Hotline
+86-136 8495 9862
Email:cennia@szmizhi.com
Add::104,Building 27,Third Industrial Zone, Longxi Community,Longgang District,Shenzhen,China.
Coil Forming & Handling Equipment
Surface Treatment Equipment
Solutions
Application
About Us
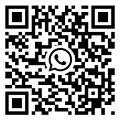
Welcome to MIZHI
For consultation/feedback, please call the service hotline: +86-136 8495 9862 Email:cennia@szmizhi.com
In the ever - evolving world of industrial surface treatment, the tumble belt shot blasting machine has emerged as an indispensable and highly adaptable piece of equipment. This innovative machine is purpose - built to carry out a wide array of operations, spanning from meticulous cleaning and deburring to sophisticated surface strengthening, making it an integral part of countless manufacturing and processing sectors.
Foundry and Forging Industries
Casting Cleaning: In foundries, after the casting process, the castings are often marred with residual sand, scale, and other impurities on their surfaces. The tumble belt shot blasting machine is extremely effective in eliminating this casting sand and filings. For instance, small to medium - sized cast iron or aluminum alloy castings can be efficiently cleaned, preparing them for subsequent processes such as machining or painting.
Forged Part Preparation: Forged components require their surfaces to be cleaned and strengthened. The shot blasting process not only removes the oxide layer that forms during forging but also induces compressive stresses on the surface. This is of great significance for parts used in high - stress applications, such as automotive crankshafts or aerospace components, as it enhances their fatigue resistance.
Automotive Industry
Component Surface Treatment: Automotive parts like gears, shafts, and brackets undergo tumble belt shot blasting. This process helps in removing rust, paint overspray, or other contaminants from the surface. Additionally, the surface strengthening effect improves the durability of these parts, ensuring they can endure the harsh operating conditions within an automobile.
Pre - painting Preparation: Before painting automotive parts, a clean and appropriately rough surface is essential for good paint adhesion. Tumble belt shot blasting creates the ideal surface profile, enhancing the paint's grip and thereby extending the lifespan of the painted finish.
Aerospace Industry
High - Precision Component Cleaning: In the aerospace industry, where the quality and reliability of components are of the utmost importance, tumble belt shot blasting is used to clean and treat parts made of various materials, including titanium alloys and high - strength steels. The process ensures that no contaminants are present on the surface, which could potentially compromise the performance of aircraft engines, landing gear components, or wing structures.
Surface Strengthening for Fatigue Resistance: Aerospace components are subjected to extreme mechanical and thermal stresses during flight. Shot blasting improves the fatigue life of these components by introducing compressive stresses on the surface, reducing the risk of crack initiation and propagation.
General Manufacturing
Deburring and Edge Rounding: Many manufactured parts have sharp edges or burrs formed during the machining process. Tumble belt shot blasting can effectively deburr these parts and round the edges, enhancing the safety of handling and also improving the aesthetics of the final product. This is applicable to a wide range of products, from small hardware components to larger machinery parts.
Surface Roughing for Adhesion: When components need to be bonded or coated with other materials, a rough surface is often required for better adhesion. Tumble belt shot blasting can create the desired surface roughness, ensuring strong and long - lasting bonds in applications such as plastic - to - metal bonding or the application of protective coatings.
High - Quality Surface Treatment
Uniform Coverage: The continuous rolling and turning of workpieces on the tumble belt guarantee that the abrasive media reaches all areas of the workpiece's surface uniformly. This results in a consistent surface finish, whether it's for cleaning, deburring, or strengthening purposes.
Defect Removal: The machine is capable of eliminating surface defects such as rust, scale, and minor scratches, improving the overall quality and appearance of the workpiece. This is particularly crucial for products where visual appeal and surface integrity are important.
Durability and Reliability
Wear - Resistant Components: The machine's housing is typically safeguarded by wear - resistant manganese steel, which can endure the constant impact of abrasive media. The turbines, responsible for propelling the abrasive, are also constructed from wear - resistant materials, ensuring long - term operation without frequent replacements.
Efficient Media Recycling System: Tumble belt shot blasting machines are equipped with systems for the continuous return and cleaning of the abrasive media. This not only reduces the consumption of abrasive but also maintains the quality of the blasting process by ensuring that only clean and effective media is used.
User - Friendly Operation
Easy Loading and Unloading: The design of the machine allows for convenient access to the loading and unloading area. Workpieces can be quickly and easily placed onto the tumble belt, and after the blasting process, they can be effortlessly removed. Some models even offer automated loading and unloading options, further streamlining the process.
