Hotline
+86-136 8495 9862
Email:cennia@szmizhi.com
Add::104,Building 27,Third Industrial Zone, Longxi Community,Longgang District,Shenzhen,China.
Coil Forming & Handling Equipment
Surface Treatment Equipment
Solutions
Application
About Us
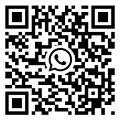
Welcome to MIZHI
For consultation/feedback, please call the service hotline: +86-136 8495 9862 Email:cennia@szmizhi.com
Roll forming dies are essential components in the roll forming process, which is a widely used method for manufacturing long, continuous metal profiles with consistent cross - sections. These dies play a crucial role in shaping flat metal coils or sheets into various desired shapes, such as channels, angles, and complex custom profiles.
The design of roll forming dies is highly intricate and demands precision engineering. Engineers must consider multiple factors, including the type of material being formed (such as steel, aluminum, or stainless steel), the desired final shape of the profile, and the production volume. Different materials have distinct mechanical properties, like hardness, ductility, and yield strength. For example, steel is strong and commonly used in construction for its durability, but it may require more robust die designs to withstand the high forces during forming. Aluminum, on the other hand, is lighter and more malleable, allowing for more delicate die designs in some cases.
The manufacturing process of roll forming dies involves several steps. High - quality tool steels are often selected as the base material for the dies due to their excellent wear resistance and toughness. These steels are then machined using advanced techniques such as computer - numerical - control (CNC) machining. CNC machining ensures that the dies are produced with extremely tight tolerances, which is vital for achieving consistent and accurate profile shapes. After machining, the dies may undergo heat treatment processes to further enhance their hardness and wear resistance. This helps to extend the lifespan of the dies, especially when used in high - volume production environments where they are subjected to repeated stress and friction.
There are different types of roll forming dies, each tailored to specific applications. For simple profiles like basic channels or angles, single - stage dies may be sufficient. These dies consist of a set of rolls that gradually bend the metal sheet into the desired shape in a single pass. However, for more complex profiles, multi - stage dies are required. Multi - stage dies are a series of roll sets, with each set performing a specific incremental bending operation. This step - by - step approach allows for the creation of intricate shapes that would be impossible to achieve with a single - stage die.
Maintenance of roll forming dies is of utmost importance. Regular inspection is necessary to detect any signs of wear, such as surface roughness or cracks. Worn - out dies can lead to inconsistent profile shapes, reduced product quality, and increased scrap rates. When wear is detected, the dies may need to be refurbished or replaced. Refurbishment can involve processes like grinding and re - polishing to restore the die's surface finish and dimensional accuracy. In some cases, damaged areas may be repaired using welding techniques, followed by machining to ensure proper fit and function.
In the modern manufacturing landscape, with the increasing demand for high - quality, customized metal profiles, roll forming die technology continues to evolve. Advanced simulation software is now being used in the design phase to predict the forming process and optimize die designs. This reduces the need for costly trial - and - error testing and speeds up the time - to - market for new products. Additionally, the development of new materials and coatings for dies is ongoing, aiming to further improve their performance and lifespan.