Hotline
+86-136 8495 9862
Email:cennia@szmizhi.com
Add::104,Building 27,Third Industrial Zone, Longxi Community,Longgang District,Shenzhen,China.
Coil Forming & Handling Equipment
Surface Treatment Equipment
Solutions
Application
About Us
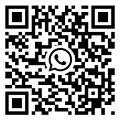
Welcome to MIZHI
For consultation/feedback, please call the service hotline: +86-136 8495 9862 Email:cennia@szmizhi.com
A metal cut to length (CTL) line is a comprehensive industrial solution designed to convert coiled metal into flat, precut sheets or strips of precise dimensions. This versatile equipment is essential for industries ranging from automotive to construction, where consistent, highquality metal blanks are critical for downstream manufacturing. By combining uncoiling, leveling, cutting, and stacking into a single automated process, metal CTL lines optimize material usage and reduce labor costs while delivering unmatched precision.
Core Processes in a Metal CTL Line
1. Uncoiling and Tension Control:
The metal coil is loaded onto an uncoiler, which releases the strip at a controlled speed while maintaining consistent tension. This prevents sagging or wrinkling, ensuring smooth feeding into the leveling section. Hydraulic or pneumatic tension systems are often used for heavygauge metals to avoid stretching or damage.
2. Leveling for Surface Perfection:
The leveling process is critical for eliminating coil set and improving flatness. Multiroll levelers with adjustable roller spacing and pressure can handle various metal properties:
For ductile metals (e.g., aluminum): Gentle leveling preserves surface finish.
For highstrength steel: Heavyduty levelers with hardened steel rollers apply more force to straighten rigid materials.
Advanced systems may include automatic leveling adjustments based on material thickness or feedback from laser measurement devices.
3. Precision Cutting Options:
Metal CTL lines offer multiple cutting technologies:
Guillotine Shears: Ideal for thick metals (up to 20 mm), guillotine shears produce clean, burrfree cuts at a fixed length. They are slower than flying shears but excel in precision and heavyduty applications.
Flying Shears: These move in sync with the moving strip, enabling continuous cutting at high speeds (up to 300 feet per minute). They are suitable for thin to mediumgauge metals and highvolume production.
Plasma/Laser Cutting: For complex geometries or holes, plasma or laser cutters can trim sheets to nonrectangular shapes while maintaining length accuracy, though at a higher cost.
4. Stacking and Packaging:
After cutting, sheets are conveyed to a stacker, which aligns them neatly by size or batch. Automated stackers may include:
Weight sensors: To limit stack height and prevent damage.
Vacuum or magnetic grippers: For gentle handling of thin or delicate sheets.
Strapping or wrapping systems: To secure stacks for shipping, reducing damage during transit.
Material Versatility
Metal CTL lines can process a wide range of materials:
Ferrous Metals: Carbon steel, stainless steel, galvanized steel, and alloy steel.
NonFerrous Metals: Aluminum, copper, brass, nickel, and titanium.
Coated Metals: Prepainted steel, galvalume, or zinccoated sheets, requiring special care to preserve surface finishes during processing.
For example, in the appliance industry, a CTL line may process thingauge stainless steel coils into sheets for refrigerator doors, using gentle leveling and flying shears to avoid scratching the prepolished surface. In contrast, a steel fabrication plant might use a heavyduty CTL line with guillotine shears to cut 10 mm thick steel plates for structural beams.
Advantages of Metal CTL Lines
1. Unmatched Precision:
Tolerances as tight as ±0.1 mm for length and ±0.05 mm for flatness ensure that each sheet meets strict specifications, reducing rework and waste in downstream processes like stamping or welding.
2. Scalability and Speed:
Highspeed lines with flying shears can produce thousands of sheets per hour, making them ideal for largescale manufacturing. Modular designs allow for easy upgrades, such as adding an edge trimmer or automated quality control system as production needs grow.
3. Cost Efficiency:
By optimizing coil usage (minimizing tail and head waste) and eliminating manual cutting, CTL lines reduce material costs by up to 15%. Labor costs are also minimized through automation, with some lines requiring only one operator for monitoring.