Hotline
+86-136 8495 9862
Email:cennia@szmizhi.com
Add::104,Building 27,Third Industrial Zone, Longxi Community,Longgang District,Shenzhen,China.
Coil Forming & Handling Equipment
Surface Treatment Equipment
Solutions
Application
About Us
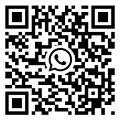
Welcome to MIZHI
For consultation/feedback, please call the service hotline: +86-136 8495 9862 Email:cennia@szmizhi.com
The roll forming process is a highly systematic method for transforming flat metal strips into complex profiles through a series of incremental bending operations. This section outlines the key stages of the process, from material preparation to final finishing, and highlights the technical considerations that ensure accuracy and efficiency.
1. Material Selection and Preparation
The process begins with selecting the appropriate metal coil, typically made of steel, aluminum, copper, or stainless steel. The material’s thickness, yield strength, and ductility are critical factors, as they determine the number of roll stands needed and the risk of cracking during forming. For example, higherstrength metals like advanced highstrength steel (AHSS) require more gradual deformation and robust roll tooling.
Before forming, the coil is loaded onto an uncoiler, which feeds the strip into a leveler to remove any curvature or waviness from the coiling process. Edge conditioning may also occur at this stage, where the strip’s edges are trimmed or deburred to prevent defects like burrs or uneven shaping later in the process.
2. Incremental Forming Through Roll Stands
The core of the roll forming process takes place in the roll stands, where the strip is progressively bent into the target profile. Each pair of rolls (upper and lower) in a stand applies a controlled amount of deformation, with subsequent stands making increasingly larger adjustments. The goal is to distribute the bending stress evenly across the material, minimizing springback (the tendency of metal to revert to its original shape) and ensuring dimensional accuracy.
For example, forming a simple Uchannel may involve:
First stands: Bend the edges slightly upward.
Middle stands: Increase the bend angle and define the flanges.
Final stands: Straighten the flanges and ensure the profile meets specified tolerances.
Complex profiles with multiple bends or intricate features may require dozens of stands, each making subtle adjustments. Computeraided design (CAD) and simulation software are instrumental in optimizing the roll sequence, predicting material flow, and avoiding issues like excessive thinning or necking.
3. Cutting and Finishing
Once the profile is fully formed, it is cut to the desired length using a cutoff tool. Flying shears are commonly used in highspeed lines, allowing continuous production without stopping the strip. After cutting, the parts may undergo additional processes:
Deburring: To remove any sharp edges created during cutting.
Welding: For profiles that require seamless joints, such as pipes or hollow sections.
Surface Treatment: Galvanizing, painting, or powder coating to enhance corrosion resistance and aesthetics.
Quality Inspection: Automated systems may measure dimensions, check for surface defects, or perform tensile tests to ensure compliance with standards.
4. Process Optimization and Challenges
Key factors influencing the roll forming process include:
Roll Design: The shape, spacing, and material of the rollers must be tailored to the profile and material. Poor roll design can lead to uneven deformation or excessive wear.
Speed and Tension: Maintaining consistent feed speed and tension prevents wrinkling or stretching of the strip. Higher speeds increase productivity but may require more robust cooling systems to manage frictiongenerated heat.
Springback Compensation: Engineers must account for the metal’s elastic recovery by overbending the material slightly in the rolls, ensuring the final profile matches specifications.
Tooling Maintenance: Regular inspection and replacement of worn rollers are essential to avoid defects like scratches or dimensional inaccuracies.
5. Advancements in Roll Forming Technology
Modern roll forming processes increasingly integrate automation and smart technologies:
CNC Controls: Allow quick changeovers between different profiles, reducing downtime.
Robotic Integration: Robots can load/unload materials, inspect parts, or perform postforming operations.
IoT and Predictive Maintenance: Sensors monitor machine performance and predict roller wear, enabling proactive maintenance to minimize disruptions.
In summary, the roll forming process is a blend of mechanical precision and material science, delivering highquality profiles with minimal waste and maximum efficiency. Its stepbystep approach, combined with technological advancements, makes it a cornerstone of modern manufacturing for applications ranging from simple brackets to complex automotive structures.