Hotline
+86-136 8495 9862
Email:cennia@szmizhi.com
Add::104,Building 27,Third Industrial Zone, Longxi Community,Longgang District,Shenzhen,China.
Coil Forming & Handling Equipment
Surface Treatment Equipment
Solutions
Application
About Us
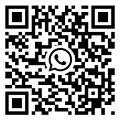
Welcome to MIZHI
For consultation/feedback, please call the service hotline: +86-136 8495 9862 Email:cennia@szmizhi.com
Coil cut to length is a manufacturing process that involves transforming continuous coils of various materials, typically metals like steel, aluminum, and copper, into individual flat sheets of precise lengths. This process is widely utilized across numerous industries due to its ability to provide customized and accurately sized material for specific applications.
The coil cut to length process begins with the coil being loaded onto a specialized machine, usually an uncoiler. The uncoiler gradually unwinds the coil, feeding the material into the cut to length system. As the material advances, it first passes through a leveling mechanism. The leveling process is crucial as it straightens out any bends, curls, or irregularities present in the coiled material, ensuring that the final cut sheets are flat and of consistent quality. This is particularly important for applications where flatness is a critical factor, such as in the production of metal panels for construction or automotive body parts.
After leveling, the material proceeds to the cutting stage. The cutting operation is highly precise, thanks to advanced measurement and control systems. Measuring devices, such as laser sensors or digital encoders, accurately determine the length of the material as it moves through the machine. Based on the pre set length parameters entered by the operator, the control system signals the cutting mechanism to make the appropriate cuts. Common cutting methods include shearing, where sharp blades shear through the material, and plasma cutting, which uses a high temperature plasma arc to melt and cut through thicker or more difficult to cut materials.
One of the significant advantages of the coil cut to length process is its flexibility. Manufacturers can produce sheets of various lengths according to the specific requirements of their projects. This customization eliminates the need for excessive material waste that may occur when using standard sized sheets and then trimming them down. For example, in the appliance manufacturing industry, different models may require metal sheets of specific lengths for components like refrigerator doors or washing machine casings. Coil cut to length allows for the production of these exact sized sheets, optimizing material usage and reducing costs.
The coil cut to length process also offers high volume production capabilities. Modern cut to length machines are highly automated and can process coils at high speeds while maintaining accuracy. This makes it suitable for industries that require large quantities of cut to length material, such as the construction industry, where significant amounts of steel sheets are needed for building structures. Additionally, the automation of the process reduces the reliance on manual labor, increasing production efficiency and consistency.
Quality control is an integral part of the coil cut to length process. Regular checks are carried out to ensure that the cut sheets meet the specified length tolerances, flatness requirements, and edge quality. Any deviations from the standards can be quickly identified and corrected, either by adjusting the machine settings or by replacing worn out components. For instance, if the cutting blades become dull, they may produce rough or uneven edges on the cut sheets, and replacing them promptly helps maintain the quality of the final product.
In recent years, advancements in technology have further enhanced the capabilities of coil cut to length systems. Newer machines are equipped with intelligent control systems that can monitor and adjust the process in real time, optimizing performance and reducing the occurrence of errors. Integration with enterprise resource planning (ERP) systems also allows for better management of production schedules, inventory levels, and material flow, making the entire coil cut to length process more efficient and responsive to market demands.