Hotline
+86-136 8495 9862
Email:cennia@szmizhi.com
Add::104,Building 27,Third Industrial Zone, Longxi Community,Longgang District,Shenzhen,China.
Coil Forming & Handling Equipment
Surface Treatment Equipment
Solutions
Application
About Us
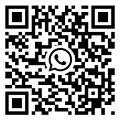
Welcome to MIZHI
For consultation/feedback, please call the service hotline: +86-136 8495 9862 Email:cennia@szmizhi.com
Steel roll forming machines are pivotal in the manufacturing landscape, playing a crucial role in transforming flat steel sheets into a diverse array of profiled products. These machines have revolutionized the production processes across multiple industries, from construction and automotive to furniture and appliances. Their significance lies in their ability to produce high - quality, consistent, and customized steel profiles with high efficiency and precision.
Working Principle of Steel Roll Forming Machines
1. Material Feeding
The process begins with the feeding of a continuous steel coil into the roll forming machine. The coil is typically placed on a coil reel or an uncoiler, which is designed to hold and unwind the steel sheet in a controlled manner. The uncoiler may be manual, semi - automatic, or fully automatic, depending on the scale of production and the level of automation desired. In large - scale manufacturing plants, fully - automatic uncoilers are often used, which can handle large - diameter coils weighing several tons. These uncoilers are equipped with sensors and control systems that ensure a steady and consistent feed of the steel sheet into the machine, maintaining the required tension to prevent wrinkling or sagging of the material.
2. Roll Forming Process
Once the steel sheet is fed into the machine, it passes through a series of roll stations. Each roll station consists of a pair of rollers, with one roller located above the steel sheet and the other below. The rollers are precisely designed and machined to gradually shape the steel sheet into the desired profile. As the steel sheet moves through the roll stations, the rollers apply pressure and bend the sheet in a sequential manner. For example, in the production of a simple C - channel profile, the first few roll stations may start by making gentle bends on the edges of the steel sheet, gradually increasing the angle of the bend in subsequent roll stations until the final C - shape is achieved. The number of roll stations required depends on the complexity of the profile. A more intricate profile, such as an automotive body part with multiple curves and bends, may require 10 - 15 roll stations, while a basic roofing panel profile may be formed with 4 - 6 roll stations.
3. Cut - Off and Finishing
After the steel sheet has been formed into the desired profile, it needs to be cut to the required length. This is typically done using a cut - off mechanism, which can be either a mechanical shear or a flying cut - off system. A mechanical shear operates by using a blade to cut the profile at a fixed point when the desired length has been reached. In contrast, a flying cut - off system moves in synchronization with the moving profile, allowing for precise cutting while the machine is in continuous operation. This is especially useful for high - speed production lines, as it reduces production downtime. Once cut, the profiles may undergo additional finishing processes, such as deburring to remove any sharp edges, painting or coating to enhance corrosion resistance and aesthetics, or perforating for specific applications like ventilation grilles.
Types of Steel Roll Forming Machines
1. Single - Purpose Roll Forming Machines
Single - purpose roll forming machines are designed to produce a specific type of steel profile. For example, a purlin roll forming machine is dedicated to manufacturing purlins, which are horizontal support members commonly used in construction. These machines are optimized for the particular shape and dimensions of purlins. They have a fixed set of roll stations configured to create the characteristic shape of purlins, such as Z - shaped or C - shaped purlins. Single - purpose roll forming machines are highly efficient for mass - producing a single type of profile, as they can be fine - tuned to achieve high - speed and high - precision production. They are often used in construction material manufacturing plants that specialize in producing large quantities of a specific profile for the building industry.
2. Multi - Purpose Roll Forming Machines
Multi - purpose roll forming machines offer greater flexibility as they can be adjusted to produce multiple types of steel profiles. These machines are equipped with interchangeable roll sets. By changing the roll sets, the machine can be reconfigured to produce different profiles. For instance, a multi - purpose roll forming machine can be used to produce both roofing panels and siding profiles. This type of machine is suitable for manufacturers who need to produce a variety of products in smaller quantities or for businesses that want to diversify their product lines without investing in multiple single - purpose machines. The ability to switch between different profiles requires a more sophisticated control system and may involve some downtime for roll set changes, but it provides significant versatility in production.
