Hotline
+86-136 8495 9862
Email:cennia@szmizhi.com
Add::104,Building 27,Third Industrial Zone, Longxi Community,Longgang District,Shenzhen,China.
Coil Forming & Handling Equipment
Surface Treatment Equipment
Solutions
Application
About Us
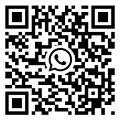
Welcome to MIZHI
For consultation/feedback, please call the service hotline: +86-136 8495 9862 Email:cennia@szmizhi.com
Roofing machines are specialized industrial systems designed to manufacture roof panels, tiles, and sheets from various materials, including steel, aluminum, copper, and composite metals. These machines play a critical role in the construction industry by enabling the production of durable, weatherresistant, and aesthetically versatile roofing solutions. Whether for residential, commercial, or industrial buildings, roofing machines combine speed, precision, and adaptability to meet the diverse demands of modern architecture.
Key Components and Functions
1. Roll Forming Mechanism:
The core of most roofing machines is a roll forming system, which shapes flat metal coils into profiled panels. Rollers are designed to create specific profiles, such as corrugated, standing seam, trapezoidal, or sinusoidal shapes. For example, standing seam roofing machines produce panels with interlocking edges, ideal for watertight commercial roofs, while corrugated machines are popular for agricultural or industrial buildings due to their strength and low cost.
2. Cutting and Punching Stations:
After forming, panels are cut to precise lengths using flying shears or hydraulic cutters, ensuring minimal waste. Some machines include integrated punching systems to add holes for screws, ventilation, or drainage, streamlining the production process.
3. Material Handling Systems:
Uncoilers and levelers prepare the metal strip by unwinding the coil and straightening it to remove any curvature or waviness. Tension control systems ensure consistent feed rates, preventing wrinkles or misalignment during forming.
4. Automation and Control Systems:
Modern roofing machines often feature CNC (computer numerical control) interfaces, allowing operators to program panel dimensions, profiles, and production speeds. Automated systems can switch between different profiles quickly, reducing downtime for changeovers.
Types of Roofing Machines
Standing Seam Roofing Machines:
These machines produce panels with vertical seams that interlock, providing a sleek, modern appearance and superior water resistance. They are widely used in highend residential and commercial projects.
Corrugated Roofing Machines:
Designed to create waveshaped panels, these machines are costeffective and durable, suitable for sheds, warehouses, and lowcost housing. Corrugated profiles offer excellent strength with minimal material usage.
Tile Forming Machines:
Mimicking the look of traditional clay or concrete tiles, these machines produce metal panels with embossed textures, combining the aesthetic appeal of tiles with the durability and lightweight benefits of metal.
Composite Roofing Machines:
These systems laminate metal sheets with insulation or decorative layers, creating energyefficient panels for commercial buildings.
Advantages of Roofing Machines
1. High Efficiency:
Roofing machines can produce up to hundreds of feet of panel per minute, significantly outpacing manual fabrication. Automated systems reduce labor costs and ensure consistent quality.
2. Design Flexibility:
With interchangeable roll sets, a single machine can produce multiple profiles, allowing manufacturers to adapt to various project requirements. Custom profiles can also be designed for unique architectural visions.
3. Material Savings:
Precise cutting and forming minimize scrap, while the use of lightweight metals like aluminum reduces overall material costs without compromising strength.
4. Durability and Sustainability:
Metal roofing produced by these machines is fireresistant, recyclable, and often coated with protective layers (e.g., galvanized, painted) to extend lifespan and reduce maintenance.
Challenges and Considerations
Initial Investment:
Highquality roofing machines require significant upfront costs, especially for automated or multiprofile systems. However, this is offset by longterm productivity and scalability.
Maintenance:
Regular lubrication and inspection of rollers and cutting tools are essential to prevent wear and ensure consistent panel quality. Corrosionresistant coatings on machine components can extend lifespan in humid or coastal environments.
Training:
Operators must be trained to use CNC controls and troubleshoot common issues, such as misalignment or material jams, to maintain optimal performance.
In summary, roofing machines are indispensable tools for the modern construction industry, driving innovation in roofing design and sustainability. Their ability to produce highquality, customized panels at scale makes them a cornerstone of efficient, reliable roofing solutions worldwide.