Hotline
+86-136 8495 9862
Email:cennia@szmizhi.com
Add::104,Building 27,Third Industrial Zone, Longxi Community,Longgang District,Shenzhen,China.
Coil Forming & Handling Equipment
Surface Treatment Equipment
Solutions
Application
About Us
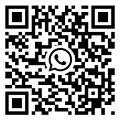
Welcome to MIZHI
For consultation/feedback, please call the service hotline: +86-136 8495 9862 Email:cennia@szmizhi.com
A sand blasting machine, also known as a sandblaster, is a versatile and essential piece of equipment widely utilized across numerous industries for surface treatment purposes. Its primary function is to propel abrasive materials, traditionally sand but now often other specialized abrasives, at high speeds onto the surface of various workpieces. By doing so, it effectively removes contaminants such as rust, paint, scale, dirt, and old coatings, while also creating a roughened surface texture that enhances adhesion for subsequent processes like painting, coating, and bonding. The application of sand blasting machines spans from metal fabrication and automotive manufacturing to construction, woodworking, and even artistic endeavors, making it a crucial tool in modern industrial and creative processes.
Pressure Vessel
The pressure vessel is a central component of the sand blasting machine, typically constructed from high strength steel to withstand the internal pressure generated during operation. It serves as a storage tank for the abrasive material and also houses the compressed air system. The vessel is equipped with safety features such as pressure relief valves to prevent over pressurization, which could lead to dangerous situations. The size of the pressure vessel varies depending on the scale of the sand blasting operation; larger vessels are used for industrial scale projects where a continuous supply of abrasive is required, while smaller ones are suitable for portable or workshop based sandblasters.
Compressed Air System
The compressed air system is responsible for generating the force that propels the abrasive material. It usually consists of an air compressor, air filters, regulators, and hoses. The air compressor draws in ambient air, compresses it, and delivers it to the pressure vessel. Air filters are essential to remove moisture, oil, and other impurities from the compressed air, as these contaminants can affect the quality of the sandblasting process and damage the equipment. Regulators control the air pressure, allowing operators to adjust it according to the specific requirements of the workpiece and the type of abrasive being used. Hoses connect the various components of the system, ensuring a continuous flow of compressed air to the blast gun.
Blast Gun
The blast gun is the interface between the operator and the workpiece. It is designed to direct the stream of abrasive material precisely onto the surface to be treated. Blast guns come in different types, including siphon feed, direct pressure, and suction feed guns. Siphon feed guns draw the abrasive from a hopper using the venturi effect created by the high velocity air stream. Direct pressure guns, on the other hand, use the pressure within the vessel to force the abrasive through the gun, providing more power and control. Suction feed guns are less powerful but are suitable for light duty tasks and are often more affordable. The nozzle of the blast gun is a critical component, as its size and shape determine the pattern and intensity of the abrasive stream. Nozzles are typically made of wear resistant materials like tungsten carbide to withstand the constant abrasion from the high speed particles.
Abrasive Hopper and Feed System
The abrasive hopper stores the sand or other abrasive media. It is connected to the pressure vessel or the blast gun via a feed system. The feed system controls the flow rate of the abrasive, ensuring a consistent and appropriate amount is delivered to the blast gun. Some advanced sand blasting machines feature adjustable feed systems that allow operators to fine tune the abrasive flow based on the material being blasted, the surface condition, and the desired finish. This precision is crucial for achieving optimal results and minimizing abrasive waste.
Dust Collection System
During the sandblasting process, a significant amount of dust is generated as the abrasive material breaks down contaminants on the workpiece surface. A dust collection system is essential to maintain a clean and safe working environment. It typically includes a dust collector, cyclone separator, and exhaust ducts. The cyclone separator first separates the larger particles from the dust laden air, reducing the load on the dust collector. The dust collector then uses filters, such as cartridge filters or bag filters, to capture the finer dust particles. The clean air is exhausted to the atmosphere, while the collected dust is stored in a hopper for proper disposal. In some cases, the dust collection system may also incorporate a recirculation feature to reuse the abrasive material after it has been cleaned of dust and debris.
The operation of a sand blasting machine begins with the activation of the compressed air system. The air compressor starts to draw in and compress air, which is then filtered and regulated to the appropriate pressure. The regulated compressed air is directed into the pressure vessel, where it mixes with the abrasive material stored in the abrasive hopper.
Depending on the type of sandblasting machine (siphon feed, direct pressure, or suction feed), the abrasive is either drawn into the air stream or forced out by the pressure. In a direct pressure system, for example, the compressed air within the pressure vessel pushes the abrasive through the feed system and into the blast gun. Once in the blast gun, the high velocity air stream accelerates the abrasive particles, propelling them out of the nozzle at high speeds.
The abrasive particles impact the surface of the workpiece with great force, effectively removing contaminants through mechanical abrasion. The rough texture created by the impact of the particles not only cleans the surface but also increases the surface area, which improves the adhesion of subsequent coatings or treatments. As the sandblasting process continues, the used abrasive and the removed contaminants fall to the ground or are collected by the dust collection system. The dust collection system separates the dust from the abrasive, and in some cases, the clean abrasive can be recycled back into the process, reducing the overall cost of operation.
Applications of Sand Blasting Machine
Metal Fabrication and Manufacturing
In the metal fabrication industry, sand blasting machines are extensively used for surface preparation. Before welding, sandblasting removes rust, mill scale, and other impurities from metal surfaces, ensuring a clean and proper bond between metal parts. It also helps in preparing metal surfaces for painting, powder coating, or electroplating. By creating a rough surface, the adhesion of the coating materials is significantly enhanced, preventing peeling and extending the lifespan of the coated metal products. Additionally, sandblasting can be used to deburr and smooth the edges of metal components, improving their appearance and functionality.
