Hotline
+86-136 8495 9862
Email:cennia@szmizhi.com
Add::104,Building 27,Third Industrial Zone, Longxi Community,Longgang District,Shenzhen,China.
Coil Forming & Handling Equipment
Surface Treatment Equipment
Solutions
Application
About Us
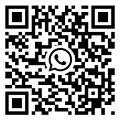
Welcome to MIZHI
For consultation/feedback, please call the service hotline: +86-136 8495 9862 Email:cennia@szmizhi.com
Inline slitters are a type of slitting equipment that offers significant advantages in terms of efficiency and integration within manufacturing processes. Unlike standalone slitting machines, inline slitters are designed to be incorporated directly into an existing production line, allowing for seamless and continuous processing of materials, typically metal coils or sheets, without the need for intermediate handling or storage steps.
The key characteristic of inline slitters is their ability to perform the slitting operation while the material is in motion, as it moves along the production line. This eliminates the time consuming process of stopping the material flow, loading it onto a separate slitting machine, and then reintroducing it to the production line. As a result, inline slitters can greatly enhance the overall productivity of the manufacturing process, reducing production lead times and increasing throughput.
Inline slitters are highly versatile and can be customized to meet the specific requirements of different production lines and materials. They can handle a wide range of materials, including steel, aluminum, copper, and various alloys, as well as different coil or sheet widths and thicknesses. For example, in the automotive manufacturing industry, inline slitters can be integrated into the production line for manufacturing body panels. Here, they can slit large coils of steel into narrower strips of the exact width required for each panel, ensuring a continuous supply of precisely sized material for subsequent stamping and forming operations.
The design of inline slitters typically includes several key components. The uncoiling section is responsible for feeding the material into the slitter. It is designed to unwind the coil smoothly and maintain a consistent tension in the material as it moves forward. The slitting mechanism, which is the core of the inline slitter, uses sharp cutting blades to make the necessary cuts. These blades are often adjustable to achieve different slit widths, and they are driven by powerful motors to ensure fast and accurate cutting. After slitting, the slit strips are then typically guided through a series of rollers or conveyors to the next stage of the production line.
One of the major benefits of inline slitters is their ability to work in harmony with other equipment on the production line. They can be synchronized with upstream and downstream processes, such as rolling mills, presses, or coating machines. For instance, in a steel production facility, an inline slitter can be integrated after the rolling mill to immediately slit the freshly rolled coils into smaller, more manageable widths, which can then be directly fed into a coating machine for surface treatment. This integration not only streamlines the production process but also reduces the risk of material damage or contamination that may occur during multiple handling and transfer operations.
Inline slitters also often feature advanced control systems. These systems use sensors and automation technology to monitor and control various aspects of the slitting process, such as the speed of the material, the position of the cutting blades, and the tension in the strips. The control system can make real time adjustments to ensure that the slitting operation is carried out with high precision and that the slit strips meet the required quality standards. Additionally, some inline slitters can be programmed to perform different slitting patterns or sequences, providing flexibility in production to meet the diverse needs of customers.
Maintenance of inline slitters is also an important consideration. Since they are part of a continuous production line, minimizing downtime for maintenance is crucial. Inline slitters are typically designed with easy access components and modular designs, which facilitate quick inspection, cleaning, and replacement of parts. Regular maintenance, including blade sharpening, lubrication of moving parts, and calibration of sensors, helps to ensure the long term reliability and optimal performance of the inline slitter, keeping the production line running smoothly and efficiently.