Hotline
+86-136 8495 9862
Email:cennia@szmizhi.com
Add::104,Building 27,Third Industrial Zone, Longxi Community,Longgang District,Shenzhen,China.
Coil Forming & Handling Equipment
Surface Treatment Equipment
Solutions
Application
About Us
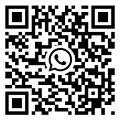
Welcome to MIZHI
For consultation/feedback, please call the service hotline: +86-136 8495 9862 Email:cennia@szmizhi.com
Precision sand blasting machines redefine surface preparation by enabling highly controlled, accurate material removal for applications that demand meticulous detail. Unlike general-purpose blasters that provide broad coverage, precision models are engineered to deliver consistent abrasive flow, precise pressure control, and specialized nozzles, making them essential in industries such as aerospace, electronics, jewelry manufacturing, and medical device production—where even minor surface imperfections can affect functionality or aesthetics.
The core of a precision sand blaster lies in its ability to regulate key parameters with micron-level accuracy. This includes adjustable air pressure (often down to 5 PSI increments), controlled abrasive flow rates, and specialized nozzle designs (such as narrow-tip or angled nozzles) that focus the blast stream to a specific area. For example, in semiconductor manufacturing, precision blasters are used to etch tiny patterns on silicon wafers without damaging adjacent components, requiring blasting zones as small as 0.1 millimeters. Digital control panels allow operators to input and store precise settings for repeatable results, ensuring consistency across multiple parts.
Another critical feature is the machine’s stability and vibration control. Precision blasting often occurs on delicate or small components, so these machines are built with rigid frames and anti-vibration mounts to prevent movement that could compromise accuracy. Some models incorporate robotic arms or CNC (computer numerical control) systems, enabling automated blasting along programmed paths with sub-millimeter precision. This is particularly useful in aerospace, where turbine blades or engine components require uniform surface treatment without altering their aerodynamic profiles.
Environmental controls also play a role in precision blasting. Cleanroom-compatible models are designed to operate in dust-free environments, using HEPA filtration and sealed chambers to prevent contamination. The use of fine abrasives, such as glass beads or aluminum oxide micro-particles, allows for gentle yet precise material removal, ideal for finishing delicate surfaces like jewelry or medical implants. As industries continue to demand higher levels of precision and consistency, these machines have become indispensable for tasks that require a balance of power and delicacy, ensuring that surface preparation meets the most rigorous quality standards while minimizing material waste and rework.