Simple Control Systems: Many tumble belt shot blasting machines are equipped with user - friendly control systems. These can include PLC (Programmable Logic Controller) Siemens systems, displays for monitoring machine parameters, and the option for automatic or manual operation. Features like automatic start - up of turbines and working - hours counters make the operation and maintenance of the machine straightforward.
Versatility
Adaptability to Different Workpiece Sizes and Shapes: Whether it's small, delicate plastic parts or large, heavy - duty forged components, tumble belt shot blasting machines can handle a wide spectrum of workpiece sizes and shapes. The adjustable settings of the machine, such as the speed of the tumble belt and the intensity of the blasting, can be customized according to the specific requirements of the workpiece.
Multi - Process Capability: In addition to basic cleaning and deburring, the machine can be utilized for surface strengthening, surface roughening, and even some degree of material removal. This multi - process capability makes it a valuable asset in various manufacturing and finishing operations.
Tumble Belt
Rubber Belt: In certain models, a perforated, continuously running endless reinforced rubber belt is employed. The rubber belt is gentle on the workpieces, making it suitable for parts that are sensitive to scratches or damage. It also provides good friction, ensuring that the workpieces roll and turn effectively during the blasting process.
Manganese Steel Belt: Other models feature a belt made from steel flaps, usually manganese steel. This type of belt is more robust and can handle heavier and more rugged workpieces. The steel belt is highly durable and can withstand the impact of abrasive media and the movement of heavy parts without significant wear.
Blasting Turbines
High - Speed Propulsion: The blasting turbines are the core of the machine. They are designed to accelerate the abrasive media to high speeds and project it onto the workpieces. The turbines are equipped with special blades, such as gamma blades in some advanced models, which ensure high media - throwing efficiency. The position and orientation of the turbines on the machine are carefully engineered to direct the abrasive media precisely onto the workpieces, achieving optimal blasting results.
Wear - Resistant Design: Since the turbines are constantly exposed to the abrasive media, they are made from wear - resistant materials. This ensures a long service life and reliable operation, reducing the need for frequent maintenance and replacement.
Abrasive Media Recycling System
Media Separation: After the abrasive media has been used to blast the workpieces, it needs to be separated from the debris and recycled. The machine is equipped with a system that typically includes a combination of screens, cyclones, and magnetic separators (if the abrasive media is magnetic). These components work in tandem to separate the used abrasive media from dust, burr particles, and other contaminants.
Media Cleaning and Reuse: The separated abrasive media is then cleaned to remove any remaining impurities. This clean media is then returned to the blasting system for reuse. The efficient recycling of abrasive media not only saves costs but also reduces the environmental impact associated with the disposal of used media.
Machine Housing
Protection and Containment: The machine housing is designed to shield the operator and the surrounding environment from the abrasive media and the debris generated during the blasting process. It is constructed from sturdy materials, such as wear - resistant manganese steel, which can withstand the continuous impact of the abrasive. The housing also helps in containing the blasting process, ensuring that the abrasive media is directed only onto the workpieces within the machine.
Insulation and Noise Reduction: In some models, the housing may also be insulated to reduce heat loss and noise. This is important for maintaining a comfortable working environment and also for energy efficiency, especially in facilities where multiple shot blasting machines are operating.
Machine Model | Productivity (tons/hour) | Maximum Volume Charge (dm³) | Maximum Advised Load (kg) | Wheel Power (kW) | Drum Diameter (mm) | Chamber Width (mm) | Air Requirement (m³/h) |
MB150G | 0.6 - 1.2 | 150 | 200 | 7.5 (or 11 in some cases) | 650 | 850 | 2000 |
MB300G | 1.5 - 2.5 | 300 | 600 | - | - | - | - |
G - 2000 - 2 (with manganese steel belt) | 8 | 2000 | 5000 | 2 * 45 | 1650 | 2400 | 18000 |
The tumble belt shot blasting machine, sometimes referred to as a crawler shot blasting machine, is ingeniously designed to manage large quantities of parts, regardless of their size variations. Its distinct design incorporates a continuous, perforated belt. This belt, which can be made of either rubber or manganese steel depending on the specific model, moves in a caterpillar - like motion. When workpieces are placed on this belt, its unique shape causes the parts to rotate and roll as it progresses. This rolling action is crucial as it ensures that every part of the workpiece's surface is evenly exposed to a high - velocity jet of abrasive media. The abrasive media is forcefully projected onto the workpieces by high - speed turbines, enabling efficient and thorough surface treatment.
the tumble belt shot blasting machine is a highly versatile and efficient piece of equipment in the industrial surface treatment landscape. Its wide range of applications, numerous features, well - designed components, and diverse basic parameters make it an ideal choice for industries looking to enhance the quality, durability, and appearance of their products through effective surface treatment.