Hotline
+86-136 8495 9862
Email:cennia@szmizhi.com
Add::104,Building 27,Third Industrial Zone, Longxi Community,Longgang District,Shenzhen,China.
Coil Forming & Handling Equipment
Surface Treatment Equipment
Solutions
Application
About Us
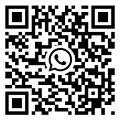
Welcome to MIZHI
For consultation/feedback, please call the service hotline: +86-136 8495 9862 Email:cennia@szmizhi.com
When a sand blasting machine malfunctions, systematic troubleshooting can identify issues quickly. Below are common problems and solutions:
Inadequate Blasting Pressure
Possible Causes:
Low air compressor output (e.g., faulty motor, clogged intake filter).
Leaky hoses, connectors, or valves.
Blocked abrasive media flow (e.g., clogged hopper or nozzle).
Solutions:
Verify the compressor pressure gauge reads 90–120 PSI. Replace filters or repair the compressor if pressure is low.
Spray soapy water on hoses and connections to detect leaks; replace damaged parts.
Empty the hopper, clean debris, and ensure the media valve is fully open. Check the nozzle for obstructions (e.g., caked media or rust).
Inconsistent Abrasive Flow
Possible Causes:
Moisture clogged media (e.g., damp sand or beads).
Worn out media control valve or siphon tube.
Incorrect media size (too large for the nozzle).
Solutions:
Dry the abrasive media or replace it with a moisture free batch. Install a desiccant dryer in the air line to prevent future moisture buildup.
Disassemble the valve and siphon tube; clean or replace components with signs of wear.
Use abrasive media recommended by the manufacturer (e.g., 80 grit aluminum oxide for a 1/4" nozzle).
Excessive Dust in the Work Area
Possible Causes:
Faulty dust collector (e.g., clogged filters, dead motor).
Leaks in the blasting chamber or hoses.
Inadequate negative pressure in cabinet style machines.
Solutions:
Replace dust collector filters and ensure the motor is operational. Check ductwork for blockages.
Inspect the chamber seals, gloves, and viewing windows for gaps. Tighten or replace seals as needed.
Adjust the dust collector fan speed or install a booster fan to maintain proper airflow.
Noisy Operation or Unusual Vibrations
Possible Causes:
Loose components (e.g., unsecured motor, vibrating hoses).
Worn out bearings in the compressor or fan.
Imbalanced wheels on portable machines.
Solutions:
Tighten bolts and brackets on the machine frame. Secure hoses with clamps to reduce vibration.
Replace damaged bearings and lubricate moving parts (e.g., fan shafts) according to the manual.
Balance or replace wheels on portable units to ensure smooth movement.
Safety System Failures
Possible Causes:
Tripped circuit breakers or blown fuses in electrical systems.
Malfunctioning emergency stop switches or interlocks.
Solutions:
Reset breakers or replace fuses; check wiring for shorts or loose connections.
Test safety switches with a multimeter; replace any that fail continuity tests.