Hotline
+86-136 8495 9862
Email:cennia@szmizhi.com
Add::104,Building 27,Third Industrial Zone, Longxi Community,Longgang District,Shenzhen,China.
Coil Forming & Handling Equipment
Surface Treatment Equipment
Solutions
Application
About Us
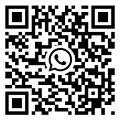
Welcome to MIZHI
For consultation/feedback, please call the service hotline: +86-136 8495 9862 Email:cennia@szmizhi.com
A steel slitting line is a specialized industrial system designed to cut wide metal coils into narrower strips with high precision, serving as a critical component in the steel processing industry. This technology is essential for producing strips used in downstream applications such as roll forming, stamping, welding, and wire drawing. By combining uncoiling, slitting, and recoiling into a single automated process, steel slitting lines optimize material utilization and enable the production of customwidth strips for diverse industries.
Key Components and Operation
1. Uncoiling System:
The process begins with an uncoiler, which holds the master steel coil (ranging from 5 to 30 tons or more) and feeds it into the line at a controlled speed. Hydraulic or motordriven uncoilers feature tension control to prevent wrinkling or misalignment, ensuring smooth material flow.
2. Slitting Section:
The core of the line is the slitting unit, which consists of:
Slitting Knives: Circular blades (upper and lower) that shear the steel into multiple strips. The spacing between knives determines the width of each strip, with precision adjustable to within ±0.1 mm. Hardened steel or tungsten carbide blades are used for durability, especially when processing highstrength steel.
Edge Trimmers: Optional components that remove burrs or uneven edges from the master coil before slitting, ensuring clean strip edges.
Spacer Rings: Used to separate the slitting knives and maintain consistent strip widths. Quickchange tooling systems allow for rapid adjustments between different strip widths, reducing downtime.
3. Guiding and Tension Control:
After slitting, strips pass through guide rollers and tension bridges to keep them aligned and prevent wandering. Tension control is critical to maintain strip flatness and prevent stretching, especially for thingauge materials.
4. Recoiling System:
Each slit strip is recoiled onto individual cores, forming neat, compact coils. Recoilers can handle multiple strips simultaneously, with each coil weighed and labeled for traceability. Automated stackers may then palletize the finished coils for shipment.
5. Control System:
A PLC or CNC interface manages the entire process, allowing operators to input desired strip widths, blade spacing, and production speed. Modern systems include realtime monitoring via cameras or laser sensors to detect edge defects or width variations, enabling immediate adjustments.
Applications and Materials
Steel slitting lines are used to process various ferrous materials:
Carbon Steel: Common in construction, automotive, and general manufacturing for components like rebar, pipes, and structural sections.
Stainless Steel: Used in aerospace, medical, and food industries for corrosionresistant strips in tubing, appliances, and surgical instruments.
Galvanized Steel: Popular for roofing, fencing, and automotive body panels due to its anticorrosive properties.
HighStrength LowAlloy (HSLA) Steel: Processed for heavyduty applications like truck frames, oil pipelines, and machinery parts.
For example, in the automotive industry, a slitting line might cut 500 mm wide galvanized steel coils into 50 mm strips for producing seat rails, while a stainless steel slitting line could create 10 mm strips for medical device springs.
Advantages of Steel Slitting Lines
1. Precision and Consistency:
Strip width tolerances as tight as ±0.3 mm and edge straightness within 0.5 mm/m ensure uniformity, critical for applications requiring precise fitment in subsequent processes.
2. Material Efficiency:
Minimizes scrap by optimizing knife spacing to utilize the entire width of the master coil. For example, a 1250 mm wide coil can be slit into (e.g.) five 250 mm strips with minimal edge waste.
3. Flexibility:
Adaptable to a wide range of strip widths (from 10 mm to over 1000 mm) and thicknesses (0.1 mm to 12 mm), making it suitable for both thin foil and heavy plate applications.
4. High Throughput:
Modern lines can process coils at speeds up to 200 meters per minute, significantly increasing productivity compared to manual cutting methods.
Challenges and Maintenance
Blade Wear: Slitting knives require regular sharpening or replacement, especially when processing hard materials. Automated blade detection systems can monitor wear and schedule maintenance.
Tension Management: Improper tension can cause strip stretching or sagging, necessitating careful calibration based on material properties.
Dust and Debris: Steel slitting generates metal fines, which must be managed via integrated dust collection systems to prevent equipment damage and ensure operator safety.
In summary, steel slitting lines are indispensable for transforming raw steel coils into precisionengineered strips, driving efficiency and quality in modern manufacturing. Their ability to handle diverse materials and produce custom widths at scale makes them a cornerstone of the steel processing industry.