Hotline
+86-136 8495 9862
Email:cennia@szmizhi.com
Add::104,Building 27,Third Industrial Zone, Longxi Community,Longgang District,Shenzhen,China.
Coil Forming & Handling Equipment
Surface Treatment Equipment
Solutions
Application
About Us
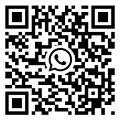
Welcome to MIZHI
For consultation/feedback, please call the service hotline: +86-136 8495 9862 Email:cennia@szmizhi.com
A cut to length (CTL) line is a specialized industrial system designed to cut metal coils into precise, uniform lengths, serving as a critical component in metal processing industries. These lines are highly sought after for their ability to transform raw coils into flat, precut sheets or strips, reducing waste and enhancing efficiency in downstream manufacturing processes. For businesses seeking to invest in CTL lines, understanding their components, applications, and purchasing considerations is essential.
Key Components of a Cut to Length Line
1. Uncoiler:
The line starts with an uncoiler, which holds the metal coil and feeds it into the system at a controlled rate. Hydraulic or motordriven uncoilers can handle coils ranging from lightweight aluminum to heavyduty steel, with capacities often ranging from 5 to 30 tons.
2. Leveler:
A precision leveler removes coil set (permanent curvature from coiling) and ensures the metal strip is flat and free of waves or wrinkles. Multiroll levelers with adjustable pressure settings can handle various material thicknesses, from thin foils to thick plates.
3. Edge Trimmers (Optional):
Some CTL lines include side trimmers to shear off uneven edges or burrs, producing strips with parallel, clean edges. This is particularly useful for applications requiring precise widths, such as stamping or roll forming.
4. Cutting System:
The heart of the CTL line is the cutting system, which can be:
Guillotine Shear: Uses a stationary lower blade and a moving upper blade to cut the strip at a fixed length. Ideal for thick materials and highprecision cuts.
Flying Shear: Cuts the moving strip without stopping the line, enabling continuous production at high speeds. Common in highvolume operations.
Plasma or Laser Cutter: For advanced applications, such as cutting complex shapes or holes in the sheet while maintaining length precision.
5. Stacker and Runout Table:
After cutting, sheets are conveyed to a stacker, which neatly piles them according to size or order. Automated stackers may include sorting features, barcode labeling, or packaging systems for efficient logistics.
6. Control System:
A PLC (programmable logic controller) or CNC interface allows operators to set sheet length, feed speed, and cutting parameters. Modern systems offer touchscreen interfaces, realtime production monitoring, and data logging for quality control and process optimization.
Applications of Cut to Length Lines
CTL lines are indispensable in industries where precise metal sheets are required, including:
Automotive Manufacturing: Producing body panels, floor pans, and structural components from precut steel or aluminum sheets.
Aerospace and Defense: Cutting highstrength alloys into precise blanks for aircraft parts or military equipment.
Construction and Fabrication: Processing steel or aluminum into sheets for roofing, siding, or structural beams.
Appliance and Electronics: Cutting thingauge stainless steel or copper for appliance casings or electronic enclosures.
Benefits of Investing in a Cut to Length Line
1. Precision and Consistency:
CTL lines achieve length tolerances as tight as ±0.5 mm, ensuring uniform parts that reduce waste in downstream processes like stamping or welding.
2. Increased Productivity:
Automated lines can process coils at speeds up to 200 feet per minute, significantly outperforming manual cutting methods. Flying shears enable continuous operation, minimizing downtime.
3. Material Versatility:
CTL lines can handle a wide range of metals, including steel, aluminum, copper, brass, and even exotic alloys like titanium or nickel. Adjustable levelers and cutting tools accommodate thicknesses from 0.1 mm to 12 mm or more.
4. Cost Savings:
By optimizing material usage (minimizing scrap from overcutting) and reducing labor costs, CTL lines offer a strong return on investment (ROI), especially for highvolume producers.
Purchasing Considerations
Material Type and Thickness:
Ensure the line is rated for your target materials (e.g., heavy steel vs. lightweight aluminum) and thickness range. Upgrading to a more robust leveler or shear may be necessary for futureproofing.
Production Volume and Speed:
Highspeed lines with flying shears are ideal for largescale production, while smaller guillotine shear lines may suffice for lowtomedium volumes.
Automation Level:
Semiautomated lines are suitable for small shops, while fully automated systems with robotic stacking and IoT connectivity are better for large enterprises seeking Industry 4.0 integration.
AfterSales Support:
Look for suppliers offering installation, training, and maintenance services. Spare parts availability and technical support are crucial for minimizing downtime.
Market Trends and Innovations
Modern CTL lines are increasingly integrating advanced features like:
Laser Measurement Systems: For realtime feedback on sheet length and flatness.
EnergyEfficient Motors: Reducing power consumption by up to 30%.
QuickChange Tooling: Enabling faster transitions between material types or sheet sizes.
In summary, a cut to length line is a strategic investment for any metal processing business aiming to enhance precision, productivity, and profitability. By selecting a system tailored to their specific needs, manufacturers can streamline operations and gain a competitive edge in today’s demanding market.