Hotline
+86-136 8495 9862
Email:cennia@szmizhi.com
Add::104,Building 27,Third Industrial Zone, Longxi Community,Longgang District,Shenzhen,China.
Coil Forming & Handling Equipment
Surface Treatment Equipment
Solutions
Application
About Us
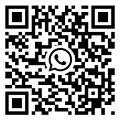
Welcome to MIZHI
For consultation/feedback, please call the service hotline: +86-136 8495 9862 Email:cennia@szmizhi.com
Regular maintenance is critical to ensuring the longevity, efficiency, and safety of sand blasting machines. Proper upkeep minimizes downtime, reduces repair costs, and prevents performance degradation. Here’s a comprehensive guide to maintaining different types of sand blasting equipment:
Daily/Weekly Maintenance
1. Clean the Machine Interior: After each use, remove residual abrasive media, dust, and debris from the blasting chamber, hopper, and hoses. Use a vacuum or compressed air to prevent clogs and ensure smooth media flow.
2. Inspect Hoses and Connections: Check for cracks, leaks, or wear in air hoses, blasting hoses, and quick connectors. Tighten loose fittings to avoid air pressure loss, which can affect blasting performance.
3. Nozzle Wear Check: The blasting nozzle is prone to abrasion. Examine the nozzle tip for enlargement or uneven wear—if the diameter exceeds the manufacturer’s specifications (e.g., 1/8" to 3/16"), replace it to maintain blasting pressure and precision.
4. Air Compressor Maintenance: Drain moisture from the air receiver tank daily to prevent rust and corrosion. Replace air filters and lubricate moving parts as per the compressor manual.
Monthly/Quarterly Maintenance
1. Check Safety Components: Test emergency stop buttons, interlocks, and pressure gauges to ensure they function correctly. Verify that safety shields and protective barriers are intact.
2. Abrasive Media Quality: Inspect the abrasive material for contamination (e.g., moisture, foreign particles). Replace media if it appears clumped or degraded, as low quality media can damage the machine and compromise surface finishes.
3. Valve and Regulator Calibration: Adjust pressure regulators to maintain optimal blasting pressure (typically 80–120 PSI). Clean or replace pressure relief valves if they show signs of sticking or leaking.
4. Dust Collection System: Clean or replace dust filters to maintain efficient air extraction. A clogged filter reduces visibility in the blasting chamber and increases the risk of dust exposure.
Annual Maintenance
1. Comprehensive Component Overhaul: Disassemble the blasting gun, hopper, and valves to remove accumulated debris and rust. Replace worn seals, gaskets, and O rings to prevent air leaks.
2. Electrical System Inspection: Check wiring for fraying or loose connections, especially in automated or power driven components. Test sensors and control panels for accuracy.
3. Structural Integrity Check: Inspect the machine’s frame and chamber for cracks or corrosion, particularly in areas exposed to abrasive impact. Weld or replace damaged parts to maintain structural stability.
4. Professional Servicing: Schedule annual maintenance with a certified technician to calibrate pressure systems, perform deep cleaning, and address complex issues (e.g., motor or pump repairs).
Special Considerations
Portable Machines: Regularly check wheels and handles for damage to ensure mobility. Lubricate moving parts (e.g., casters) to prevent stiffness.
Cabinet Style Machines: Clean viewing windows with anti static solutions to maintain visibility. Replace worn gloves or arm holes in the cabinet to prevent dust leakage.