Hotline
+86-136 8495 9862
Email:cennia@szmizhi.com
Add::104,Building 27,Third Industrial Zone, Longxi Community,Longgang District,Shenzhen,China.
Coil Forming & Handling Equipment
Surface Treatment Equipment
Solutions
Application
About Us
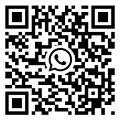
Welcome to MIZHI
For consultation/feedback, please call the service hotline: +86-136 8495 9862 Email:cennia@szmizhi.com
Tumble belt shot blasting machines have long been vital for high-volume surface treatment of small castings, but the accumulation of abrasive media, metal debris, and dust within their components has posed significant challenges for maintenance and hygiene. Traditional designs often require hours of manual cleaning, leading to prolonged downtime, increased labor costs, and potential contamination risks. The development of easy clean designs has revolutionized these systems, prioritizing accessibility, self-cleaning features, and anti-contamination materials to minimize maintenance burdens and enhance operational efficiency.
Easy clean designs focus on:
Minimizing Trapping Points: Eliminating crevices, recesses, and horizontal surfaces where media or dust can accumulate.
Enhancing Accessibility: Designing components for quick disassembly and rapid cleaning.
Self-Cleaning Mechanisms: Integrating features that automatically remove debris during operation.
Hygienic Material Selection: Using non-porous, corrosion-resistant materials that resist fouling and are easy to sanitize.
This technological advancement is particularly critical for industries requiring high cleanliness standards, such as medical device manufacturing, food processing, and aerospace, where even minor contamination can lead to product failures or regulatory non-compliance.
1. Smooth Surface Engineering and Geometry
Easy clean machines prioritize fluid dynamics and anti-trap designs:
Radiused Corners and Sloped Surfaces:
All internal chamber corners feature minimum 25 mm radii, and horizontal surfaces are sloped at 15-30° to prevent media accumulation. In a test with steel grit, sloped surfaces reduced residual media by 90% compared to flat surfaces.
Tapered Belt Slats: Slats are designed with 10-15° tapered edges to shed media, while recessed fasteners eliminate protrusions that could trap particles. This design reduced manual cleaning of slat joints by 75%.
Non-Porous Coatings:
Chamber walls and belt components are coated with electropolished stainless steel (Ra <0.8 μm) or PTFE (Teflon) to create low-friction surfaces. PTFE-coated belts showed 80% less media adhesion than uncoated steel in pharmaceutical component blasting.
Ceramic Thermal Sprays: Plasma-sprayed alumina coatings (0.5-1 mm thick) provide a glassy, non-porous surface that resists abrasion and fouling, ideal for harsh foundry environments.
2. Quick-Release and Modular Components
Design for maintainability reduces cleaning time:
Tool-Less Disassembly:
Hinged chamber doors with quick-release clamps (compression latches) allow access in <1 minute, compared to 15-20 minutes for bolted designs. A medical device manufacturer reduced chamber cleaning setup time from 30 to 5 minutes using this feature.
Snap-Fit Belt Slats: Individual slats attach via spring-loaded clips, enabling rapid removal for cleaning. In a hardware plant, this allowed 100% belt slat inspection and cleaning in 2 hours, versus 8 hours for traditional bolted systems.
Modular Media Systems:
Detachable media hoppers and separators lift out as single units for washing, with quick-connect fluid lines and electrical plugs. A foundry using modular separators reduced media system cleaning time from 4 to 1.5 hours per shift.
Plug-and-Play Dust Filters: Cartridge filters with bayonet mounts allow replacement in <2 minutes, minimizing downtime during filter cleaning or replacement.
3. Integrated Self-Cleaning Mechanisms
Automated features reduce manual intervention:
Pneumatic Blow-Off Systems:
Compressed air nozzles (40-60 PSI) positioned around the chamber and belt automatically activate after each batch, blasting away residual media. In a test with aluminum castings, this reduced post-process media (residue) from 5% to <0.5%.
Vibratory Cleaning Modules:
Electromagnetic vibrators attached to media hoppers and conveyors induce low-amplitude vibrations (50-100 Hz) to dislodge stuck particles. This eliminated the need for manual hopper scraping, saving 1 hour per day in a stainless steel processing plant.
Reverse Airflow Cleaning:
Dust collectors use periodic reverse air pulses (6-8 bar) to dislodge dust from filter cartridges, extending their service life and maintaining cleaning efficiency without manual intervention.
