Hotline
+86-136 8495 9862
Email:cennia@szmizhi.com
Add::104,Building 27,Third Industrial Zone, Longxi Community,Longgang District,Shenzhen,China.
Coil Forming & Handling Equipment
Surface Treatment Equipment
Solutions
Application
About Us
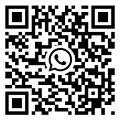
Welcome to MIZHI
For consultation/feedback, please call the service hotline: +86-136 8495 9862 Email:cennia@szmizhi.com
A rotoblast machine is a highly specialized and efficient piece of equipment used primarily for surface preparation and finishing tasks. This type of machine is based on the principle of centrifugal force, where abrasive media is accelerated by a high - speed rotating wheel and propelled onto the surface of the workpiece.
The key component of a rotoblast machine is the impeller or wheel assembly. The wheel rotates at extremely high speeds, typically in the range of several thousand revolutions per minute. As the abrasive media is fed into the center of the wheel, it is caught by vanes or blades and then thrown outward at high velocity. This high - energy impact of the abrasive on the workpiece surface effectively removes rust, paint, scale, and other contaminants, as well as prepares the surface for subsequent processes such as painting, coating, or plating.
Rotoblast machines offer several distinct advantages over other blasting methods. Firstly, they provide a high - productivity solution. The high - speed rotation of the wheel allows for a large volume of abrasive to be projected onto the workpiece in a short time, enabling the treatment of large surface areas quickly. This makes them ideal for industrial applications where high - volume production is required, such as in the manufacturing of automotive parts, structural steel, and machinery components.
Secondly, rotoblast machines offer excellent control over the surface finish. By adjusting parameters such as the type of abrasive media, wheel speed, and abrasive flow rate, operators can achieve a wide range of surface profiles, from a smooth finish for aesthetic purposes to a rough, textured surface for enhanced adhesion of coatings. This versatility makes rotoblast machines suitable for a diverse range of industries with different surface treatment requirements.
The design of rotoblast machines also takes into account safety and environmental considerations. Most models are equipped with robust enclosures to contain the abrasive and prevent it from scattering into the surrounding area. Additionally, efficient dust collection systems are integrated into the machine to capture the dust generated during the blasting process. This helps to maintain a clean and safe working environment for operators and also complies with environmental regulations regarding dust emissions.
In terms of maintenance, although rotoblast machines have complex mechanical components, modern designs have made them more reliable and easier to service. Regular inspection of the wheel assembly, abrasive delivery system, and dust collection components is necessary to ensure proper operation. The wear - and - tear parts, such as the wheel blades and hoses, need to be replaced periodically to maintain the machine's performance.
Furthermore, with the development of automation technology, many rotoblast machines can now be integrated into automated production lines. This allows for seamless operation, where workpieces can be automatically loaded into the machine, processed, and then unloaded without the need for extensive manual intervention. This not only increases production efficiency but also reduces the potential for human error in the blasting process.