Hotline
+86-136 8495 9862
Email:cennia@szmizhi.com
Add::104,Building 27,Third Industrial Zone, Longxi Community,Longgang District,Shenzhen,China.
Coil Forming & Handling Equipment
Surface Treatment Equipment
Solutions
Application
About Us
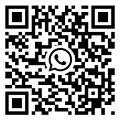
Welcome to MIZHI
For consultation/feedback, please call the service hotline: +86-136 8495 9862 Email:cennia@szmizhi.com
In the dynamic landscape of industrial manufacturing and metal processing, the wire rod shot blasting machine has emerged as an essential and highly effective piece of equipment. This in - depth exploration will cover its introduction, diverse applications, distinct features, integral components, and fundamental parameters.
Steel and Metalworking Industries
Wire Rod Manufacturing: In the production of wire rods, shot blasting is an integral step. Newly manufactured wire rods often have mill scale and other surface imperfections. By subjecting them to shot blasting, the scale is removed, and the surface is made smooth. This not only improves the appearance of the wire rod but also enhances its mechanical properties. For example, in the production of high - carbon steel wire rods used for making springs, shot blasting helps in relieving internal stresses and improving the fatigue resistance of the wire.
Forging and Stamping Operations: Before wire rods are used in forging or stamping processes, they need to have a clean and smooth surface. Shot blasting ensures that the wire rods are free from contaminants, which can otherwise cause defects in the forged or stamped products. In the manufacturing of metal fasteners like bolts and nuts, where the wire rod is cold - headed into the desired shape, a clean surface obtained through shot blasting is crucial for a successful forming process.
Automotive and Aerospace Sectors
Automotive Component Manufacturing: Wire rods are used in the production of various automotive components, such as suspension springs, valve springs, and transmission parts. Shot blasting these wire rods before further processing improves their surface quality, which in turn affects the performance and durability of the final automotive components. For instance, shot - blasted wire rods used in suspension springs can better withstand the repeated stress and vibration experienced in vehicle operation, leading to a more comfortable and reliable ride.
Aerospace Applications: In the aerospace industry, the quality and reliability of components are of utmost importance. Wire rods used in aircraft structures, engine components, and landing gear systems are shot blasted to achieve a high - quality surface finish. This helps in preventing corrosion, improving fatigue life, and ensuring the overall safety and performance of the aircraft. The stringent quality requirements of the aerospace sector make shot blasting an essential process for wire rod preparation.
Construction and Infrastructure
Reinforcement Bar Production: Wire rods are often used to produce reinforcement bars (rebar) for concrete structures. Shot blasting the wire rods before they are processed into rebar helps in improving the bond between the steel and the concrete. By removing rust and scale, the surface of the wire rod becomes more receptive to the concrete, resulting in a stronger and more durable concrete - steel composite. This is particularly important in large - scale infrastructure projects such as bridges, high - rise buildings, and dams.
Wire Rope Manufacturing: Wire ropes are widely used in construction for lifting and hoisting operations. The wire rods used to make these ropes are shot blasted to enhance their strength and resistance to wear. A clean and well - treated wire rod surface ensures that the individual wires in the rope can work together effectively, reducing the risk of breakage during use.
Other Industrial Applications
Electrical and Telecommunications: In the production of electrical conductors and cables, wire rods are sometimes used. Shot blasting can be applied to these wire rods to improve their electrical conductivity by removing any surface impurities that may impede the flow of electricity. In the telecommunications industry, wire rods used for manufacturing cables for signal transmission also benefit from shot blasting to ensure consistent signal quality.
Manufacturing of Hand Tools and Hardware: Wire rods are used to make a variety of hand tools like pliers, wrenches, and screwdrivers. Shot blasting the wire rods before forming these tools helps in creating a better surface finish, which is not only aesthetically pleasing but also improves the grip and durability of the tools. In the hardware industry, wire rods used for making nails, screws, and hooks are also shot blasted to enhance their quality.
Features
1. High - Speed and Efficient Blasting
Wire rod shot blasting machines are designed to operate at high speeds, allowing for rapid treatment of wire rods. The high - velocity impact of the abrasive media enables quick removal of even stubborn contaminants. Some advanced machines are equipped with multiple blasting wheels or nozzles arranged in a way that maximizes the coverage area, significantly reducing the time required to treat a large quantity of wire rods. For example, in a high - volume wire rod production facility, a machine with multiple blasting stations can process thousands of meters of wire rod per hour.
