Hotline
+86-136 8495 9862
Email:cennia@szmizhi.com
Add::104,Building 27,Third Industrial Zone, Longxi Community,Longgang District,Shenzhen,China.
Coil Forming & Handling Equipment
Surface Treatment Equipment
Solutions
Application
About Us
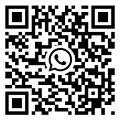
Welcome to MIZHI
For consultation/feedback, please call the service hotline: +86-136 8495 9862 Email:cennia@szmizhi.com
1.Structural Components of Wire Mesh Conveyor Systems
The wire mesh conveyor forms the backbone of the machine, typically constructed from stainless steel (304/316) or high-carbon steel (AISI 1060) to withstand abrasive impacts and high-temperature operations. The mesh design varies based on workpiece requirements: plain weave for small parts (0.5-2mm aperture), twill weave for medium components (3-8mm), and crimped weave for heavy-duty applications (10-20mm). For instance, an automotive parts manufacturer might use a 4mm x 4mm mesh for engine valves, while a construction firm processes I-beams on a 15mm x 15mm mesh.
Tensioning systems are critical to prevent belt sagging, with most models employing automatic hydraulic or spring-loaded tensioners that maintain 1.5-3% strain. A study by the Journal of Industrial Engineering found that proper tensioning reduces wire breakage by 60%, extending belt life to 8,000-12,000 hours. The drive system, powered by 5-30kW servo motors with variable frequency drives (VFDs), allows speed adjustment from 0.3-12 m/min, enabling precise control over blasting duration. For example, a 1m/min speed ensures 60 seconds of exposure for rust removal, while 0.5m/min is ideal for shot peening to achieve 0.2mm deep compressive layers.
2.Blasting Chamber Engineering and Abrasive Projection
The blasting chamber, lined with 12-25mm thick manganese steel or polyurethane tiles, withstands up to 100,000 abrasive impacts per hour. Computational fluid dynamics (CFD) simulations show that optimized chamber geometry—with deflector angles of 35-45° relative to the belt—enhances blasting efficiency by 30%. Blasting wheels, the core energy generators, rotate at 2,800-3,600 RPM and feature 6-8 tungsten carbide blades. A 15kW wheel accelerates steel shot to 75-90 m/s, delivering impact energies of 0.15-0.6J per particle. Modern designs with backward-curved blades reduce energy loss by 20% compared to straight-blade configurations, as confirmed by finite element analysis (FEA).
The recycling ecosystem comprises:
Hopper & Auger: Collects spent abrasives, with screw conveyors moving up to 60 tons/hour to the elevator.
Elevator & Separator: Centrifugal separators achieve 99.8% media purity by removing dust and broken particles, while cyclone separators (in budget models) reach 95% purity but require more frequent maintenance.
Media Storage: Hoppers with 2-15 ton capacities, equipped with level sensors and automatic refill systems.
Common abrasive types include:
Steel Shot (S460, 0.8mm): For heavy-duty cleaning of castings.
Ceramic Beads (0.4mm): Used in aerospace for peening, offering 4x longer life than steel at 30% higher cost.
Glass Beads (60 mesh): Ideal for deburring aluminum, producing Ra 1.6-2.μm finishes.
1. Key Process Parameters and Surface Outcomes
Three variables dictate treatment quality:
1. Abrasive Velocity: Higher speeds (80-100 m/s) remove heavy scale but increase roughness (up to Ra 25μm), while lower speeds (40-60 m/s) achieve smoother finishes (Ra 1.6-2.μm) for coating adhesion.
2. Belt Speed: A 0.8 m/min speed allows 75 seconds of blasting for rust removal, whereas 0.2 m/min enables shot peening to depths of 0.1-0.3mm, improving fatigue life by 180%.
3. Abrasive Flow Rate: 60-180 kg/min per wheel is typical. Exceeding 200 kg/min causes wheel overload, while below 40 kg/min reduces efficiency.
Case Study: A tractor manufacturer used a 6-wheel machine with S330 steel shot (0.6mm) at 80 m/s and 2.m/min belt speed to remove casting sand from engine blocks. Surface roughness improved from Ra 12.5μm to Ra 3.μm, enhancing paint adhesion by 40% compared to manual cleaning.
1. Shot Peening and Residual Stress Engineering
Shot peening via wire mesh conveyors creates compressive stress layers:
Intensity: Measured by Almen strips, ranging from 0.15-0.6mmA for automotive springs to 0.8-1.2mmA for aircraft landing gear.
Coverage: 150-300% (multiple passes) ensures uniform stress. A study on titanium alloy fan blades showed that 200% coverage increased fatigue life from 8x10^5 to 6x10^7 cycles.
Media Selection: Stainless steel shot (SS316) prevents contamination of aerospace alloys, while chrome steel shot suits carbon steel components.
3. Quality Control Metrics and Validation Methods
Critical measurements include:
Surface Roughness: Using profilometers (e.g., Taylor Hobson Surtronic), targeting Ra values within ±10% of specifications.
