Hotline
+86-136 8495 9862
Email:cennia@szmizhi.com
Add::104,Building 27,Third Industrial Zone, Longxi Community,Longgang District,Shenzhen,China.
Coil Forming & Handling Equipment
Surface Treatment Equipment
Solutions
Application
About Us
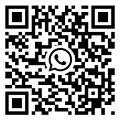
Welcome to MIZHI
For consultation/feedback, please call the service hotline: +86-136 8495 9862 Email:cennia@szmizhi.com
An HR (Hot Rolled) coil slitting machine is a specialized industrial apparatus designed to handle the unique challenges associated with slitting hot rolled steel coils. Hot rolled steel, which is produced by rolling steel at high temperatures, is widely used in various applications due to its high strength and relatively lower cost compared to cold rolled steel. However, its properties, such as a rougher surface finish and higher thickness variability, require specific features and capabilities in the slitting machine.
The operation of an HR coil slitting machine begins with the careful loading of the hot rolled coil onto an appropriate uncoiler. Given the weight and size of hot rolled coils, which can be substantial, the uncoiler is often designed with robust construction and hydraulic or mechanical systems to ensure smooth and controlled unwinding. The uncoiler must also be able to handle the inherent irregularities in hot rolled coils, such as slight variations in thickness and shape, without causing damage to the coil or disrupting the slitting process.
Once the coil is being fed from the uncoiler, the hot rolled steel strip typically passes through a series of pre slitting preparations. One of the important steps is leveling. Since hot rolled steel may have significant camber, crook, or waviness due to the hot rolling process, the leveling unit in the HR coil slitting machine is crucial. It uses multiple sets of rollers with precisely adjusted pressure to straighten the strip, bringing it to a more uniform and flat state. This not only improves the accuracy of the subsequent slitting but also helps in preventing issues like uneven cutting forces and blade wear.
The slitting mechanism in an HR coil slitting machine is engineered to withstand the tough nature of hot rolled steel. The slitting blades are made from high wear resistant materials, such as high carbon high chromium tool steels or carbide tipped blades. These blades are designed to cut through the relatively thick and hard hot rolled steel with minimal deformation and long lasting sharpness. The blade arrangement and alignment are also carefully calibrated to ensure clean and accurate cuts, even when dealing with variations in the steel's hardness and thickness across the coil.
Tension control is another critical aspect of an HR coil slitting machine. Hot rolled steel strips can be more prone to stretching or sagging during the slitting process due to their material properties. The tension control system in the machine monitors and adjusts the tension of the strip in real time. It ensures that the strip remains taut enough to be cut accurately but not so tight as to cause excessive stretching or damage. This is achieved through a combination of sensors, motors, and control algorithms that work together to maintain the optimal tension level throughout the slitting operation.
In addition to the basic slitting functionality, HR coil slitting machines may incorporate features to handle the edge trim produced during the slitting process. Edge trim, which consists of the excess material removed from the sides of the hot rolled strip, can be quite substantial. Some machines are equipped with scrap choppers or winders that collect and process the edge trim, either by cutting it into smaller pieces for easier disposal or winding it into manageable coils for recycling.
Modern HR coil slitting machines also often come with advanced control systems. These systems allow operators to input parameters such as the desired slit width, coil dimensions, and production speed. The control system then automatically adjusts the various components of the machine, including the uncoiler speed, leveling roller settings, and blade position, to achieve the specified requirements. Additionally, these systems can provide real time monitoring and diagnostic functions, enabling operators to quickly identify and address any issues that may arise during the slitting process, thereby minimizing downtime and maximizing productivity.