3. Custom - Built Roll Forming Machines
Custom - built roll forming machines are tailored to meet specific and unique production requirements. When a company has a highly specialized profile design that cannot be produced by standard machines, a custom - built machine is the solution. These machines are designed from the ground up, taking into account the exact dimensions, shape, and material properties of the desired profile. For example, in the automotive industry, a custom - built roll forming machine may be required to produce a specific body panel profile with complex curves and tight tolerances. The design and manufacturing of custom - built machines involve close collaboration between the machine manufacturer and the customer. The machine builder will conduct detailed engineering analysis, create custom - designed roll profiles, and integrate advanced control systems to ensure the machine can produce the desired profile accurately and efficiently.
Applications of Steel Roll Forming Machines
1. Construction Industry
In the construction industry, steel roll forming machines are used to produce a wide range of products. Roofing and siding panels are among the most common applications. Roll - formed roofing panels are lightweight, durable, and can be produced in various profiles, such as trapezoidal or corrugated, to provide excellent water - shedding properties. Siding panels, on the other hand, not only enhance the aesthetic appeal of buildings but also offer protection against the elements. Purlin and girt systems, which are crucial for providing structural support in buildings, are also produced using roll forming machines. These components are designed to be strong yet lightweight, allowing for easy installation and cost - effective construction. In addition, steel decking, which is used in multi - story buildings for flooring and as a formwork for concrete, is manufactured through roll forming processes. The use of roll - formed steel products in construction has increased significantly due to their high strength - to - weight ratio, corrosion resistance, and ease of installation.
2. Automotive Industry
The automotive industry relies on steel roll forming machines for the production of various components. Body panels, such as doors, hoods, and fenders, are often made using roll forming techniques. Roll - formed steel provides the necessary strength and rigidity to protect passengers in the event of a collision while also allowing for complex shaping to meet the design requirements of modern automobiles. Additionally, automotive frames and chassis components can be produced using roll forming machines. These components need to be highly precise and consistent in their dimensions to ensure proper fit and performance of the vehicle. The use of roll forming in the automotive industry helps to streamline the production process, reduce costs, and improve the overall quality of the vehicles.
3. Furniture and Appliance Manufacturing
In the furniture manufacturing sector, steel roll forming machines are used to create components such as chair frames, table legs, and cabinet handles. Roll - formed steel components offer durability and a modern aesthetic appeal. For example, metal chair frames can be produced with smooth curves and precise dimensions using roll forming, providing both comfort and stability. In the appliance industry, roll - formed steel is used for manufacturing parts such as refrigerator door frames, oven racks, and washing machine drums. These components need to be corrosion - resistant and have high strength to withstand the rigors of daily use. The ability to produce consistent and high - quality steel profiles using roll forming machines makes them an essential tool in the furniture and appliance manufacturing industries.
Advantages of Steel Roll Forming Machines
1. High - Speed and High - Volume Production
Steel roll forming machines are capable of high - speed production, which is essential for meeting the demands of large - scale manufacturing. In a continuous production process, these machines can produce linear feet of profiled steel per minute. For example, a modern roll forming machine in a roofing material production plant can produce up to 100 linear feet of roofing panels per minute. This high - speed production enables manufacturers to produce large volumes of products in a short time, reducing production lead times and increasing overall productivity. The continuous nature of the roll forming process also minimizes material waste, as the steel sheet is gradually formed into the desired profile without the need for excessive cutting and shaping operations.
2. Precision and Consistency
Roll forming machines offer a high level of precision in profile formation. The rollers are machined to tight tolerances, ensuring that each profile produced is identical in dimensions. This precision is crucial for applications where accurate fit is required, such as in the construction of pre - fabricated buildings or in the automotive industry. For example, in the production of automotive body panels, the roll - formed profiles need to have consistent dimensions within a few thousandths of an inch to ensure proper assembly. The use of advanced control systems, such as programmable logic controllers (PLCs), further enhances the precision of the roll forming process by precisely controlling the speed, position, and pressure of the rollers.
