Hotline
+86-136 8495 9862
Email:cennia@szmizhi.com
Add::104,Building 27,Third Industrial Zone, Longxi Community,Longgang District,Shenzhen,China.
Coil Forming & Handling Equipment
Surface Treatment Equipment
Solutions
Application
About Us
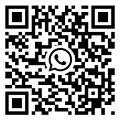
Welcome to MIZHI
For consultation/feedback, please call the service hotline: +86-136 8495 9862 Email:cennia@szmizhi.com
A used slitting line offers an affordable alternative to new equipment for businesses seeking to enter metal processing or expand their capabilities without a high upfront investment. These preowned systems, which range from basic manual lines to advanced automated systems, can be refurbished or retrofitted to meet modern production demands. While used equipment requires careful evaluation, it provides significant cost savings and flexibility for small to mediumsized enterprises (SMEs) or startups.
Benefits of Investing in a Used Slitting Line
1. Cost Savings:
Used slitting lines typically cost 30–70% less than new systems, depending on age, condition, and technology. This makes them accessible to businesses with limited budgets, allowing them to allocate funds to other areas like tooling or training.
2. Proven Technology:
Older models often feature robust mechanical designs that have withstood the test of time. Many used lines from reputable manufacturers (e.g., FIMI, Athader) can still deliver reliable performance for basic to mediumduty applications.
3. Quick Availability:
Unlike new lines, which may have long lead times for production and delivery, used systems can be purchased and installed within weeks, enabling faster timetomarket for new products.
4. Retrofitting Opportunities:
Used lines can be upgraded with modern components, such as CNC controls, laser measurement systems, or automated safety features, to enhance precision and efficiency. For example, adding a PLC interface to an older mechanical line can improve programmability and reduce operator error.
Key Considerations When Purchasing a Used Slitting Line
1. Condition Assessment:
Mechanical Inspection: Check for wear on critical components like slitting knives, bearings, rollers, and hydraulic systems. Look for signs of corrosion, misalignment, or excessive vibration.
Electrical and Control Systems: Older electrical panels may use obsolete components, requiring replacement to ensure compatibility with modern safety standards and software.
Production History: Request maintenance records and production logs to gauge usage intensity. A line that primarily processed thin aluminum will have less wear than one used for heavy steel.
2. Material and Process Compatibility:
Ensure the line is rated for your target materials (e.g., steel, aluminum, copper) and thickness range. For example, a used line designed for 3 mm steel may not handle the 8 mm thickness needed for your project without costly upgrades.
3. Tooling and Accessories:
Verify that the line includes essential tooling, such as slitting knives, spacers, and recoil cores. Missing or worn tooling can add unexpected costs, as custom knives may need to be ordered from the manufacturer.
4. Supplier Reputation and Support:
Purchase from reputable dealers or direct sellers who offer warranties, technical support, and spare parts availability. Avoid unbranded or poorly documented systems, as they may be difficult to repair or upgrade.
Refurbishment and Upgrades
Basic Refurbishment:
Involves cleaning, painting, replacing worn seals and bearings, and calibrating mechanical components. This can extend the lifespan of the line and improve reliability.
Technological Upgrades:
Automation Retrofits: Adding CNC controls or IoT sensors to monitor performance and predict maintenance needs.
Safety Enhancements: Installing emergency stop systems, guarding, or light curtains to meet OSHA or CE standards.
Energy Efficiency Upgrades: Replacing old motors with energyefficient models or adding variable frequency drives (VFDs) to reduce power consumption.
Risks and Mitigation
Obsolescence: Older control systems may lack compatibility with modern software, limiting integration with Industry 4.0 initiatives. Mitigate by prioritizing lines with upgradable PLCs or openarchitecture controls.
Limited Warranty: Used equipment often has shorter or no warranties. Negotiate a postpurchase service contract with the seller to cover unexpected repairs.
Logistics and Installation: Heavy slitting lines require specialized rigging and electrical setup. Ensure the supplier provides installation support or recommend qualified technicians.
In conclusion, a used slitting line can be a strategic investment for businesses looking to balance cost and performance. By conducting thorough due diligence and partnering with reliable suppliers, buyers can acquire a functional, refurbished system that meets their production needs while staying within budget.