2. Precision and Uniformity
These machines are engineered to provide a high level of precision in the blasting process. The design ensures that the abrasive media is evenly distributed across the surface of the wire rod, resulting in a uniform surface finish. This is crucial as any uneven treatment can lead to variations in the quality of the final product. Specialized mechanisms are often in place to control the speed and movement of the wire rod as it passes through the blasting area, ensuring that every part of the wire rod receives the same level of treatment.
3. Adjustable Process Parameters
Wire rod shot blasting machines offer a wide range of adjustable parameters. Operators can control the blasting pressure, which determines the force with which the abrasive media hits the wire rod. The flow rate of the abrasive media can also be adjusted, allowing for customization based on the type of wire rod material, the thickness of the contaminants, and the desired surface finish. Additionally, the speed at which the wire rod is conveyed through the blasting area can be varied. For instance, for a thin - walled or delicate wire rod, a lower blasting pressure and a slower conveyor speed may be selected to avoid damage, while for a thick - walled wire rod with heavy scale, higher pressure and a faster conveyor speed can be used.
4. Abrasive Recycling and Cost - Efficiency
Modern wire rod shot blasting machines are equipped with efficient abrasive recycling systems. After the abrasive media has been used to blast the wire rod, it is collected, separated from the debris, and recycled for further use. This significantly reduces the cost of operation as new abrasive media does not need to be constantly purchased. The recycling system typically includes a series of screens, cyclones, and conveyors that work together to clean and sort the abrasive media. Some machines can achieve an abrasive recycling rate of up to 95%, making them highly cost - effective in the long run.
5. Automated and User - Friendly Operation
Many wire rod shot blasting machines are designed with automation in mind. Automated control systems can be programmed to perform specific blasting operations based on pre - set parameters. This reduces the need for manual intervention and ensures consistent results. The control panels are often user - friendly, with clear displays and intuitive interfaces that allow operators to easily adjust the machine settings, monitor the blasting process, and receive alerts in case of any malfunctions. This automation not only improves the efficiency of the operation but also reduces the risk of human error.
1. Blasting Chamber
The blasting chamber is the central component of the wire rod shot blasting machine. It is where the actual shot blasting process takes place. The chamber is constructed from high - strength materials, usually thick - walled steel plates, to withstand the continuous impact of the abrasive media. To further enhance its durability, the chamber may be lined with wear - resistant materials such as manganese steel or rubber. The chamber is designed to be airtight, preventing the escape of abrasive particles and dust, which not only ensures a safe working environment but also improves the efficiency of the blasting process. It is equipped with access doors for maintenance and inspection purposes and openings for the entry and exit of the wire rod.
2. Blasting Wheels or Nozzles
Blasting Wheels: In some wire rod shot blasting machines, rotating blasting wheels are used to accelerate the abrasive media. These wheels are driven by powerful electric motors. The wheels have specially designed vanes that pick up the abrasive particles from a feed system and then throw them at high speeds towards the wire rod. The number and position of the blasting wheels can be adjusted according to the diameter and length of the wire rod and the desired blasting pattern. For example, in a machine designed to treat a wide range of wire rod diameters, the blasting wheels can be repositioned to ensure optimal coverage.
Nozzles: Other machines use nozzles to direct the abrasive media. Compressed air or a combination of compressed air and mechanical force is used to propel the media through the nozzles. The nozzles are made of wear - resistant materials such as tungsten carbide to withstand the high - velocity flow of the abrasive. They can be adjusted in terms of their angle, distance from the wire rod, and the size of the orifice through which the abrasive is ejected. This allows for precise control of the blasting intensity and direction.
3. Abrasive Feeding System
The abrasive feeding system is responsible for supplying the abrasive media to the blasting wheels or nozzles. It consists of a hopper, which stores the abrasive, and a feeding mechanism. The feeding mechanism can be a screw conveyor, a vibrating feeder, or a pneumatic feeder. The choice of feeder depends on the type of abrasive media and the requirements of the blasting process. The feeding system is designed to provide a consistent and adjustable flow of abrasive media to ensure a continuous and efficient blasting operation. Sensors are often installed in the hopper to monitor the level of abrasive media, and an automatic refill system can be integrated to prevent interruption of the blasting process due to low abrasive levels.
