Hotline
+86-136 8495 9862
Email:cennia@szmizhi.com
Add::104,Building 27,Third Industrial Zone, Longxi Community,Longgang District,Shenzhen,China.
Coil Forming & Handling Equipment
Surface Treatment Equipment
Solutions
Application
About Us
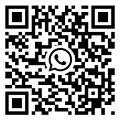
Welcome to MIZHI
For consultation/feedback, please call the service hotline: +86-136 8495 9862 Email:cennia@szmizhi.com
Cold roll forming is a versatile and efficient metalworking process that transforms flat metal strips into custom profiles through a series of consecutive rolling stands. Unlike hot forming, which involves heating the material, cold roll forming operates at room temperature, preserving the metal’s mechanical properties while achieving precise dimensions and consistent shapes. This process is widely used in industries such as automotive, construction, aerospace, and appliance manufacturing to produce components like structural beams, pipes, channels, and automotive parts.
The core principle of cold roll forming lies in gradual deformation. The metal strip is fed through multiple pairs of rollers (roll stands), each designed to incrementally bend and shape the material into the desired profile. Each roll stand makes a small, controlled adjustment to the strip’s geometry, reducing stress and minimizing the risk of cracking or distortion. This incremental approach allows for the production of complex cross-sections, including those with intricate flanges, lips, or stiffening ribs. For example, in automotive manufacturing, cold roll forming is used to create chassis components, door frames, and seat structures, where strength and dimensional accuracy are critical.
One of the primary advantages of cold roll forming is its high production speed and efficiency. Once the roll tooling is set up, the process can run continuously, producing long lengths of uniform profiles at rates up to hundreds of feet per minute. This makes it ideal for high-volume manufacturing, significantly reducing costs compared to alternative methods like extrusion or stamping, especially for long components. Additionally, cold working enhances the metal’s strength through work hardening, making the final product more durable without additional heat treatment.
However, cold roll forming requires precise tooling design and setup. The initial investment in roll dies can be substantial, particularly for complex profiles, but this is offset by low per-unit production costs over large quantities. The process is most suitable for ductile metals like steel, aluminum, copper, and stainless steel, as brittle materials may crack under the applied stresses. Maintenance of the roll dies is also critical to ensure consistent quality, as wear can lead to dimensional variations or surface defects.
In recent years, advancements in computer-aided design (CAD) and simulation software have revolutionized cold roll forming. Engineers can now use finite element analysis (FEA) to model the deformation process, optimize roll sequences, and predict potential issues like springback or material thinning before physical tooling is created. This reduces trial-and-error costs and speeds up the prototyping phase. As sustainability gains importance, cold roll forming’s low material waste (minimal scrap compared to cutting processes) and energy efficiency further solidify its role in modern manufacturing.
In summary, cold roll forming combines precision, efficiency, and material savings to deliver high-quality metal profiles at scale. Its ability to produce complex shapes with minimal post-processing makes it a cornerstone of modern industrial fabrication.