1. Medical Device Manufacturing
Implant and Instrument Processing:
Easy clean systems with electropolished 316L stainless steel chambers and PTFE-coated belts meet ISO 13485 standards for medical devices. Blasting titanium spinal implants with 20 μm zirconia beads in such a system ensures no metallic contamination, with post-blasting particle counts <10 particles/ft² of >50 μm.
Sterile Component Preparation:
Quick-release belt modules allow thorough sanitization with alcohol or steam, critical for components entering cleanrooms. A surgical tool manufacturer reduced contamination-related rejects from 7% to 0.5% by implementing easy clean designs.
2. Food and Beverage Equipment
Stainless Steel Component Finishing:
Belts made from FDA-approved UHMWPE with smooth surfaces (Ra <0.5 μm) resist food residue buildup, while sloped chamber floors prevent liquid pooling. In a dairy equipment plant, these features reduced sanitization time from 4 hours to 1 hour per day.
Canning and Packaging Machinery Parts:
Easy clean blasting removes rust and scale from conveyor components without introducing contaminants. The self-cleaning pneumatic system ensures no abrasive media enters food processing areas, complying with USDA and FDA regulations.
3. Aerospace and Electronics
High-Purity Component Blasting:
Aerospace turbine blades require blasting free of foreign object debris (FOD). Easy clean systems with HEPA-filtered recirculation and non-shedding belts reduced FOD incidents by 99% in a jet engine component facility.
Microelectronic Package Deburring:
Tight geometries in IC packages demand thorough media removal. Easy clean machines with vacuum-assisted belt systems and anti-static coatings prevent ESD damage, achieving <0.1% media trapping in 0.5 mm diameter holes.
Advantages of Easy Clean Design in Tumble Belt Machines
1. Significant Downtime Reduction
Faster Routine Maintenance:
Quick-release components and self-cleaning features reduce scheduled maintenance from 8 hours/week to 2 hours/week in a typical automotive casting plant, increasing machine availability from 85% to 96%.
Minimized Unplanned Cleaning:
Anti-trap designs prevent media jams that cause unscheduled stops. A case study in a motorcycle parts factory showed a 75% decrease in emergency shutdowns for cleaning-related issues.
2. Cost Savings and Labor Efficiency
Reduced Labor Costs:
Automated self-cleaning and quick disassembly cut maintenance staff requirements by 50%. A medium-sized foundry saved $80,000 annually by reallocating maintenance personnel to production roles.
Lower Consumable Costs:
Efficient media recycling in easy clean systems reduces abrasive consumption by 15-20%, as less media is trapped and wasted. This equates to $15,000/year in savings for a plant using 100 tons of steel grit annually.
3. Enhanced Quality and Compliance
Consistent Cleanliness:
Easy clean designs maintain uniform cleanliness across batches, critical for industries with strict quality standards. A medical implant manufacturer achieved 100% compliance with ISO 11737-1 for bioburden control after upgrading to easy clean systems.
Regulatory Compliance:
Smooth surfaces and non-corrosive materials help meet standards like FDA 21 CFR Part 117 and EU 10/2011 for food contact materials, avoiding fines and production halts.
1. Balancing Cleanability with Structural Integrity
Challenge: Smooth, sloped surfaces may compromise structural strength in heavy-duty applications.
Solution:
Reinforced Hygienic Design: Stainless steel chambers use hidden internal ribs for strength, maintaining smooth exteriors. A foundry system with this design supported 2,000 kg/h of cast iron parts while meeting cleanroom standards.
Composite Materials Engineering: Hybrid components combine wear-resistant metals with easy clean polymers. For example, ceramic-coated steel slats with PTFE edge seals resist abrasion while shedding media.
2. Initial Cost vs. Long-Term Benefits
Challenge: Easy clean machines cost 15-30% more than standard designs, daunting for budget-constrained manufacturers.
Solution:
Life Cycle Cost Analysis: Tools demonstrate that easy clean systems pay for themselves in 1-2 years via reduced downtime and maintenance. A small medical parts supplier recovered their investment in 14 months through avoided contamination-related recalls.
Phased Upgrades: Manufacturers offer retrofit kits for existing machines, such as quick-release belt modules or self-cleaning hoppers, allowing incremental adoption.
