Hotline
+86-136 8495 9862
Email:cennia@szmizhi.com
Add::104,Building 27,Third Industrial Zone, Longxi Community,Longgang District,Shenzhen,China.
Coil Forming & Handling Equipment
Surface Treatment Equipment
Solutions
Application
About Us
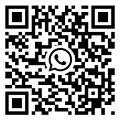
Welcome to MIZHI
For consultation/feedback, please call the service hotline: +86-136 8495 9862 Email:cennia@szmizhi.com
1.Coil Width: 100-1600 mm
2.Material Thickness: 0.4-4.5 mm
3.Yield Strength: ≤245 N/mm2
4.Tensile Strength: ≤392 N/mm2
5.Applicable Material:Raw Material Type: Hot-Rolled Metal steel, Cold-Rolled Metal steel, Galvanized Metal steel ,Stainless Steel etc.
When working with heavy stock or little space, Coil Feeding lines provide innovative,cost-effective coil processing solutions. Combining straightening and feeding makes a sometimes long coil loop in between Straightener and Servo Roll Feed. With our press feeding systems you can process coil material width from 400mm to 1600mm, coil thickness from 0.4-4.5mm, coil weight up to 10000kgs.
Coil Feeding Line offers to customers a complete product range for nearly all applications within the metal sheet stamping and metal forming industry, such as brake pads, front pillar, Seat slide rail, center pillar, flip wheel and so on.
AUTOMOTIVE
Manufacture of equipment for metal stamping of automotive parts. Structural car body parts and other parts like front brackets, brake pads, wipers, seat supports, electrical windows, exhaust pipes, catalytic converters, radiators, levers, pedals, gear box parts, wheels, damping supports, etc ...
BUILDING & HOUSEHOLD
Feeding lines to produce a variety of metal components for the building and household sector and derivatives. Parts like braces, clamps, straps, locks and hinges for doors,furniture hardware, knifes, cooking ware carpentry parts, metal supports, perforated plates, etc ..
HOME APPLIANCE & ElECTRONICS
Installations for the manufacture of parts for household appliances sector or white goods. Metal pieces like air conditioner parts, motor housings, doors,electric cabinet, shells and covers, trays, guides, caps, supports, brackets, handles, etc ...
ILLUMINATION
Many solutions for the blanking of metal parts for lighting sector. Several parts such as housings, panels, brackets, feet, arms, buttons, diffusers, etc ...
Space-saving, easy installation and low maintenance
Compact design is ideal for limited space metalworking stamping process.
The compact coil feed line is very easy to install without any pit. The advanced techniques with an integrated self-diagnosis control system, it can ensure machine stable and low failure. which maximum save the cost and protect the operator's safety.
Easy and smart operation
Our machine adopts PLC control, all process parameters of products to be stamping can be set up and saved in program means that there is no need to repeat input, also with the characteristic of high degree of automation, high operation safety, low maintenance. Reducing labor input and improve the production efficiency. Moreover, movable regulating handle is very convenient operation for installing and debugging when the machine is testing.
Advance Techniques
With the world’s leading automatic metal forming stamping techniques ,advanced and
humanized management system,we unite thousands of elites dedicated to the development of automatic press,including top engineers in this field,experienced technicians, production workers with fine craftsmanship to ensure every equipment produced durable ,high-efficiency and stable.
High precision straightening and feeding performance
With the coil inlet supporting arm assisting, the strip head will be inserting into the straightener part automatically and smoothly, and driven by gear transmission, the strips will be straightening and feeding forward.
The straightener roller and feeder roller mechanism are placed on the same precise platform to ensure the uniformity of parallel precision and to limit the error of leveling and feeding operation to the maximum extent.
Wide range of metal coil stamping application
Compact coil feeding line is design to make thick plate of auto parts stamping, such as brake pads, front pillar, Seat slide rail, center pillar, flip wheel and so on.
Also for hardware stamping parts, furniture and home appliances and so on.
Coil Car
Coil car is one of the optional devices for the customer, It is disposed on the side of the decoiler part, and can automatically feed the coil into the straightener-feeder accurately and fastly.
Coil car consists of a frame and a pallet fixed at the top of the rack. In order to prevent the coil from dumping or slipping during the uncoiling process, the pallet has a V-shape and is concavely facing upward.
The bottom of the rack is provided with a linear guide rail, and a moving mechanism for pushing the frame to walk and lift on the linear guide is provided between the linear guide and the frame.
