Hotline
+86-136 8495 9862
Email:cennia@szmizhi.com
Add::104,Building 27,Third Industrial Zone, Longxi Community,Longgang District,Shenzhen,China.
Coil Forming & Handling Equipment
Surface Treatment Equipment
Solutions
Application
About Us
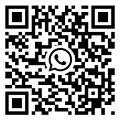
Welcome to MIZHI
For consultation/feedback, please call the service hotline: +86-136 8495 9862 Email:cennia@szmizhi.com
In the dynamic landscape of industrial manufacturing, the roller conveyor shot blasting machine has emerged as a pivotal solution for surface treatment processes. This specialized equipment combines advanced technology with efficient material handling, offering a comprehensive approach to enhancing the quality and durability of a wide range of industrial products.
Automotive Industry
Component Cleaning and Surface Preparation: In the automotive manufacturing process, numerous components such as engine blocks, chassis parts, and suspension components require thorough surface treatment. The roller conveyor shot blasting machine effectively removes casting sand, rust, and other contaminants from these parts, ensuring a clean surface for further machining, painting, or coating. For example, engine blocks often have rough surfaces after casting, and shot blasting smooths them out, improving heat dissipation and the overall performance of the engine.
Enhancing Fatigue Resistance: Shot blasting also imparts compressive stresses on the surface of automotive components, which significantly improves their fatigue resistance. This is crucial for parts like crankshafts and axles that are subjected to high - stress cyclic loading during operation. By increasing the fatigue life of these components, the overall reliability and lifespan of the vehicle are enhanced.
Aerospace Industry
High - Precision Component Treatment: The aerospace industry demands the highest level of quality and precision in its components. The roller conveyor shot blasting machine is used to clean and treat parts made of advanced materials such as titanium alloys and high - strength steels. It removes machining marks, oxidation layers, and other surface imperfections, ensuring that the components meet the strict aerospace standards. For instance, aircraft landing gear components, which are exposed to extreme forces during takeoff and landing, require a flawless surface finish, and shot blasting helps achieve this.
Surface Strengthening for Safety - Critical Parts: Safety - critical aerospace components, such as those in the engine and airframe, need to be highly resistant to fatigue and stress corrosion cracking. Shot blasting introduces compressive stresses on the surface, which act as a barrier against crack initiation and propagation, thereby enhancing the safety and reliability of these components.
Construction and Heavy Machinery
Steel Structure Cleaning and Preparation: In the construction of buildings, bridges, and other infrastructure, steel structures are commonly used. The roller conveyor shot blasting machine is employed to clean the steel surfaces, removing rust, mill scale, and other contaminants. This pre - treatment is essential for applying protective coatings, such as paint or zinc coatings, which prevent corrosion and extend the lifespan of the structures. For example, large - scale steel beams used in high - rise buildings are shot - blasted to ensure a strong bond with the protective coating.
Component Refurbishment: Heavy machinery components, such as hydraulic cylinders, gears, and shafts, often require refurbishment after extended use. Shot blasting is used to remove worn - out surfaces, clean out contaminants, and prepare the components for re - coating or re - machining. This process helps to restore the performance and functionality of the components, reducing the need for costly replacements.
Metal Fabrication and Foundry
Deburring and Edge Rounding: In metal fabrication shops, parts are often cut, drilled, or welded, leaving behind sharp edges and burrs. The roller conveyor shot blasting machine can effectively deburr and round these edges, improving the safety of handling and the aesthetics of the final product. Additionally, it helps to remove any heat - affected zones or surface imperfections caused by the fabrication process.
Casting Cleaning and Surface Finishing: In foundries, castings are typically covered with sand, oxide layers, and other residues. Shot blasting is an efficient method for cleaning these castings, revealing a clean and smooth surface. It also helps to improve the surface finish of the castings, making them suitable for further processing or direct use in various applications.
