Hotline
+86-136 8495 9862
Email:cennia@szmizhi.com
Add::104,Building 27,Third Industrial Zone, Longxi Community,Longgang District,Shenzhen,China.
Coil Forming & Handling Equipment
Surface Treatment Equipment
Solutions
Application
About Us
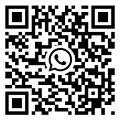
Welcome to MIZHI
For consultation/feedback, please call the service hotline: +86-136 8495 9862 Email:cennia@szmizhi.com
Drum blast machines are a type of industrial equipment that is specifically designed for the surface treatment of small - to medium - sized parts. These machines are widely used in industries such as automotive, aerospace, metalworking, and foundries, where the cleaning, deburring, and surface finishing of components are essential processes.
The basic principle of a drum blast machine involves placing the parts to be treated inside a rotating drum. Abrasive media, which can be in the form of steel shot, steel grit, or other suitable materials, is then introduced into the drum. As the drum rotates, the parts tumble and are continuously bombarded by the abrasive media. This impact action effectively removes contaminants such as rust, scale, and old coatings from the surface of the parts. At the same time, it can also smooth out rough edges, deburr the parts, and create a uniform surface finish.
One of the significant advantages of drum blast machines is their ability to process multiple parts simultaneously. The rotating drum allows for thorough and consistent treatment of all the components inside, ensuring that each part receives an even amount of abrasive impact. This makes them highly efficient for mass - production environments where a large number of similar parts need to be processed in a short period.
Drum blast machines come in various sizes and configurations to accommodate different part sizes and production requirements. Some models have adjustable drum speeds, which can be set according to the type and hardness of the parts being processed. By controlling the drum speed, operators can optimize the blasting process to achieve the desired surface finish without causing excessive damage to the parts.
Another important feature of drum blast machines is their dust collection system. During the blasting process, a significant amount of dust is generated as the abrasive media impacts the parts. A well - designed dust collection system is essential to capture this dust, ensuring a clean and safe working environment. It also helps to prevent the dust from interfering with the blasting process and affecting the quality of the finished parts.
Maintenance of drum blast machines is relatively straightforward. Regular inspection of the drum, abrasive delivery system, and dust collection components is necessary to ensure proper operation. The abrasive media also needs to be periodically replenished or replaced as it wears out over time. Additionally, the parts inside the drum should be loaded and unloaded carefully to avoid damage to the machine and ensure consistent treatment results.
In recent years, drum blast machines have also incorporated advanced technologies to improve their performance. For example, some models are equipped with automated controls that can monitor and adjust the blasting process in real - time. These controls can detect changes in the part load, abrasive flow, and other parameters, and make the necessary adjustments to maintain optimal performance. This not only increases the efficiency of the machine but also reduces the need for constant operator supervision.