Hotline
+86-136 8495 9862
Email:cennia@szmizhi.com
Add::104,Building 27,Third Industrial Zone, Longxi Community,Longgang District,Shenzhen,China.
Coil Forming & Handling Equipment
Surface Treatment Equipment
Solutions
Application
About Us
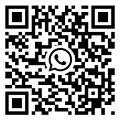
Welcome to MIZHI
For consultation/feedback, please call the service hotline: +86-136 8495 9862 Email:cennia@szmizhi.com
A slitting line machine is a crucial piece of equipment in the metalworking and manufacturing industries. Its primary function is to transform large metal coils into narrower strips or coils of smaller widths, making the material more suitable for a wide range of applications. This process, known as slitting, is essential for industries such as automotive parts production, construction materials manufacturing, and general metal fabrication.
The slitting line machine typically begins with an uncoiler. This component holds the large metal coil and carefully feeds it into the rest of the machine. Uncoilers can vary in design; some are manual, where an operator has to physically adjust and control the uncoiling process, while others are fully automatic. Automatic uncoilers are often preferred in high volume production settings as they can operate continuously and precisely, reducing the need for constant operator intervention. They are designed to handle different coil sizes and weights, ensuring a smooth and consistent feed of the metal strip into the machine.
Before the slitting process, some slitting line machines incorporate straightening and leveling units. These units play a vital role in ensuring that the metal strip is flat and even. When metal coils are produced, they may have some natural curvature or unevenness. If the strip is not straightened and leveled before slitting, it can lead to inaccurate cuts and inconsistent strip widths. The straightening and leveling units use a series of rollers and adjustment mechanisms to apply the right amount of force to the metal strip, flattening it out and making it suitable for the slitting operation. This step is particularly important when the end product requires high precision dimensions, such as in the case of parts for the aerospace or electronics industries.
The heart of the slitting line machine is the slitter head. The slitter head consists of multiple sets of circular blades or rotary knives. These blades are precisely engineered and arranged to make clean and accurate cuts along the width of the metal coil. The number of blades and the spacing between them can be adjusted according to the desired width of the final strips. For example, if a manufacturer needs to produce a large number of very narrow strips, more blades with closer spacing will be used. The blades are made from high quality materials, such as hardened steel or carbide, to withstand the high pressure forces and abrasion during the slitting process. They need to be sharp and durable to ensure consistent cut quality over long production runs.
After the metal coil has been slit into smaller strips, a recoiler comes into play. The recoiler winds the individual strips into coils of the desired size. Similar to uncoilers, recoilers can be manual or automatic. Automatic recoilers are equipped with tension control systems. Tension control is crucial because it ensures that the strips are wound evenly and tightly onto the coil. If the tension is too loose, the coils may be unstable and prone to tangling or unravelling. On the other hand, if the tension is too high, it can cause the strips to stretch or deform. The tension control system monitors and adjusts the tension as the strips are being wound, resulting in neatly wound coils that are easy to handle, transport, and use in subsequent manufacturing processes.
During the slitting process, there is often some material on the edges of the coil that is not part of the desired final product. This material, known as trim or scrap, needs to be removed. A scrap winder is an integral part of the slitting line machine that collects and compresses this scrap material. The scrap winder helps to keep the work area clean and organized. Additionally, the compressed scrap can be more easily recycled or disposed of. In many manufacturing facilities, recycling the scrap metal is an important part of reducing waste and minimizing the environmental impact of the production process.
Modern slitting line machines are equipped with advanced computerized control systems. These control systems give operators a high degree of precision and flexibility. Operators can input parameters such as the desired strip width, cutting speed, and tension settings directly into the control panel. The control system then ensures that the machine operates according to these settings, making real time adjustments if necessary. For example, if the operator notices that the strip width is slightly off during production, they can quickly make the adjustment on the control panel, and the machine will automatically correct the slitting process. This level of automation not only improves the accuracy of the slitting process but also increases production efficiency, as the machine can run continuously without the need for frequent manual intervention.
Safety is of utmost importance in the operation of slitting line machines. These machines are designed with multiple safety features. Safety guards are installed around the moving parts, such as the uncoiler, slitter head, and recoiler, to prevent operators from accidentally coming into contact with them. Emergency stop buttons are placed at easily accessible locations on the machine, allowing operators to quickly halt the machine in case of an emergency. Some machines are also equipped with sensors that can detect abnormalities such as jams, overheating, or incorrect material feeding. If such an issue is detected, the machine will automatically stop, and an alarm may be sounded to alert the operator.
Slitting line machines come in a wide variety of sizes and configurations to meet the diverse needs of different industries. Some machines are designed for light duty applications, where they may process thinner and lighter weight metal coils at relatively low speeds. These machines are often used in small scale manufacturing or for producing components that require less material. On the other hand, heavy duty slitting line machines are built to handle thick and heavy metal coils, such as those used in the construction or automotive industries. These heavy duty machines are more robust, with more powerful motors, stronger frames, and larger capacity components to withstand the high forces involved in processing thick metal.
The choice of a slitting line machine depends on several factors. The type and thickness of the metal to be slit are important considerations. Different metals have different properties, such as hardness, ductility, and toughness, which can affect the slitting process. For example, stainless steel is harder to slit than aluminum, so a machine used for stainless steel may need more powerful blades and a stronger drive system. The required strip width also plays a role in determining the machine's configuration. If a manufacturer needs to produce a wide range of strip widths, they may opt for a machine with a more flexible slitter head that allows for easy adjustment of the blade spacing. Production volume is another key factor. High volume production facilities will require machines that can operate at high speeds and have long lasting components to ensure continuous and efficient production.
Proper maintenance of the slitting line machine is essential to ensure its longevity and optimal performance. Regular inspection of the blades is necessary to check for wear and tear. Worn out blades can lead to poor quality cuts, so they need to be sharpened or replaced in a timely manner. The rollers in the straightening and leveling units, as well as those in the uncoiler and recoiler, should be lubricated regularly to reduce friction and prevent premature wear. The control system should also be checked periodically to ensure that it is functioning correctly and that the input parameters are being accurately followed. Operator training is equally important. Well trained operators are more likely to use the machine correctly, follow safety procedures, and identify any potential issues early on, which can help to minimize downtime and maximize the productivity of the slitting line machine.