High - Efficiency Blasting System
Powerful Blasting Turbines: The machine is equipped with high - power blasting turbines that can accelerate the abrasive media to extremely high velocities. These turbines are designed with advanced impeller designs to ensure a high - volume and uniform distribution of the abrasive, resulting in efficient and thorough surface treatment. The number and arrangement of the turbines can be customized according to the specific requirements of the workpiece and the desired blasting intensity.
Adjustable Blasting Parameters: The blasting parameters, such as the abrasive flow rate, blasting pressure, and turbine speed, can be easily adjusted. This allows operators to fine - tune the shot blasting process for different types of workpieces, materials, and surface treatment requirements. For example, softer materials may require a lower blasting intensity, while harder materials may need a more aggressive treatment.
Reliable Roller Conveyor System
Robust Construction: The roller conveyor is built with a heavy - duty frame and high - quality rollers to ensure reliable operation even under heavy loads. The rollers are designed to be durable and resistant to wear, minimizing maintenance requirements. The conveyor system can be customized to accommodate different workpiece sizes, shapes, and weights, providing flexibility in production.
Precise Speed Control: The speed of the roller conveyor can be precisely controlled, allowing for consistent and uniform surface treatment. This is important for ensuring that each workpiece receives the appropriate amount of blasting time. The adjustable speed also enables operators to optimize the production rate based on the complexity of the surface treatment and the throughput requirements.
Effective Abrasive Recycling and Dust Collection
Abrasive Recycling System: The roller conveyor shot blasting machine is equipped with an efficient abrasive recycling system. After the abrasive media has been used to blast the workpieces, it is collected, separated from the debris, and recycled for reuse. This not only reduces the consumption of abrasive media but also helps to maintain a consistent quality of the blasting process. The recycling system typically includes a combination of screens, cyclones, and magnetic separators to effectively clean and reclaim the abrasive.
Advanced Dust Collection System: During the shot blasting process, dust and debris are generated. The machine is equipped with a high - efficiency dust collection system that captures and filters these particles, preventing them from being released into the environment. The dust collection system not only ensures a clean and safe working environment but also helps to comply with environmental regulations.
User - Friendly Operation and Control
Intuitive Control Panel: The machine is equipped with an intuitive control panel that allows operators to easily set and monitor the blasting parameters, conveyor speed, and other functions. The control panel is designed to be user - friendly, with clear displays and easy - to - operate buttons. Operators can quickly adjust the settings to suit different production requirements, minimizing the learning curve and maximizing productivity.
Automated Safety Features: Safety is a top priority in the design of the roller conveyor shot blasting machine. The machine is equipped with a range of automated safety features, such as emergency stop buttons, safety interlocks, and protective enclosures. These features ensure the safety of the operators and prevent any accidents or injuries during the operation of the machine.
Blasting Chamber
Wear - Resistant Linings: The blasting chamber is the core component of the machine, where the actual shot blasting process takes place. It is lined with wear - resistant materials, such as manganese steel or rubber, to protect against the continuous impact of the abrasive media. The wear - resistant linings not only extend the lifespan of the blasting chamber but also help to maintain a consistent blasting environment by preventing any debris or particles from escaping.
Proper Ventilation and Lighting: The blasting chamber is designed with proper ventilation to remove the dust and fumes generated during the shot blasting process. It also has adequate lighting to allow operators to visually inspect the workpieces during the treatment. The ventilation and lighting systems are carefully integrated to ensure a safe and efficient working environment.
Blasting Turbines
High - Performance Impellers: The blasting turbines are responsible for accelerating the abrasive media and propelling it onto the workpieces. They are equipped with high - performance impellers that are designed to withstand the high - speed rotation and the impact of the abrasive. The impellers are made of wear - resistant materials and can be easily replaced when they become worn out, ensuring the continuous operation of the machine.