Abrasive Contamination: Weekly magnetic separation tests to detect oil or paint particles, with visual inspection under 10x magnification.
Belt Alignment: Laser tools ensure ±0.3mm centerline accuracy to prevent workpiece jams.
Dust Emission: HEPA filters must maintain <0.5mg/m³, compliant with OSHA 29 CFR 1910.1000 and EU EN 15051 standards.
1. Automotive Manufacturing: High-Volume Processing
In automotive plants, wire mesh conveyors handle:
Engine Blocks: 8-wheel machines with 120-150 kg/min abrasive flow remove casting sand. A 4m-wide belt processes 100 blocks/hour, reducing labor by 75%.
Suspension Components: Shot peening control arms with S170 shot at 65 m/s creates 900-1,100MPa compressive stress, extending service life from 6 to 12 years.
Aluminum Wheels: Ceramic bead blasting achieves Ra 2.μm, eliminating acid etching and cutting wastewater treatment costs by 50%.
Case Study: A Guangzhou OEM uses a 10-wheel through-type machine with dual 4m x 18m belts, processing 1,500 wheels daily. Automated loading robots and integrated dust extraction reduce energy consumption to 0.7kWh per wheel, 30% below the industry average.
2. Aerospace: Precision Treatment for Critical Components
Aerospace applications require:
Turbine Blades: Peening cobalt-chrome blades with 0.3mm ceramic beads at 55 m/s creates 0.25mm deep compressive layers to resist thermal fatigue.
Landing Gear Parts: Shot peening 4340 steel with S550 shot at 90 m/s increases fracture toughness by 35%.
Composite Tooling: Glass bead blasting (50 mesh) roughens mold surfaces, improving resin adhesion and raising composite part yield from 82% to 97%.
3. Heavy Industry: Construction and Mining Equipment
For large components:
Excavator Buckets: Manganese steel buckets blasted with 1-2mm steel grit remove welding spatters, with 6-wheel machines processing 8-12 buckets/hour.
Crusher Plates: Shot peening with angular steel grit increases wear resistance by 60%, extending service life from 4 to 6 months in mining operations.
Bridge Beams: Through-type machines with 10m-long belts achieve Sa 2.5 cleanliness (ISO 8501-1), preparing them for anti-corrosion coatings lasting 15+ years.
1. Maintenance Strategies and Downtime Reduction
Key maintenance areas:
Blasting Wheels: Blades need replacement every 600-900 hours. Quick-change designs (e.g., Kaitai’s 20-minute replacement system) cut downtime by 70%.
Belt Wear: Wire breakage occurs at 6,000-8,000 hours. Aramid-reinforced belts extend life to 12,000 hours but cost 40% more.
Chamber Liners: Manganese steel liners last 1,800-2,500 hours; polyurethane liners (for non-ferrous media) last 3,500-5,000 hours but are unsuitable for steel shot.
Predictive maintenance technologies:
Vibration sensors detect wheel imbalance at 0.05mm amplitude, triggering alerts before failure.
Thermal imaging monitors bearing temperatures, predicting failures 96 hours in advance.
RFID tags track abrasive usage, automating reordering when levels drop below 15%.
2. Environmental Innovations and Energy Efficiency
Eco-friendly advancements:
Dust Collection: Electrostatic precipitators achieve 99.95% efficiency, reducing emissions to <0.3mg/m³ vs. 95% for bag filters.
Abrasive Recycling: Closed-loop systems with centrifugal separators achieve 99.7% media reuse, saving $60,000/year for a medium-sized foundry.
Energy Savings: IE5 motors and regenerative drives cut power consumption by 25%. A 30kW machine retrofitted with VFDs saved $15,000/year in Zhejiang.
3. Future Technological Directions
AI-Powered Process Control: Machine learning optimizes parameters using real-time 3D surface scans, achieving ±3% roughness consistency.
Hybrid Blasting Systems: Combining shot blasting with dry ice or water jetting reduces cycle times by 40% for complex parts.
Modular Design: Plug-and-play blasting modules enable reconfiguration in 90 minutes, down from 10 hours previously.
Additive Manufacturing Integration: Post-processing 3D-printed parts with precision blasting removes supports and refines surfaces in one step.
From manual belt systems in the mid-20th century to today’s intelligent, IoT-integrated machines, wire mesh conveyor shot blasting has revolutionized surface treatment. Key drivers—precision process control, energy efficiency, and modular design—have enabled its adoption across industries, from automotive mass production to aerospace precision engineering. As manufacturers face pressures to reduce costs, meet sustainability targets, and integrate Industry 4.0 technologies, the next generation of machines will likely feature AI-optimized blasting algorithms, hybrid processing systems, and fully automated material handling.
For businesses, selecting the right solution requires balancing initial investment against long-term TCO, while staying abreast of technological trends. In an era of global manufacturing competition, the wire mesh conveyor shot blasting machine remains indispensable for achieving efficient, high-quality surface engineering. As materials science and automation continue to advance, this technology will play an increasingly critical role in enabling next-generation manufacturing processes.