Hotline
+86-136 8495 9862
Email:cennia@szmizhi.com
Add::104,Building 27,Third Industrial Zone, Longxi Community,Longgang District,Shenzhen,China.
Coil Forming & Handling Equipment
Surface Treatment Equipment
Solutions
Application
About Us
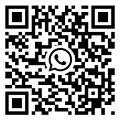
Welcome to MIZHI
For consultation/feedback, please call the service hotline: +86-136 8495 9862 Email:cennia@szmizhi.com
Drilling and blasting machines for tunnels are specialized equipment designed to excavate underground passages efficiently while maintaining structural integrity and safety. These machines combine drilling rigs and blasting systems to create precise boreholes for explosive charges, enabling controlled rock fragmentation in confined spaces. Tunnel excavation demands high precision to avoid over excavation, which can compromise stability, or under excavation, which requires costly rework.
Multi boom drilling rigs are a core component of tunnel blasting systems. These rigs feature multiple hydraulic arms (booms) that can simultaneously drill multiple boreholes in the tunnel face. Each boom is equipped with a rotary drill that penetrates rock, with adjustable angles and depths to create a pattern optimized for blasting. For example, in a highway tunnel project, the rig might drill hundreds of holes in a specific pattern to ensure the rock face fractures uniformly, minimizing irregularities in the tunnel profile.
Blasting pattern design is critical for tunnel excavation. Engineers use software to model the placement, depth, and charge size of each borehole, considering factors like rock hardness, jointing, and desired tunnel shape. The blasting machine must execute this pattern with precision, as even minor deviations can lead to unstable tunnel walls or excessive rock debris. Modern machines often integrate GPS or laser guidance systems to ensure each borehole is drilled to the exact coordinates specified in the design.
Safety and efficiency are further enhanced by automated charging systems. These systems insert explosive charges into the boreholes with minimal human intervention, reducing the risk of accidents. Additionally, tunnel blasting machines may include features like dust suppression systems to control airborne particles and ventilation ducts to expel fumes after detonation. Post blasting, the machine may also be equipped with sensors to monitor rock stability, ensuring it is safe for crews to enter and remove debris. As tunnel projects become more complex—such as those for high speed railways or deep sea crossings—drilling and blasting machines continue to evolve with advanced automation and data analytics to optimize performance and safety.