Variable - Speed Drives: The turbines are powered by variable - speed drives, which allow for precise control of the blasting intensity. Operators can adjust the speed of the turbines according to the specific requirements of the workpiece, providing flexibility in the surface treatment process.
Roller Conveyor
Heavy - Duty Rollers: The roller conveyor consists of a series of heavy - duty rollers that are used to transport the workpieces through the blasting chamber. The rollers are made of high - quality materials and are designed to be durable and resistant to wear. They are evenly spaced to ensure a stable and smooth movement of the workpieces.
Drive System: The roller conveyor is powered by a reliable drive system, which can be either electric or hydraulic. The drive system is designed to provide a consistent and adjustable speed, allowing for precise control of the workpiece transportation.
Abrasive Recycling and Dust Collection Systems
Abrasive Separation and Recycling Components: The abrasive recycling system includes components such as screens, cyclones, and magnetic separators. These components work together to separate the used abrasive media from the debris and contaminants. The clean abrasive is then recycled and returned to the blasting system for reuse.
Dust Collection Filters and Fans: The dust collection system is equipped with high - efficiency filters and powerful fans. The filters capture the dust and debris particles, preventing them from being released into the atmosphere. The fans are used to create a negative pressure inside the blasting chamber, ensuring the efficient removal of dust and fumes.
Control System
PLC - Based Control: The control system of the roller conveyor shot blasting machine is typically based on a Programmable Logic Controller (PLC). The PLC is a microprocessor - based device that allows for precise control and automation of the machine's functions. It can be programmed to control various parameters such as the blasting intensity, conveyor speed, abrasive recycling, and dust collection.
Human - Machine Interface (HMI): The machine is also equipped with a Human - Machine Interface (HMI), which provides a user - friendly interface for operators to interact with the control system. The HMI allows operators to monitor the machine's performance, set the operating parameters, and receive alerts in case of any malfunctions or issues.
Parameter | Description |
Blasting Chamber Dimensions | Customizable based on workpiece size, but commonly ranges from 2m x 1m x 1m to 10m x 3m x 2m (length x width x height) |
Maximum Workpiece Weight | Can range from 500 kg to several tons, depending on the machine design |
Blasting Power | Depends on the number and size of the blasting turbines, typically ranges from 20 kW to 200 kW |
Abrasive Media Type | Steel shots, ceramic beads, or other suitable abrasives; particle size usually ranges from 0.5mm to 3mm |
Conveyor Speed | Adjustable, usually in the range of 0.1m/min to 5m/min |
Abrasive Recycling Efficiency | Generally over 95%, depending on the quality of the recycling system |
Dust Collection Efficiency | High, typically over 99%, to meet environmental and safety standards |
Power Supply | Usually 3 - phase, 380V, 50Hz, but can be customized according to regional requirements |
Machine Weight | Varies depending on size and construction, but can range from 3 tons to 20 tons or more |
The roller conveyor shot blasting machine is designed to streamline the surface treatment of various workpieces by utilizing a continuous roller conveyor system. Workpieces are placed on the rollers, which transport them through a sealed blasting chamber. Inside the chamber, high - velocity abrasive media, such as steel shots or ceramic beads, is propelled onto the workpiece surfaces by powerful blasting turbines. The impact of the abrasive media effectively removes impurities like rust, scale, paint, and old coatings, while also enhancing the surface roughness to improve adhesion for subsequent processes.
This type of shot blasting machine is particularly well - suited for handling large - scale production runs and workpieces with irregular shapes or heavy weights. The continuous operation of the roller conveyor allows for a high throughput, making it an ideal choice for industries where efficiency and productivity are key.
the roller conveyor shot blasting machine is a versatile and efficient solution for surface treatment in various industries. Its advanced features, reliable components, and customizable parameters make it an ideal choice for improving the quality, durability, and appearance of industrial products. Whether it's for automotive manufacturing, aerospace applications, construction, or metal fabrication, this machine offers a cost - effective and high - performance solution for achieving superior surface treatment results.