Hotline
+86-136 8495 9862
Email:cennia@szmizhi.com
Add::104,Building 27,Third Industrial Zone, Longxi Community,Longgang District,Shenzhen,China.
Coil Forming & Handling Equipment
Surface Treatment Equipment
Solutions
Application
About Us
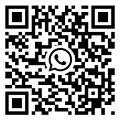
Welcome to MIZHI
For consultation/feedback, please call the service hotline: +86-136 8495 9862 Email:cennia@szmizhi.com
Proper installation ensures a sand blasting machine operates safely and efficiently. This guide covers key steps for different machine types:
1. Site Selection and Preparation
Environment: Choose a well ventilated area with minimal dust accumulation. For industrial use, install the machine in a dedicated blasting booth or room with fire resistant walls.
Space Requirements:
Portable machines: Allow 3–5 feet of clearance around the unit for access and mobility.
Cabinet machines: Ensure ceiling height is 2–3 feet taller than the cabinet to accommodate exhaust ducts.
Flooring: Use a non slip, easy to clean surface (e.g., concrete or epoxy coated flooring). For outdoor installations, use a covered area to protect the machine from rain and debris.
2. Unpacking and Assembly
Inspect Components: Check the shipment for damaged parts (e.g., cracked chambers, bent nozzles). Reference the parts list in the manual to ensure all items are present (e.g., blasting gun, hoses, filters).
Assemble the Frame: For cabinet style machines, attach the legs or base to the chamber using provided bolts. Tighten evenly to prevent wobbling.
Install Dust Collection System:
Connect ductwork from the machine’s exhaust port to the dust collector. Use airtight clamps and seal joints with silicone to prevent leaks.
Position the dust collector outside the work area or in a ventilated room to minimize indoor air pollution.
3. Electrical and Pneumatic Connections
Electrical Setup:
For machines with electrical components (e.g., dust collector motors), connect to a grounded circuit with the specified voltage (e.g., 110V or 220V). Hire a licensed electrician for 3 phase power connections.
Install a dedicated circuit breaker for the machine to prevent overloads.
Air Compressor Connection:
Choose a compressor with sufficient CFM (cubic feet per minute) for the machine’s requirements (e.g., 10–15 CFM for a small cabinet, 20–30 CFM for a large industrial unit).
Use reinforced air hoses rated for the maximum working pressure (e.g., 150 PSI). Install a moisture trap and pressure regulator near the machine to protect against condensation and control airflow.
4. Calibration and Testing
Pressure Testing:
Turn on the compressor and set the regulator to the machine’s minimum operating pressure (e.g., 60 PSI). Spray soapy water on all connections to check for bubbles, which indicate leaks. Tighten or replace faulty parts.
Media Flow Test:
Fill the hopper with a small amount of abrasive media. Trigger the blasting gun into a safe container and verify consistent, non sputtering flow. Adjust the media control valve if flow is inconsistent.
Dust Collection Efficiency:
Run the dust collector and hold a piece of paper near the exhaust duct—if it sticks, the suction is adequate. If not, check filter installation or fan speed.
5. Safety and Compliance Checks
Emergency Stops: Ensure all emergency stop buttons are accessible and function correctly. Test them by pressing and verifying the machine shuts down immediately.
Ventilation Compliance: For indoor installations, confirm the dust collection system meets local OSHA or environmental standards (e.g., capturing 99% of respirable particles).
Grounding: Connect the machine’s frame to a grounding rod using a 10 gauge wire to prevent static electricity buildup, which can cause sparks or explosions with flammable media.
6. Final Adjustments and Training
Operator Training: Provide comprehensive training on machine operation, safety protocols, and basic maintenance. Ensure operators are familiar with the manual and emergency procedures.
Record Keeping: Maintain installation records, including wiring diagrams, component specifications, and test results, for future reference and compliance audits.