Hotline
+86-136 8495 9862
Email:cennia@szmizhi.com
Add::104,Building 27,Third Industrial Zone, Longxi Community,Longgang District,Shenzhen,China.
Coil Forming & Handling Equipment
Surface Treatment Equipment
Solutions
Application
About Us
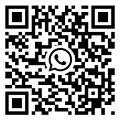
Welcome to MIZHI
For consultation/feedback, please call the service hotline: +86-136 8495 9862 Email:cennia@szmizhi.com
Programmable blasting machines redefine the landscape of explosive operations by allowing users to customize detonation parameters through flexible software interfaces. Unlike fixed-function machines, these devices feature programmable logic controllers (PLCs) or digital control panels that enable operators to input specific timing sequences, charge configurations, and safety protocols for each blasting scenario. This level of customization is crucial in industries where geological conditions, project requirements, and safety regulations vary significantly, such as mining, civil engineering, and military demolitions.
The programmability of these machines lies in their ability to store and execute multiple blasting patterns. For instance, a mining engineer can design different programs for soft sedimentary rock versus hard granite, adjusting the delay between charges to optimize fragmentation. Each program can specify parameters like the number of detonators, firing order, millisecond delays, and even energy output levels. Some advanced models allow real-time modification of programs on-site, enabling quick adjustments based on unexpected geological findings. This flexibility reduces the need for multiple specialized machines, lowering costs and enhancing operational efficiency.
Safety features in programmable blasting machines are often integrated into the programming interface. For example, the software may include built-in checks to ensure that the number of connected detonators matches the programmed sequence, or it may enforce minimum safety distances before allowing activation. Password-protected access prevents unauthorized changes to critical settings, and audit trails record all program modifications for compliance and accountability. Additionally, programmable machines can interface with external systems, such as seismic monitoring devices, to automatically adjust blast parameters and minimize environmental impact. As Industry 4.0 technologies advance, these machines are increasingly compatible with IoT platforms, allowing remote programming and real-time data analysis to further optimize blasting operations. The ability to tailor each blast through programming has made these machines indispensable for projects that demand precision, adaptability, and compliance with complex safety standards.