Decoiler Parts
When the coils is place on the spindle, decoiler machine rotates intermittently to release the metal coil to metal strip, the support rollers on coil car will lead the strips into the straightener arm.
Pull-off Coil Reel with threading drive
Powered Straightener with threading system and loop control.
For continuous pull-off of coil material from Coil Reel into loop
Loop Bridge for threading of coil material from Straightener to Servo Feed
Spindle expansion range: Φ470-Φ520mm.
Decoiler is Driven is by AC motor with an inverter
Press arm pressure is driven by AC motor
Coil inlet support Arm
After uncoiling process, the support arm of decoiler machine will rise up and lead the material strips into coil inlet support arm which is driven by a hydraulic cylinder will close automatically to hold-down material strip when strip head touch the straightener part.
The bottom inlet roller is geared transmission, sharing drive power with straightener rollers. When upper inlet roller goes down, the two rollers clamp the metal strip and lead it to the straightening part. These two rollers are made by high quality bearing steel, with sandblasting treatment, hardness reaches HRC60±2.
High Precision Straightening and Feeding Parts
The straightener feeder parts is straightening the coil strips and feeding it into the stamping press and dies according to the fixed length controlled by PLC.
Given the difference in coil at the beginning of rollers and the end of roller, it is usually necessary for an operator to always be monitoring straightening operations, and to manually carry out corrections to ensure a high degree of precision in straightening. With the unique eccentric turbine worm adjustment by manual fitted on MFL3 Series coil straightener-feeder, changes in the coil strips thickness are detected during production.
Hydraulic cutting (Option)
A hydraulic shearing unit is used to cut the material heads and tails for productivity improvement and better stamping product quality. The hydraulic cutting unit has four sides scissors to achieve smooth cutting.It's operated by touch screen control and with manual scissors adjustment.
Automatic Lubrication Unit (Option)
Lubrication of steel strip before stamping will protect the stamping dies from damaging and prolonging the uselife. The automatic lubrication system is automatically controlled, with an oil loop recycling system, which will save oiling cost and prevent leakage.
Discharging Support Bracket
The outlet support bracket is used to deliver the straightening strips to press die smoothly. When the coil material is thin thickness or soft material , or the distance between straightener-feeder and stamping dies is long, the strip can not be delivered the strip head into the die successfully, the support bracket will help to reach it. The length of the support bracket is adjustable to meet different dimensions of stamping press machine and dies.
Model | MFL3-300 | MFL3-400 | MFL3-600 | MFL3-800 | MFL3-1000 |
Stock Width(mm) | 50-300 | 50-400 | 50-600 | 70-800 | 70-1000 |
Stock Thickness(mm) | 0.4-4.5 | ||||
Max.Coil Weight(kg) | 5000 | 5000 | 5000 | 5000/7000 | 7000 |
Max.Coil O.D.(mm) | Φ1400 | ||||
Coil I.D.(mm) | φ470-520 | ||||
Feed Length(mm) | ~500* | ||||
Max.Line Speed(m/min) | 16-24 | ||||
Straightener Rolls(piece) | φ68mm*7(upper4/ lower 3) | ||||
Feed Rolls(set) | φ88mm*2 (upper 1/ lower 1) | ||||
Main Motor | AC4.4 | AC4.4 | AC4.4 | AC5.5 | AC7.5 |
Mandrel Expansion | hydraulic | ||||
Reel Motor(kw) | 2.2 | 2.2 | 2.2 | 2.2 /3.7 | 3.7 |
Power(v) | 3 Phase 220V/380V/440V/50HZ | ||||
Operating Air(Mpa) | 0.49 |
Straightener Capacity( Yield strength σs≤245N/mm² ,Tensile strength σb≤392 N/mm²) | |||||||||
Model | Thickness | ||||||||
0.3-0.8 | 1 | 1.6 | 2 | 2.3 | 2.8 | 3.2 | 4.5 | ||
Width(mm) | MFL3-400 | 400 | 370 | 300 | 160 | ||||
MFL3-500 | 500 | 430 | 320 | 270 | 160 | ||||
MFL3-600 | 600 | 430 | 360 | 290 | 250 | 160 | |||
MFL3-800 | 800 | 480 | 370 | 320 | 250 | 220 | 150 | ||
MFL3-1000 | 1000 | 750 | 430 | 330 | 290 | 230 | 200 | 110 |