Hotline
+86-136 8495 9862
Email:cennia@szmizhi.com
Add::104,Building 27,Third Industrial Zone, Longxi Community,Longgang District,Shenzhen,China.
Coil Forming & Handling Equipment
Surface Treatment Equipment
Solutions
Application
About Us
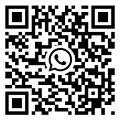
Welcome to MIZHI
For consultation/feedback, please call the service hotline: +86-136 8495 9862 Email:cennia@szmizhi.com
What is Hanger Shot Blast Machine?
A Hanger Shot Blast Machine is an industrial device designed to clean, descale, and prepare the surfaces of various workpieces by propelling abrasive media (such as steel shot or grit) at high speed. This type of machine is particularly useful for treating medium to large-sized components, especially those with irregular shapes or fragile surfaces that require careful handling. It is widely used in industries such as automotive, aerospace, construction, shipbuilding, and metalworking.
Key Features and Components
1.Main Blast Cabinet:
The blast cabinet is the enclosed chamber where the shot blasting process takes place. It is designed to contain the abrasive media and prevent dust from escaping into the environment.
2.Rotating Hooks:
Workpieces are suspended from rotating hooks that move through the blast chamber. These hooks can rotate 360 degrees, ensuring that all surfaces of the workpiece are exposed to the abrasive media.
3.Blast Wheels or Nozzles:
High-efficiency blast wheels or nozzles propel the abrasive media at high speed onto the workpiece surface, effectively removing rust, scale, and other contaminants.
4.Abrasive Circulation System:
The machine includes a bucket elevator, screw conveyor, and separator to recycle and clean the abrasive media. This reduces waste and lowers operational costs.
5.Dust Collection System:
An integrated dust collection system captures and filters dust generated during the blasting process, ensuring environmental compliance.
6.Control System:
Equipped with a PLC (Programmable Logic Controller) system for precise control over the blasting process, including conveyor speed, blast intensity, and other parameters.
Working Principle
l Loading: Workpieces are suspended from rotating hooks and placed in the work area of the machine.
l Rotation: The hooks begin to rotate, exposing all angles of the workpiece surface to the shot blasting process.
l Shot Blasting: High-speed rotating blast wheels propel abrasive particles onto the workpiece surface, removing rust, scale, and other impurities.
l Recovery and Reuse: Used abrasive particles are collected, screened, and cleaned for reuse.
l Unloading: After the cleaning cycle is complete, the workpieces are unloaded and inspected.
Technical Parameters
l Workpiece Capacity: Up to 10,000 kg or more, depending on the model.
l Blast Wheels: Typically 2-6 blast wheels, each with a power rating of 11-15 kW.
l Abrasive Flow Rate: Ranges from 200 kg/min to 600 kg/min per blast wheel.
l Conveyor Speed: Adjustable from 0.5 m/min to 5 m/min.
l Surface Finish: Achieves a high-quality surface finish suitable for further processing such as painting or coating.
Applications
l Automotive: Cleaning and preparing engine parts, chassis components, and other large metal parts.
l Aerospace: Surface treatment of aircraft components to remove corrosion and prepare surfaces for coating.
l Construction: Cleaning and preparing structural steel components for welding or painting.
l Shipbuilding: Removing rust and scale from large steel plates and structural components.
l Metalworking: Surface treatment of castings, forgings, and welded structures.
Benefits
l High Efficiency: Continuous operation and automated process ensure high production rates and consistent results.
l Versatility: Suitable for a wide range of workpiece sizes and shapes.
l Environmental Protection: Enclosed system and dust collection minimize environmental impact.
l Customization: Machines can be tailored to meet specific requirements, including workpiece size and production capacity.
Conclusion
The Hanger Shot Blast Machine is an essential tool for industries requiring high-quality surface treatment of large and complex components. Its versatility, efficiency, and environmental protection features make it a valuable investment for any manufacturing facility.