4. Wire Rod Conveyor System
The wire rod conveyor system is used to move the wire rod through the blasting chamber. It can be designed in various configurations, such as a roller conveyor, a chain conveyor, or a belt conveyor. The conveyor speed is adjustable, allowing for precise control of the time the wire rod spends in the blasting area. The conveyor system is also equipped with guides and supports to ensure that the wire rod remains in the correct position as it passes through the blasting chamber. For long - length wire rods, special conveyor systems with additional support points may be used to prevent sagging or misalignment during the blasting process.
5. Dust Collection System
A highly efficient dust collection system is an essential component of a wire rod shot blasting machine. During the blasting process, fine dust particles and small abrasive fragments are generated. The dust collection system is designed to capture these particles and prevent them from being released into the environment. It typically consists of a series of filters, cyclones, and fans. The fans draw in the air from the blasting chamber, which contains the dust and particles. The cyclones first separate the larger particles, and then the remaining fine dust is captured by the filters. The collected dust is then removed from the system for proper disposal. Some advanced dust collection systems are designed to meet strict environmental regulations, ensuring that the emissions from the shot blasting process are well within acceptable limits.
6. Control and Monitoring System
The control and monitoring system of a wire rod shot blasting machine is responsible for regulating the various functions of the machine. It includes a control panel that allows the operator to set and adjust parameters such as blasting pressure, abrasive flow rate, conveyor speed, and the operation of the dust collection system. The control panel may also have indicators to show the status of the machine, such as the temperature of the motors, the level of abrasive in the hopper, and the pressure in the compressed - air system (if applicable). Additionally, sensors are installed at various points in the machine to monitor the performance and detect any anomalies. For example, sensors can detect if the wire rod has deviated from its intended path or if there is a blockage in the abrasive feeding system. In case of any problems, the control system can trigger an alarm and, in some cases, automatically shut down the machine to prevent damage.
Parameter | Description | Example Values |
Wire Rod Diameter Range | The minimum and maximum diameters of wire rods that the machine can handle | φ5 - φ50 mm |
Wire Rod Length Range | The minimum and maximum lengths of wire rods that can be processed | 1 - 30 m |
Blasting Pressure (for air - driven systems) | The pressure at which the abrasive media is propelled | 0.4 - 0.7 MPa |
Abrasive Media Flow Rate | The amount of abrasive media fed per unit time | 30 - 150 kg/min |
Conveyor Speed | The speed at which the wire rod is moved through the blasting chamber | 0.3 - 3 m/min |
Power Consumption | The total electrical power consumed by the machine | 5 - 50 kW |
Abrasive Recycling Rate | The percentage of abrasive media that can be recycled and reused | 80 - 95% |
Dust Emission Standard | The maximum allowable amount of dust emitted into the environment | < 10 mg/m³ |
A wire rod shot blasting machine is engineered to perform a series of crucial surface treatment operations on wire rods. These operations primarily involve cleaning, descaling, and surface preparation. The machine functions by propelling a high - velocity stream of abrasive materials, such as steel shots or grits, onto the surface of the wire rod. The impact of these abrasive particles effectively removes rust, scale, mill scale, and other contaminants that may have formed on the wire rod during its manufacturing or storage process.
The working principle of a wire rod shot blasting machine typically begins with a power - driven mechanism. This can be an electric motor or a compressed - air - based system. The power source drives a mechanism that accelerates the abrasive media. Once accelerated, the abrasive is directed towards the wire rod through precisely designed nozzles or rotating wheels, depending on the machine's design. As the wire rod moves through the blasting area, either continuously or in batches, all its surfaces are uniformly exposed to the abrasive impact, ensuring a comprehensive treatment.
the wire rod shot blasting machine plays a pivotal role in multiple industries by providing a reliable and efficient method for surface treatment of wire rods. Its wide range of applications, advanced features, well - designed components, and adjustable parameters make it an indispensable tool for ensuring the quality and performance of wire - rod - based products.