Hotline
+86-136 8495 9862
Email:cennia@szmizhi.com
Add::104,Building 27,Third Industrial Zone, Longxi Community,Longgang District,Shenzhen,China.
Coil Forming & Handling Equipment
Surface Treatment Equipment
Solutions
Application
About Us
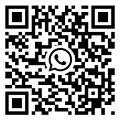
Welcome to MIZHI
For consultation/feedback, please call the service hotline: +86-136 8495 9862 Email:cennia@szmizhi.com
1.Name:Glass Bead Sand Blaster
2.Model:MS
3.Operation Way: Manual
A glass bead blasting machine is a type of surface treatment equipment that uses compressed air to propel small glass beads at high speed onto the surface of a workpiece. This process is designed to clean, polish, and prepare surfaces without causing significant damage or altering the dimensions of the workpiece. The glass beads used are typically made from high-quality materials, such as soda-lime glass, and are characterized by their smooth, spherical shape and uniform size.
Working Principle
The working principle of a glass bead blasting machine involves the following steps:
1.Media Supply: The machine uses a media supply system to deliver glass beads into the blasting chamber. These beads are carefully selected for their uniformity and smoothness to ensure consistent surface treatment.
2.Air Pressure Generation: A compressor provides the necessary compressed air, which is then directed through a nozzle. The pressure can be adjusted to control the speed and force of the glass beads.
3.Surface Treatment: The glass beads are propelled at high velocity towards the workpiece surface. Upon impact, they create a smooth, even texture without causing significant abrasion.
4.Collection and Recycling: After the beads have impacted the surface, they are collected and can often be recycled for future use, making the process cost-effective and environmentally friendly.
Main Applications
Glass bead blasting machines are widely used across various industries for the following purposes:
Surface Cleaning: Removing contaminants, rust, and old coatings from metal surfaces without causing damage.
Surface Preparation: Preparing surfaces for painting or coating by creating a uniform texture that enhances adhesion.
Polishing and Finishing: Achieving a smooth, satin-like finish on metal, plastic, and glass surfaces.
Deburring and Edge Blending: Removing sharp edges and burrs from machined parts.
Anti-Fatigue Treatment: Increasing the fatigue strength of metal components by creating a compressive stress layer on the surface.
Detailed Advantages
1.Smooth Surface Finish
Glass bead blasting creates a uniform, smooth surface finish that is ideal for applications where a high-quality aesthetic is required. For example, in the automotive industry, glass bead blasting is often used to prepare the surface of car parts before painting to ensure a smooth, even coat of paint.
2.Non-Erosive Process
Unlike more abrasive blasting methods, glass bead blasting is a non-erosive process. This means it does not significantly alter the dimensions of the workpiece, making it suitable for precision work. This is particularly important in industries such as aerospace, where the dimensions of components must be exact.
3.Versatility
Glass bead blasting can be used on a wide range of materials, including metals, plastics, and glass. This versatility makes it a popular choice for manufacturers who need to treat different types of materials with the same equipment.
4.Environmental and Health Benefits
The use of glass beads reduces the environmental impact of the blasting process, as these beads can be recycled multiple times. Additionally, the lower dust generation associated with glass bead blasting reduces health risks for operators, making it a safer option for workers.
5.Cost Efficiency
Glass beads can be reused multiple times, which reduces the operational costs associated with abrasive blasting. This cost efficiency is particularly beneficial for large-scale industrial applications where the frequency of use is high.
In conclusion, glass bead blasting machines offer a versatile, cost-effective, and environmentally friendly solution for surface treatment. Their ability to create a smooth, even finish without altering the dimensions of the workpiece makes them a preferred choice for many industries. By considering the specific requirements of your project and choosing the right equipment, you can achieve high-quality results while minimizing environmental impact and operational costs.
Advantages Over Other Types of Blasting Machines
Aspect | Glass Bead Blasting | Other Types of Blasting (e.g., Sand Blasting) |
Surface Finish | Leaves a smooth, satin-like finish without altering the dimensions of the workpiece. | May leave a rougher surface and can alter the dimensions of the workpiece. |
Material Compatibility | Suitable for a wide range of materials, including metals, plastics, and glass. | May be less suitable for delicate or heat-sensitive materials. |
Environmental Impact | Uses recyclable glass beads, reducing waste and environmental impact. | May generate more dust and waste, requiring additional dust collection systems. |
Health and Safety | Lower risk of respiratory issues due to the use of glass beads instead of more abrasive materials. | Higher risk of dust inhalation and associated health issues. |
Cost-Effectiveness | Glass beads can be reused multiple times, reducing operational costs. | Higher costs due to the need for frequent replacement of abrasive materials. |