial systems, which can be expanded or reconfigured as pr
Industrial sand blasting machines have evolved from simple surface cleaners to sophisticated, technology-driven systems essential for modern manufacturing and maintenance. Their ability to handle large-scale, precision tasks across diverse industries—from aerospace to shipbuilding—makes them indispensable tools for ensuring product quality, durability, and compliance. As technology continues to advance, integrating IoT, robotics, and sustainable design, industrial sand blasters will only become more efficient, versatile, and critical to global industrial operations. For companies seeking to optimize production, maintain equipment, or comply with strict standards, investing in cutting-edge industrial sand blasting technology is not just a choice but a necessity in the competitive landscape of 2025 and beyond.