Hotline
+86-136 8495 9862
Email:cennia@szmizhi.com
Add::104,Building 27,Third Industrial Zone, Longxi Community,Longgang District,Shenzhen,China.
Coil Forming & Handling Equipment
Surface Treatment Equipment
Solutions
Application
About Us
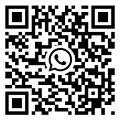
Welcome to MIZHI
For consultation/feedback, please call the service hotline: +86-136 8495 9862 Email:cennia@szmizhi.com
Carbide nozzles are essential components of sand blasting machines, known for their exceptional durability and performance. These nozzles are made from tungsten carbide, a compound composed of tungsten and carbon, which exhibits remarkable hardness and resistance to wear. In sand blasting operations, the nozzle is subjected to high velocity abrasive particles, making its durability a critical factor in the efficiency and cost effectiveness of the process.
The primary function of a carbide nozzle is to accelerate and direct the abrasive material onto the surface being treated. The design of the nozzle, including its shape and internal diameter, plays a crucial role in determining the velocity, spread pattern, and concentration of the abrasive stream. Carbide nozzles are available in various shapes, such as straight, Venturi, and convergent divergent, each designed to optimize different aspects of the blasting process. For example, Venturi nozzles are known for their ability to increase the velocity of the abrasive particles, resulting in more efficient material removal.
One of the key advantages of carbide nozzles is their extended lifespan compared to nozzles made from other materials. The hardness of tungsten carbide allows it to withstand the erosive forces of the abrasive particles for a much longer time, reducing the frequency of nozzle replacements. This not only saves on replacement costs but also minimizes downtime associated with changing nozzles. Additionally, carbide nozzles maintain their shape and internal dimensions more consistently over time, ensuring a stable and predictable blasting performance. However, carbide nozzles are generally more expensive upfront than other types of nozzles, such as those made of ceramic or rubber. Despite the higher initial cost, their long term durability often makes them a cost effective choice for high volume or continuous sand blasting operations.