3. Cost - Effectiveness
Steel roll forming machines offer cost - effective production solutions. The high - speed production and low material waste contribute to overall cost savings. Additionally, once the initial investment in the machine and the tooling (roll sets) is made, the per - unit production cost decreases significantly with increased production volume. For small - to - medium - sized manufacturers, multi - purpose roll forming machines can be a cost - effective option as they can be used to produce a variety of products, reducing the need for multiple specialized machines. Moreover, the durability of roll - formed steel products often reduces maintenance and replacement costs over time, making them a cost - effective choice for end - users as well.
Challenges and Solutions in Steel Roll Forming
1. Tooling Wear and Maintenance
One of the main challenges in steel roll forming is tooling wear. The continuous contact between the steel sheet and the rollers, especially when working with hard or abrasive steel materials, can cause wear and tear on the roll surfaces. This can lead to a loss of precision in profile formation and may require frequent replacement of the roll sets. To address this issue, manufacturers use high - quality tool steels for the rollers, which are heat - treated to increase their hardness and wear resistance. Additionally, proper lubrication of the roll surfaces is essential. Specialized lubricants are used to reduce friction between the steel sheet and the rollers, minimizing wear. Regular maintenance and inspection of the roll sets are also crucial. Manufacturers often have a preventive maintenance schedule in place, which includes checking for signs of wear, measuring the dimensions of the roll surfaces, and replacing worn - out components in a timely manner.
2. Material Compatibility and Springback
Different types of steel have varying mechanical properties, and ensuring material compatibility with the roll forming process can be a challenge. Some steels may be more prone to springback, which is the tendency of the formed profile to return to its original shape to some extent after the forming process. Springback can affect the accuracy of the final product. To overcome this, manufacturers use advanced simulation software to predict springback behavior for different steel materials and profile designs. Based on the simulation results, adjustments can be made to the roll profiles, the forming sequence, or the process parameters, such as the amount of pre - stress applied to the steel sheet. Additionally, post - forming operations, such as stretch - leveling or shot peening, can be used to reduce springback and improve the dimensional accuracy of the profiles.
Future Trends in Steel Roll Forming Machines
1. Automation and Industry 4.0 Integration
The future of steel roll forming machines lies in increased automation and integration with Industry 4.0 concepts. Fully automated roll forming lines are becoming more prevalent, with robots handling tasks such as coil loading, material feeding, and finished product stacking. These automated systems are equipped with sensors and control systems that can monitor and adjust the production process in real - time. For example, sensors can detect any variations in the thickness or quality of the steel sheet and automatically adjust the roll pressure or speed to ensure consistent profile formation. Integration with Industry 4.0 also enables remote monitoring and control of the roll forming machines. Manufacturers can access production data, such as production rates, machine performance, and quality metrics, from anywhere in the world, allowing for more efficient production management and quick response to any issues.
2. Advanced Material Processing
As new and advanced steel materials are developed, roll forming machines will need to adapt to process these materials. High - strength, lightweight steels, as well as steels with special properties such as corrosion resistance or heat resistance, are being increasingly used in various industries. Roll forming machines will require new tooling designs and process parameters to effectively form these advanced materials. For example, the development of advanced high - strength steels (AHSS) for the automotive industry has led to the need for roll forming machines with more powerful drive systems and improved roll materials to handle the higher strength and toughness of these steels. Research is also being conducted on innovative ways to form complex profiles using new material combinations, such as composite materials that combine steel with other materials like polymers or ceramics.
3. Sustainable and Energy - Efficient Solutions
Sustainability and energy efficiency are becoming key considerations in the design and operation of steel roll forming machines. Manufacturers are focusing on reducing energy consumption during the roll forming process. This can be achieved through the use of energy - efficient motors, improved drive systems, and optimized process parameters. For example, variable - frequency drives can be used to adjust the speed of the motors based on the actual production requirements, reducing energy waste. Additionally, efforts are being made to develop more sustainable production methods, such as using recycled steel materials and reducing material waste. The development of closed - loop production systems, where waste materials are recycled and reused within the production process, is also an area of growing interest in the steel roll forming industry.
In conclusion, steel roll forming machines are integral to modern manufacturing, with a wide range of applications across multiple industries. Their ability to produce high - quality, customized steel profiles with high efficiency and precision makes them a valuable asset. While challenges such as tooling wear and material compatibility exist, solutions are constantly being developed. Looking to the future, the industry is set to witness significant advancements in automation, material processing, and sustainability, further enhancing the capabilities and importance of steel roll forming machines.