Hotline
+86-136 8495 9862
Email:cennia@szmizhi.com
Add::104,Building 27,Third Industrial Zone, Longxi Community,Longgang District,Shenzhen,China.
Coil Forming & Handling Equipment
Surface Treatment Equipment
Solutions
Application
About Us
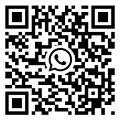
Welcome to MIZHI
For consultation/feedback, please call the service hotline: +86-136 8495 9862 Email:cennia@szmizhi.com
Blasting machines for rock breaking are specialized equipment designed to fracture and fragment rock formations in mining, construction, and civil engineering projects. These machines utilize explosive energy or mechanical force to break down large rock masses into manageable pieces, enabling efficient excavation and material extraction. The technology combines precision engineering with powerful mechanisms to ensure safety, accuracy, and cost effectiveness in challenging terrains.
Explosive based rock breaking machines rely on controlled detonations to fracture rock. These systems involve drilling boreholes into the rock, inserting explosive charges, and triggering detonations with blasting caps or electronic initiation systems. The design of the machine must account for factors like charge placement, blast timing, and shockwave propagation to minimize collateral damage and maximize rock fragmentation. For example, in open pit mining, large scale blasting machines can break down entire rock faces in a single operation, allowing excavators to remove material efficiently.
Mechanical rock breakers, alternatively, use hydraulic or pneumatic forces to crack rock. These machines feature a chisel tipped hammer that delivers high impact blows to the rock surface, gradually causing it to fracture. Hydraulic breakers, often mounted on excavators, are popular in urban construction where explosive blasting is impractical due to noise or safety concerns. Their precision allows operators to target specific areas without damaging nearby structures, making them ideal for tunnel excavation or foundation work.
Safety features are paramount in rock breaking machines. Explosive systems include fail safe ignition mechanisms and remote detonation capabilities to keep operators at a safe distance. Mechanical breakers incorporate vibration dampening designs to reduce operator fatigue and prevent equipment damage. Additionally, modern machines often integrate digital controls for precise blast parameter adjustments, such as charge size and detonation sequence, ensuring consistent results and minimizing over breaking (which wastes material) or under breaking (which requires rework). As environmental regulations tighten, rock breaking machines are also evolving to reduce noise, dust, and vibration, making them more sustainable for future projects.