3. User Training and Process Adherence
Challenge: Complex cleaning protocols may be misapplied, negating design benefits.
Solution:
Interactive Training Systems: AR-guided maintenance tutorials walk operators through cleaning procedures, reducing errors by 80%. A pharmaceutical company implemented this to ensure compliance with GMP guidelines.
Automated Cleaning Schedules: PLCs enforce mandatory cleaning cycles based on production hours, preventing operator oversight. Alerts prompt cleaning when media accumulation exceeds preset thresholds.
Innovations in Easy Clean Tumble Belt Technology
1. Self-Sanitizing Coatings
Photocatalytic Titanium Dioxide (TiO₂) Coatings:
UV-activated TiO₂ coatings on chamber walls decompose organic contaminants, reducing the need for chemical sanitization. In a medical device test, TiO₂-coated chambers showed 99.9% reduction in bacterial growth after 24 hours of exposure.
Silver Ion Antimicrobial Treatments:
Silver-impregnated polymers in belts and seals inhibit microbial growth, ideal for food processing. These treatments maintain efficacy for 5,000+ hours, eliminating the need for frequent disinfectant applications.
2. Robotic Cleaning Assistants
Cobot-Integrated Cleaning Arms:
Collaborative robots with articulated arms and pressure washer attachments perform deep cleaning during scheduled downtime. A automotive plant used cobots to reduce manual chamber cleaning from 4 hours to 30 minutes per week.
Nano-robot Debris Collectors:
Experimental micro-robots (10-20 mm) navigate tight spaces like belt joints, using electroadhesion to collect trapped media. Lab tests showed 95% debris removal from 1 mm gaps.
3. Smart Clean Monitoring Systems
RFID-Enabled Cleanliness Tracking:
RFID tags in components record cleaning history and verify compliance. A aerospace supplier used this to ensure every blasted part met FOD standards, with digital records for audit trails.
Terahertz Imaging for Sub-Surface Contamination:
Terahertz scanners detect media trapped in micro-cavities, invisible to traditional inspection. This technology identified 20% more contaminated parts in a casting facility, preventing downstream issues.
1. Hydrophobic and Superoleophobic Surfaces
Nanostructured Anti-Adhesion Coatings:
Lotus-effect inspired coatings with hierarchical nano-pores repel both water and oil, causing media and debris to slide off effortlessly. Prototype coatings reduced media adhesion by 98% in lab tests.
Self-Lubricating Surface Textures:
Micro-grooved surfaces filled with permanent lubricants create a low-friction layer, minimizing particle sticking. These could eliminate the need for manual belt lubrication in food-grade applications.
2. Fully Automated Cleaning Ecosystems
Closed-Loop Cleaning Cycles:
Post-blasting, machines automatically transition to cleaning mode: belt reverses, nozzles spray detergent, and vacuums extract debris—all without operator intervention. A concept design for medical devices achieved full cleaning in 5 minutes between batches.
AI-Optimized Cleaning Schedules:
Machine learning analyzes production data to predict when cleaning is needed, optimizing intervals to balance cleanliness and productivity. This could reduce unnecessary cleanings by 30%, saving energy and water.
3. Biodegradable and Dissolvable Cleaning Aids
Water-Soluble Cleaning Media:
Blasting with sodium bicarbonate or ice particles that dissolve during post-blasting rinsing, eliminating the need for media removal. This is being tested for single-use medical devices, reducing cleaning steps by 50%.
Enzyme-Based Degradation Systems:
Chamber surfaces coated with immobilized enzymes break down organic residues, ideal for pharmaceutical applications where harsh chemicals are prohibited.
Easy clean design has transformed tumble belt shot blasting machines from maintenance-intensive equipment to hygienic, efficient production tools. By prioritizing accessibility, self-cleaning mechanisms, and anti-contamination materials, these systems address the long-standing challenges of media accumulation and downtime in surface treatment. As industries increasingly demand higher cleanliness standards and leaner operations, easy clean technologies will continue to evolve through nanocoatings, robotic assistance, and smart automation. For manufacturers, investing in these designs is not just about meeting regulatory requirements—it’s a strategic move to enhance productivity, reduce costs, and ensure product quality in an era of heightened consumer and industry expectations. The future holds even more innovative solutions, promising a new standard of cleanliness and efficiency in tumble belt shot blasting.