Automotive Industry
Automotive manufacturers rely on sand blasting machines for various tasks. During the restoration of classic cars, sandblasting is used to strip old paint, rust, and body filler from the vehicle's body panels. This reveals the true condition of the metal, allowing for proper repair and preparation before applying new paint. In new car manufacturing, sandblasting is used to clean and prepare parts such as engine blocks, cylinder heads, and suspension components. It helps in removing casting residues and improving the surface finish, which is crucial for the performance and durability of these parts.
Construction Industry
In construction, sand blasting machines are used for cleaning and renovating concrete, brick, and stone surfaces. They can remove graffiti, old paint, and dirt from building facades, restoring the original appearance of the structures. Sandblasting is also employed to prepare surfaces for the application of protective coatings, such as waterproofing membranes or sealants. Additionally, it can be used to etch patterns or designs onto concrete and stone surfaces, adding an aesthetic element to architectural projects.
Woodworking
Although less common than in metalworking, sand blasting machines are also used in woodworking. They can be used to create a rustic or textured finish on wooden surfaces, giving the wood a unique appearance. Sandblasting can also be used to remove old finishes from wooden furniture, preparing the surface for refinishing. However, special care must be taken when sandblasting wood, as the high velocity abrasive particles can easily damage the soft wood fibers if not properly controlled.
Art and Sculpture
Artists and sculptors often use sand blasting machines to create intricate designs and textures on various materials, including metal, stone, and glass. The precision and control offered by sandblasting allow for the creation of detailed patterns and reliefs that would be difficult to achieve using other methods. Sandblasting can also be used to etch images or text onto surfaces, adding a personalized touch to artworks and sculptures.
Effective Surface Cleaning
Sand blasting machines are highly effective at removing a wide range of contaminants from surfaces. Whether it's thick layers of rust on metal, stubborn paint on concrete, or dirt and grime on various materials, the high velocity abrasive particles can quickly and thoroughly clean the surface, leaving it ready for further treatment.
Improved Adhesion
By creating a rough surface texture, sandblasting significantly improves the adhesion of coatings, paints, and adhesives. This results in longer lasting finishes and better performing bonded joints, reducing the likelihood of coating failure and the need for frequent maintenance or reapplication.
Versatility
Sand blasting machines can be used on a vast variety of materials, including metals, ceramics, glass, wood, and concrete. They can also handle different types of contaminants and surface conditions, making them a versatile tool for numerous industries and applications.
Precision and Control
Modern sand blasting machines offer a high degree of precision and control. Operators can adjust parameters such as air pressure, abrasive flow rate, and nozzle type to achieve the desired results. This precision allows for targeted cleaning and surface treatment, minimizing damage to the underlying material while still effectively removing contaminants.
Maintenance and Safety of Sand Blasting Machine
Maintenance
Regular maintenance is essential to keep a sand blasting machine in optimal working condition. The pressure vessel should be inspected regularly for signs of corrosion, cracks, or leaks. Pressure relief valves should be tested periodically to ensure they are functioning correctly. The compressed air system components, including the air compressor, filters, and regulators, need to be cleaned and serviced as per the manufacturer's instructions. The blast gun and nozzle should be checked for wear and tear, and any damaged parts should be replaced promptly. The abrasive hopper and feed system should be kept clean to prevent clogging, and the dust collection system filters should be cleaned or replaced regularly to maintain efficient dust removal.
Safety
Safety is of paramount importance when operating a sand blasting machine. Operators must wear appropriate personal protective equipment (PPE), including a full face respirator with high efficiency filters to protect against inhaling dust, safety goggles, earplugs to protect against the noise generated during operation, and protective clothing to shield the skin from abrasive particles. The work area should be well ventilated, and proper signage should be displayed to warn others of the ongoing sandblasting operation. The machine should be grounded to prevent electrical hazards, and all safety devices, such as pressure relief valves and emergency stop buttons, should be regularly inspected and tested to ensure they are in working order.
Future Developments of Sand Blasting Machine
The future of sand blasting machines holds several promising developments. One area of focus is the development of more environmentally friendly sandblasting solutions. As environmental regulations become stricter, there is a growing demand for abrasive materials that are less harmful to the environment and can be easily disposed of or recycled. Researchers are exploring the use of biodegradable and recyclable abrasives, such as corn cobs, walnut shells, and recycled glass beads, as alternatives to traditional sand based abrasives.
Another trend is the integration of automation and digital control systems into sand blasting machines. Automated sandblasting systems can be programmed to perform repetitive tasks with high precision, reducing the need for manual labor and improving the consistency of the surface treatment process. Digital control systems allow operators to monitor and adjust the machine's parameters in real time, optimizing the sandblasting process for different workpieces and surface conditions. Additionally, the use of sensors and imaging technologies can be incorporated to detect surface defects and adjust the sandblasting process accordingly, further enhancing the quality of the surface treatment.
In conclusion, the sand blasting machine is a highly valuable and widely used piece of equipment with a diverse range of applications across multiple industries. Its unique structure, working principle, performance advantages, and safety features make it an indispensable tool for surface treatment. With continuous advancements in technology, the sand blasting machine is expected to become more efficient, environmentally friendly, and automated, further expanding its capabilities and applications in the future.