Hotline
+86-136 8495 9862
Email:cennia@szmizhi.com
Add::104,Building 27,Third Industrial Zone, Longxi Community,Longgang District,Shenzhen,China.
Coil Forming & Handling Equipment
Surface Treatment Equipment
Solutions
Application
About Us
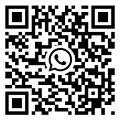
Welcome to MIZHI
For consultation/feedback, please call the service hotline: +86-136 8495 9862 Email:cennia@szmizhi.com
Tube forming rolls are key elements in the tube roll forming process, which is a specialized metal - forming technique used to produce seamless or welded tubes with high precision and efficiency. This process is widely applied in various industries, including automotive, aerospace, construction, and plumbing.
The tube roll forming process begins with a flat metal sheet, typically made of steel, aluminum, or other metals. The sheet is first fed into a series of forming rolls. These rolls are designed with specific grooves and contours that gradually bend the metal sheet into a tubular shape. Each roll in the sequence performs a small but incremental bending operation, ensuring a smooth and consistent transformation of the flat sheet into a tube. The number of rolls and their configuration depend on the complexity of the tube's shape and the diameter and wall thickness requirements.
Tube forming rolls are made from high - quality materials to withstand the significant forces and wear during the forming process. Common materials for these rolls include alloy steels, which offer a good balance of hardness, toughness, and wear resistance. In some cases, materials with enhanced properties, such as heat - treated tool steels or specialized alloys, may be used for more demanding applications. The surface of the rolls is often carefully finished to ensure smooth contact with the metal sheet, minimizing friction and preventing damage to the tube surface.
One of the main advantages of using tube forming rolls is the ability to produce tubes with tight tolerances. This is crucial in industries where precise dimensions are required, such as in the automotive industry for parts like exhaust systems and structural components. The consistent bending action of the rolls results in tubes with uniform wall thicknesses and accurate diameters. For example, in aerospace applications, where weight reduction and structural integrity are of utmost importance, tubes produced using tube forming rolls can be designed with specific wall thickness variations to meet the strength requirements while minimizing weight.
There are different types of tube forming rolls, depending on the type of tube being produced. For seamless tube production, the rolls are designed to gradually close the edges of the metal sheet without the need for welding. This is achieved through a series of carefully controlled bending operations that ensure a seamless join. In the case of welded tubes, the rolls are used to form the tube shape, and then a welding process, such as high - frequency induction welding or laser welding, is employed to seal the edges. Welding rolls may also be used to support and guide the tube during the welding process, ensuring proper alignment and a high - quality weld.
Maintenance of tube forming rolls is essential to ensure their long - term performance and the quality of the tubes produced. Regular inspection for signs of wear, such as groove erosion or surface roughness, is necessary. Wear can occur due to the continuous contact with the metal sheet and the high forces involved in the forming process. When wear is detected, the rolls may need to be re - ground or replaced. Re - grinding can restore the original shape and surface finish of the rolls, while replacement may be required if the wear is too severe. Additionally, proper lubrication of the rolls is crucial to reduce friction and wear. Lubricants are carefully selected based on the type of metal being formed and the operating conditions to ensure optimal performance.
In recent years, advancements in technology have led to the development of more sophisticated tube forming roll systems. Automated control systems are now commonly used to adjust the roll positions, speeds, and other parameters in real - time. This allows for greater flexibility in producing different tube sizes and shapes and improves the overall efficiency of the tube roll forming process.