Hotline
+86-136 8495 9862
Email:cennia@szmizhi.com
Add::104,Building 27,Third Industrial Zone, Longxi Community,Longgang District,Shenzhen,China.
Coil Forming & Handling Equipment
Surface Treatment Equipment
Solutions
Application
About Us
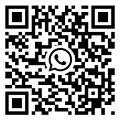
Welcome to MIZHI
For consultation/feedback, please call the service hotline: +86-136 8495 9862 Email:cennia@szmizhi.com
Roll forming equipment is the backbone of the cold roll forming process, consisting of a series of integrated components designed to feed, shape, and finish metal strips into specific profiles. This machinery is highly customizable, ranging from simple manual systems for low-volume production to advanced automated lines for high-speed industrial applications. Understanding the key components of roll forming equipment is essential for optimizing efficiency and product quality.
1. Uncoiler: The process begins with an uncoiler, which holds the metal coil and feeds the strip into the roll forming machine at a controlled speed. Modern uncoilers may include tension control systems to prevent wrinkling or misalignment, ensuring a smooth start to the forming process.
2. Leveler: Before shaping, the metal strip must be flattened to remove any coil set or waviness. The leveler uses multiple rollers to straighten the material, ensuring consistent thickness and flatness. This step is critical for achieving accurate profile dimensions later in the process.
3. Roll Stands: The heart of the roll forming equipment, roll stands house the forming rollers that gradually bend the metal into the desired shape. Each stand contains a pair of upper and lower rollers, with successive stands progressively modifying the profile. The number of stands depends on the complexity of the profile; simple shapes may require 4–6 stands, while intricate designs can need 12 or more. Rollers are typically made from hardened steel or tool steel to withstand the high pressures and friction involved, and their surfaces may be coated (e.g., with tungsten carbide) for durability.
4. Guiding and Sensing Systems: To maintain precision, guiding rollers or side guides ensure the strip stays centered as it moves through the stands. Sensors may be integrated to monitor speed, tension, and dimensional accuracy in real time, allowing for automatic adjustments to correct deviations.
5. Cut-off Tool: After forming, the continuous strip is cut into individual lengths using a cut-off tool, which can be a flying shear (operates while the strip is moving) or a stationary shear (cuts after the strip stops). Flying shears are preferred for high-speed production to minimize downtime.
6. Runout Table and Stacker: The finished profiles are conveyed to a runout table, where they cool (if heat was applied, though rare in cold roll forming) and are then stacked or bundled for shipment. Automated stackers can sort and package parts according to size or order specifications.
Additional components may include edge conditioning units (to deburr or trim the strip edges), pre-punching stations (for adding holes or notches before forming), and post-forming operations like welding, painting, or galvanizing. Advanced roll forming lines may also incorporate robotics for loading/unloading, CNC controls for rapid tooling changes, and predictive maintenance systems to monitor roller wear and machine performance.
The design of roll forming equipment is highly application-specific. For example, automotive lines may prioritize speed and precision for producing uniform parts, while construction equipment may focus on handling thicker gauge metals and larger profiles. Proper maintenance of the equipment, including regular cleaning, lubrication, and roller inspection, is essential to ensure long lifespan and consistent product quality.
In summary, roll forming equipment is a sophisticated assembly of components that work in tandem to transform raw metal coils into precision-engineered profiles. Its adaptability and scalability make it a vital asset in modern manufacturing across diverse industries.